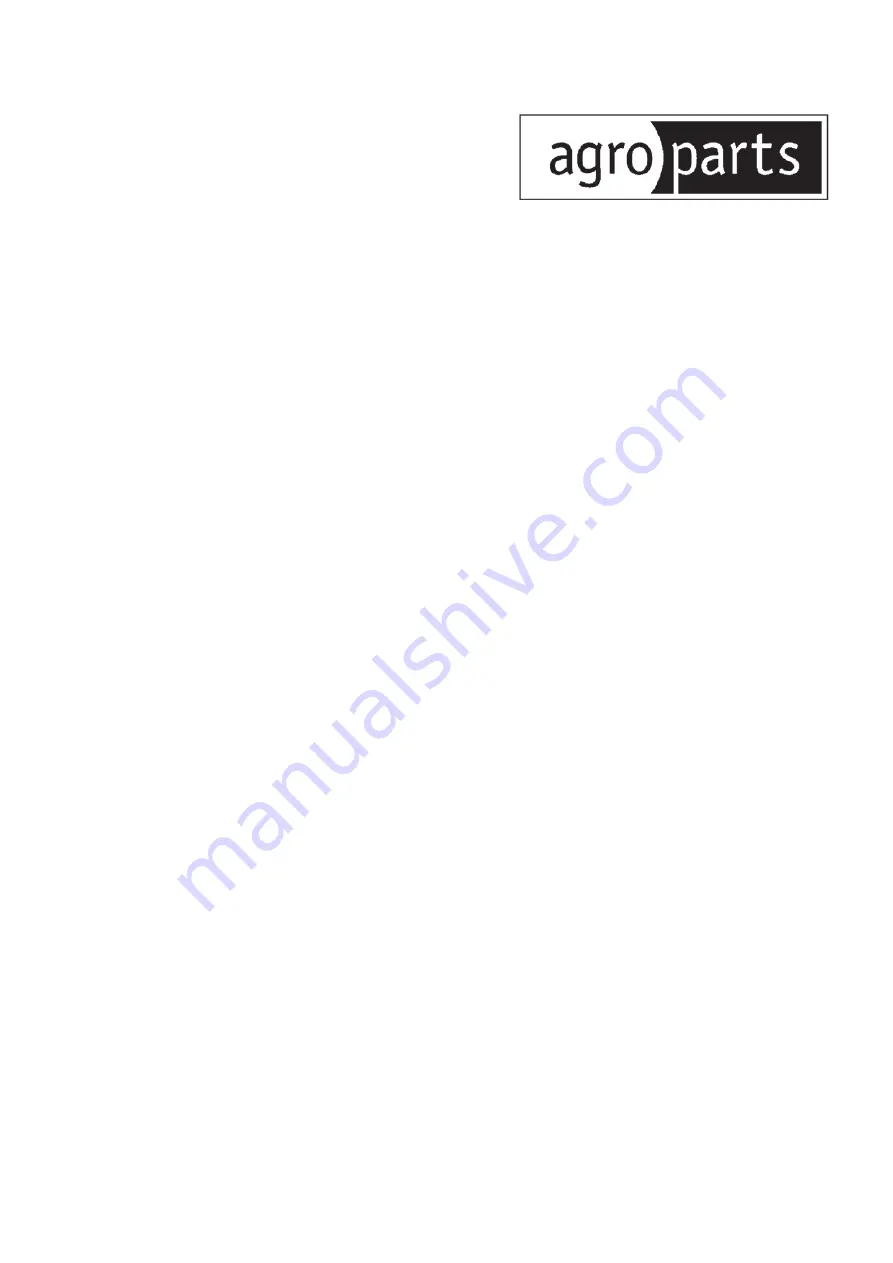
Spare Parts
To see updated spare part information, visit the Agroparts website.
Here all parts information can be accessed in the spare parts catalogue:
1.
Go to www.agroparts.com, register for free and log in.
2.
Select “HARDI” in the menu on the left.
3.
Select “Spare parts catalogue” and find your spare part.
4.
Online ordering is also possible.
5.
Contact your HARDI dealer for further information on spare parts.
Summary of Contents for NK MB Series
Page 8: ...1 Identification 8 ...
Page 52: ...3 Description 52 ...
Page 62: ...4 Sprayer Setup 62 ...
Page 84: ...5 Operation 84 ...
Page 87: ...6 Maintenance 87 Boom Lubrication Oiling Plan Lift Lubrication Oiling Plan ...
Page 116: ...9 EC Declaration 116 ...
Page 120: ...Index 120 ...
Page 122: ...HARDI INTERNATIONAL A S Helgeshøj Allé 38 DK 2630 Taastrup DENMARK ...