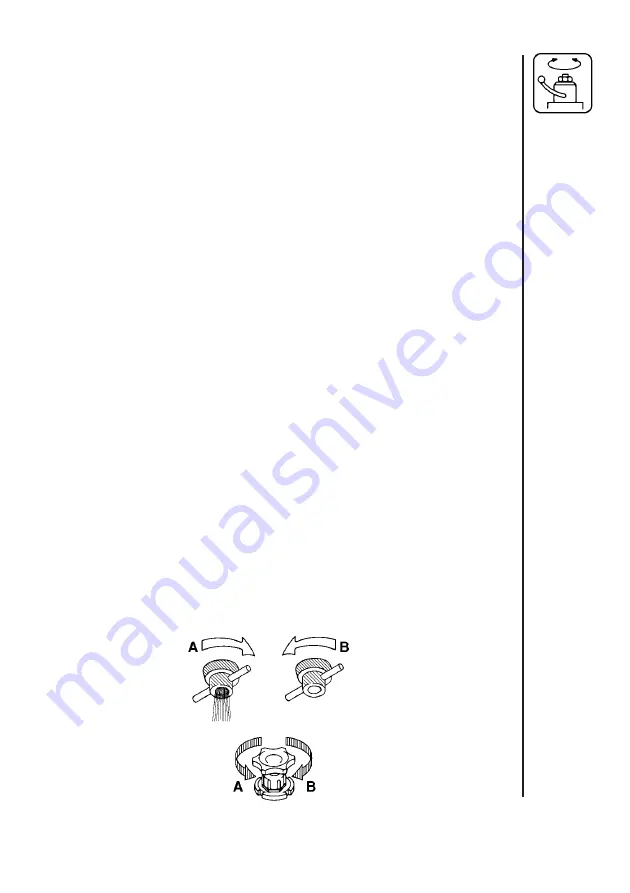
11
Adjust the HARDI-MATIC valve 6 so that the pressure gauge indicates
the recommended pressure.
ADJUST THE PRESSURE EQUALIZATION SECTIONS AS FOL-
LOWS:
7. Note the pressure and place the first lever 3 on the distribution valve
in position B (off position).
8. Turn the corresponding adjust screw 5 until the pressure gauge
again shows the same pressure (turn the screw clockwise for higher
pressure, anti-clockwise for lower pressure).
9. Adjust the other sections of the distribution valve in the same way.
NB: HEREAFTER ADJUSTMENT OF PRESSURE EQUALIZATION
WILL ONLY BE NEEDED IF YOU CHANGE TO NOZZLES WITH
OTHER CAPACITIES.
10. Operating the control unit while driving:
To close the entire boom, turn the handle 2 to position B. This takes
the pressure off the pump. The liquid will then return to the tank via the
return system. The diaphragm anti-drip valves ensure instantaneous
closing of all nozzles. In order to close part of the boom, move lever 3
of the distribution valve to position B (off position) for the section or
sections to be closed. The pressure equalization device ensures that
the pressure does not rise in the sections which are to remain open.
Drain valve operation
Pressure filter
The operating unit has an in-built pressure filter. It is not necessary to
dismantle the filter to clean it. When cleaning the sprayer (clean water
circulating in the tank), open the drain valve to flush the filter;
To open
: A
To close
: B
Tank drain
To open
: A
To close
: B
Summary of Contents for LX-MB Series
Page 14: ...1 X 40 1 X 40 2 A X 12 B X 40 3 X 20 14 20 6 10 11 22...
Page 15: ...15 4 X 40 5 X 40 6 X 40 7 X 40 MB MB MB MB 19 9 18 18...
Page 16: ...16 8 X 40 9 A X 40 B X 40 10 A X 40 B X 40 A A A A B B B B B HB HB 19 9 19 HB A A A B B...
Page 17: ...17 11 X 40 12 A X 40 B X 40 HB HB 19 18 B A A...
Page 21: ...21 Model 1302 Model 361...
Page 30: ......
Page 31: ......
Page 32: ......
Page 33: ......
Page 34: ......
Page 35: ......
Page 36: ......
Page 37: ......
Page 38: ......
Page 39: ......
Page 40: ......
Page 41: ......
Page 42: ......
Page 43: ......
Page 44: ......
Page 45: ......
Page 46: ......
Page 47: ......
Page 48: ...32 Notes 48...