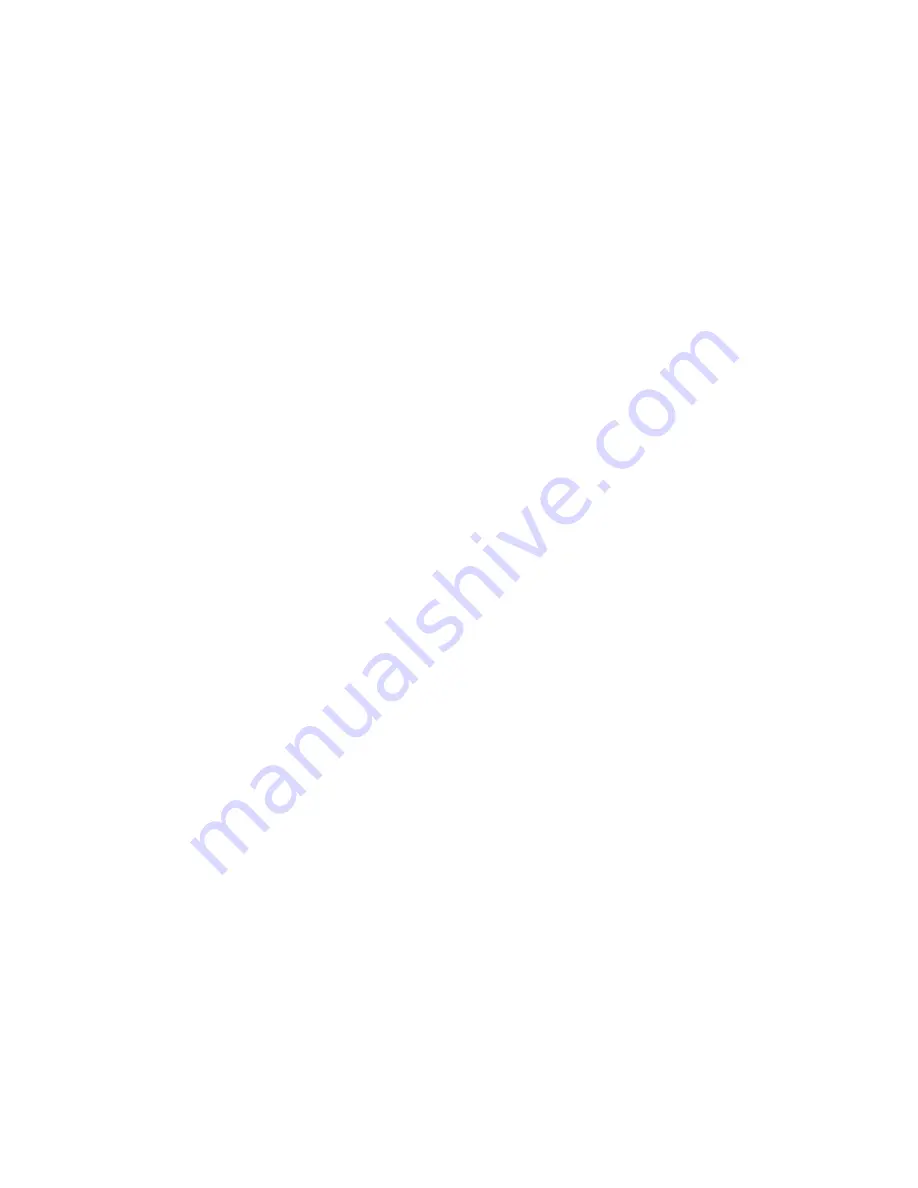
NEVER OPERATE THE MACHINE SPINDLE without a work-holding device if the draw tube is
in the spindle.
TIGHTEN ALL DRAW TUBE SCREWS before beginning spindle operation.
MAKE CERTAIN that the equipment is properly grounded. Consult National Electric Code and
all local codes.
DISCONNECT MAIN ELECTRICAL POWER before attempting repair or maintenance.
ALLOW ONLY AUTHORIZED PERSONNEL to have access to enclosures containing electri-
cal equipment.
DON’T REACH into any control or power case area unless electrical power is OFF.
DON’T TOUCH ELECTRICAL EQUIPMENT when hands are wet or when standing on a wet
surface.
REPLACE BLOWN FUSES with fuses of the same size and type as originally furnished.
ASCERTAIN AND CORRECT the cause of a shutdown caused by overload heaters before
restarting the machine.
