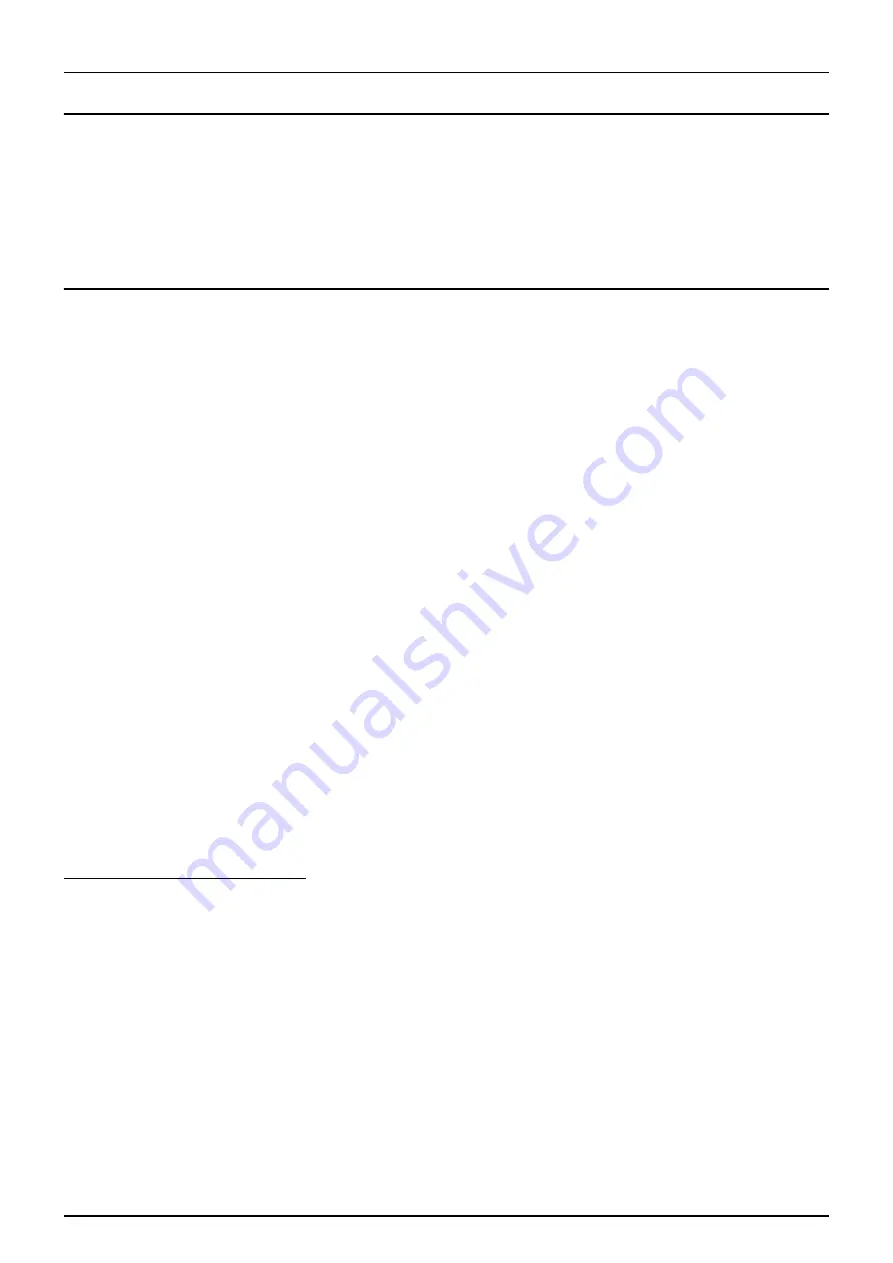
9
2 - General Safety Instructions
Obligations and Liability
Comply with the Instruction Book
Knowledge of the basic safety information and safety regulations is a fundamental requirement for safe handling and fault-
free sprayer operation.
Lack
of knowledge or non-compliance of the safety instructions can lead to injuries and fatal accidents
as well as damage to the
sprayer and its surroundings.
Follow the safety instructions in this Instruction Book.
Before First Use of the Sprayer
The owner of the sprayer must take note of the following obligations before using the sprayer. These obligations also applies
to the employer or the supervisor of the sprayer operators.
Workplace Assessment
This must be completed to start with. Check your national regulations regarding
•
the content of the workplace assessment
•
the frequency of repeating the workplace assessment.
Worker / Operator Instructions
Only let those people work with, or on the sprayer, who
•
are aware of the basic workplace safety information and accident prevention regulations
•
have been instructed in working with/on the tractor and sprayer and hereby achieving appropriate qualifications
•
have read and understood this Instruction Book.
If you still have queries after reading the Instruction Book, or if something remains unclear after reading it, please contact the
manufacturer or your HARDI dealer.
A worker is hereinafter called an operator. An operator is a person who installs, operates, configures, adjusts, maintains,
cleans, repairs, transports or moves the sprayer.
Use of Work Equipment
Throughout the lifetime of the sprayer, the owner shall take every measure to ensure the safety of the sprayer and its
equipment made available to operators according to European Directive 2009/104/EC – Use of Work Equipment.
Amendments to the directive, as well as subsequent directive versions are to be followed when applicable.
In this directive, the “minimum safety and health requirements for the use of work equipment by workers at work” are
described in full. To guide you in this matter, the issues concerning your work with the sprayer are listed below. However,
HARDI do not accept liability that the issues listed cover the requirements in the directive fully. This responsibility lies with
the owner of the sprayer.
From European Directive 2009/104/EC:
CHAPTER I
GENERAL PROVISIONS
Article 1
Subject matter
1.
This Directive, which is the second individual directive within the meaning of Article 16(1) of Directive 89/391/EEC, lays
down minimum safety and health requirements for the use of work equipment by workers at work, as defined in Article
2.
2.
The provisions of Directive 89/391/EEC are fully applicable to the whole scope referred to in paragraph 1, without
prejudice to more stringent or specific provisions contained in this Directive.
Summary of Contents for NK SB Series
Page 8: ...1 Identification 8...
Page 52: ...3 Description 52...
Page 62: ...4 Sprayer Setup 62...
Page 84: ...5 Operation 84...
Page 87: ...6 Maintenance 87 Boom Lubrication Oiling Plan Lift Lubrication Oiling Plan...
Page 116: ...9 EC Declaration 116...
Page 120: ...Index 120...
Page 122: ...HARDI INTERNATIONAL A S Helgesh j All 38 DK 2630 Taastrup DENMARK...