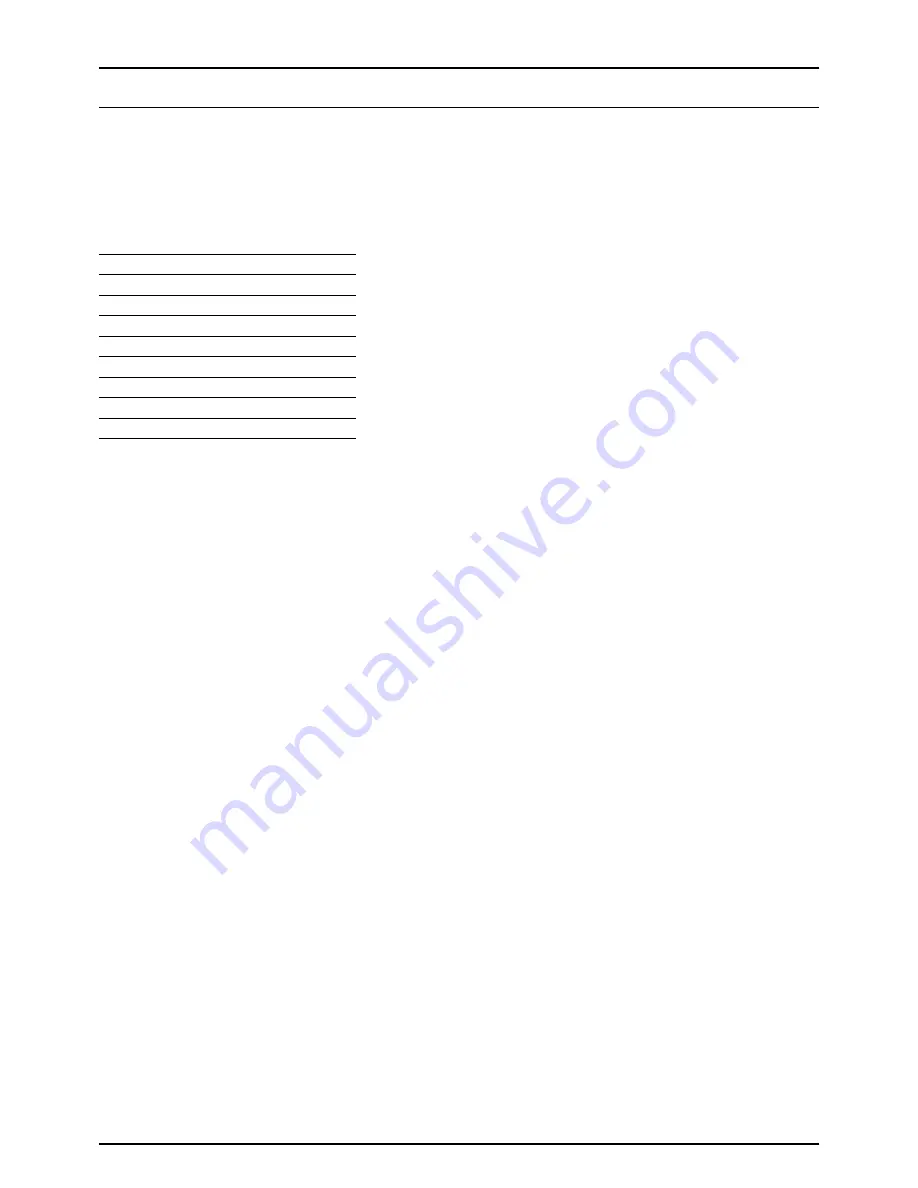
8 - Technical specifications
107
Materials and Recycling
Disposal of the Sprayer
When the equipment has completed its working life, it must be thoroughly cleaned. The tank, hoses and synthetic fittings
can be incinerated at an authorized disposal plant. The metallic parts can be scrapped. Always follow local legislation
regarding disposal.
Materials used:
Tanks:
HDPE
Chassis, frame:
Steel
Pump:
Cast iron
Diaphragms:
PUR
Hoses (suction):
PVC
Hoses (pressure):
EPDM
Valves:
Glass reinforced PA
Filters:
PP
Nozzles:
Unfilled POM
Fittings:
Glass reinforced PA
Summary of Contents for NAVIGATOR FORCE
Page 4: ...1 EU Declaration 4 ...
Page 12: ...2 Safety Notes 12 ...
Page 54: ...4 Sprayer setup 54 ...
Page 76: ...6 Maintenance 76 Boom lubrication oiling plan ...
Page 112: ...8 Technical specifications 112 ...
Page 116: ...Index 116 ...
Page 118: ...HARDI INTERNATIONAL A S Herthadalvej 10 DK 4840 Nørre Alslev DENMARK ...