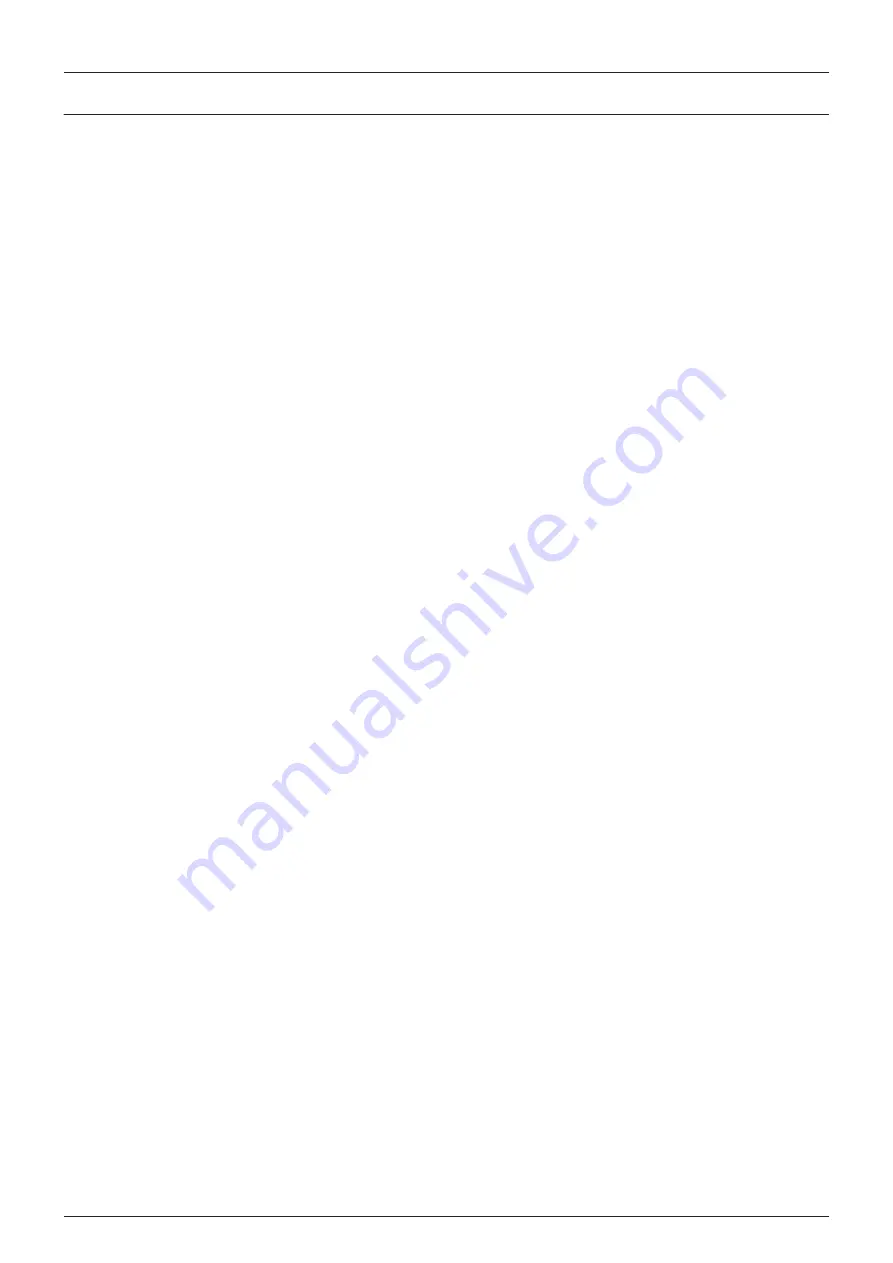
65
7 - Fault finding
Operational problems
General info
Operational incidents are frequently due to the same reasons:
1.
A suction leakage reduces the pump pressure and may interrupt suction completely.
2.
A clogged suction filter may damage suction or interrupt and prevent the pump from running normally.
3.
A clogged pressure filter increases pressure in the fluid system in front of the pressure filter. This may blow the safety
valve.
4.
Clogged In-line or nozzle filters increase pressure in the pressure gauge but decrease pressure at the nozzles.
5.
Impurities sucked by the pump may prevent the valves from closing correctly, thus reducing the pump flow.
6.
A bad reassembly of the pump elements, especially the diaphragm covers, causes air intakes or leaks and reduces the
pump flow.
7.
Rusted or dirty hydraulic components cause bad connections and early wears.
8.
A badly charged or faulty battery causes failures and misbehaviour in the electrical system.
Therefore ALWAYS check
1.
Suction and pressure filters, as well as nozzles, are clean.
2.
Hoses for leaks and cracks, paying particular attention to suction hoses.
3.
Gaskets and O-rings are present and in good condition.
4.
Pressure gauge is in good working order. Dosage accuracy depends on it.
5.
Operating unit functions properly. Use clean water to check.
6.
Hydraulic components are clean.
7.
The good condition of the tractor battery and its connectors.
Summary of Contents for MASTER PRO VHH
Page 6: ...Table of Contents 6 ...
Page 8: ...1 EC Declaration 8 ...
Page 12: ...2 Safety notes 12 ...
Page 50: ...5 Operation 50 ...
Page 52: ...6 Maintenance 52 Boom lubrication oiling plan Lift lubrication oiling plan ...
Page 70: ...7 Fault finding 70 ...
Page 76: ...8 Technical specifications 76 Charts Boom hydraulic Z ...
Page 78: ...8 Technical specifications 78 ...
Page 82: ...HARDI INTERNATIONAL A S Helgeshøj Allé 38 DK 2630 Taastrup DENMARK ...