KEEP THE AREA AROUND THE MACHINE well lighted and dry.
KEEP CHEMICAL AND FLAMMABLE MATERIAL away from electrical or operating equip-
ment.
HAVE THE CORRECT TYPE OF FIRE EXTINGUISHER handy when machining combustible
material and keep chips clear of the work area.
DON’T USE a toxic or flammable substance as a solvent cleaner or coolant.
MAKE CERTAIN THAT PROPER GUARDING is in place and that all doors are closed and
secured.
TO REMOVE OR REPLACE the chuck closer it is necessary to remove the guard door at the
left end of the machine. Make certain that the guard door is in place before starting the ma-
chine.
DON’T OPEN GUARD DOORS while any machine component is in motion.
MAKE SURE chucks, closers, fixture plates, and all other spindle-mounted work-holding de-
vices are properly mounted and secured before starting the machine.
MAKE CERTAIN all tools are securely clamped in position before starting the machine.
REMOVE ANY LOOSE PARTS OR TOOLS left on machine or in the work area before oper-
ating the machine. Always check the machine and work area for loose tools and parts espe-
cially after work has been completed by maintenance personnel.
REMOVE CHUCK WRENCHES before starting the machine.
BEFORE PRESSING THE CYCLE START PUSH BUTTON, make certain that proper func-
tions are programmed and that all controls are set in the desired modes.
KNOW WHERE ALL stop push buttons are located in case of an emergency.
CHECK THE LUBRICATION OIL LEVEL and the status of the indicator lights before operat-
ing the machine.
ii
M-448B
Summary of Contents for Talent 10/78
Page 9: ... NOTES M 448B vii ...
Page 10: ... NOTES viii M 448B ...
Page 17: ... NOTES M 448B 1 7 ...
Page 18: ... NOTES 1 8 M 448B ...
Page 27: ... NOTES M 448B 2 9 ...
Page 28: ... NOTES 2 10 M 448B ...
Page 32: ... NOTES 3 4 M 448B ...
Page 43: ... NOTES M 448B 4 11 ...
Page 44: ... NOTES 4 12 M 448B ...
Page 49: ... NOTES M 448B 5 5 ...
Page 50: ... NOTES 5 6 M 448B ...
Page 61: ... NOTES M 448B 6 11 ...
Page 62: ... NOTES 6 12 M 448B ...
Page 65: ... NOTES M 448B A1 3 ...
Page 66: ... NOTES A1 4 M 448B ...
Page 68: ...A2 2 M 448B Figure A2 3 Coolant Pump Electrical Connection TALENT 6 45 and 8 52 Lathes TP6027 ...
Page 73: ...M 448B A2 7 Figure A2 10 Tailstock Quill Hydraulic Valves TALENT 8 66 and 10 78 Lathes TP6040 ...
Page 78: ...A2 12 M 448B Figure A2 16 Tailstock Hydraulic Valves TALENT 6 45 and 8 52 Lathes TP5240 ...
Page 79: ...M 448B A2 13 Figure A2 17 Tailstock Hydraulic Valves TALENT 8 66 and 10 78 Lathes TP6045 ...
Page 86: ...A2 20 M 448B Figure A2 24 Internal Power Case View Relay Panel TP5208A ...
Page 91: ...M 448B A2 25 Figure A2 29 Internal Power Case View Service Entrance to Power Case TP5217A ...
Page 92: ...A2 26 M 448B Figure A2 30 Internal Power Case View Fuse and Contactor Panel TP5209A ...
Page 97: ...M 448B A2 31 Figure A2 35 Pump for Through Tool Coolant TP5231 ...
Page 98: ...A2 32 M 448B Figure A2 36 Spindle with Chuck Removed TP5236 ...
Page 99: ...M 448B A2 33 Figure A2 37 Spindle with Chuck Installed TP5243 ...
Page 100: ...A2 34 M 448B Figure A2 38 Tailstock Assembly TALENT 6 45 6 45SV 8 52 and 8 52SV Lathes TP5754 ...
Page 101: ...M 448B A2 35 Figure A2 39 Tailstock Assembly TALENT 8 66 and 10 78 Lathes TP6044 ...
Page 102: ...A2 36 M 448B Figure A2 40 Z Axis Drive Motor TALENT 8 66 and 10 78 Lathes TP6049 ...
Page 103: ... NOTES M 448B A2 37 ...