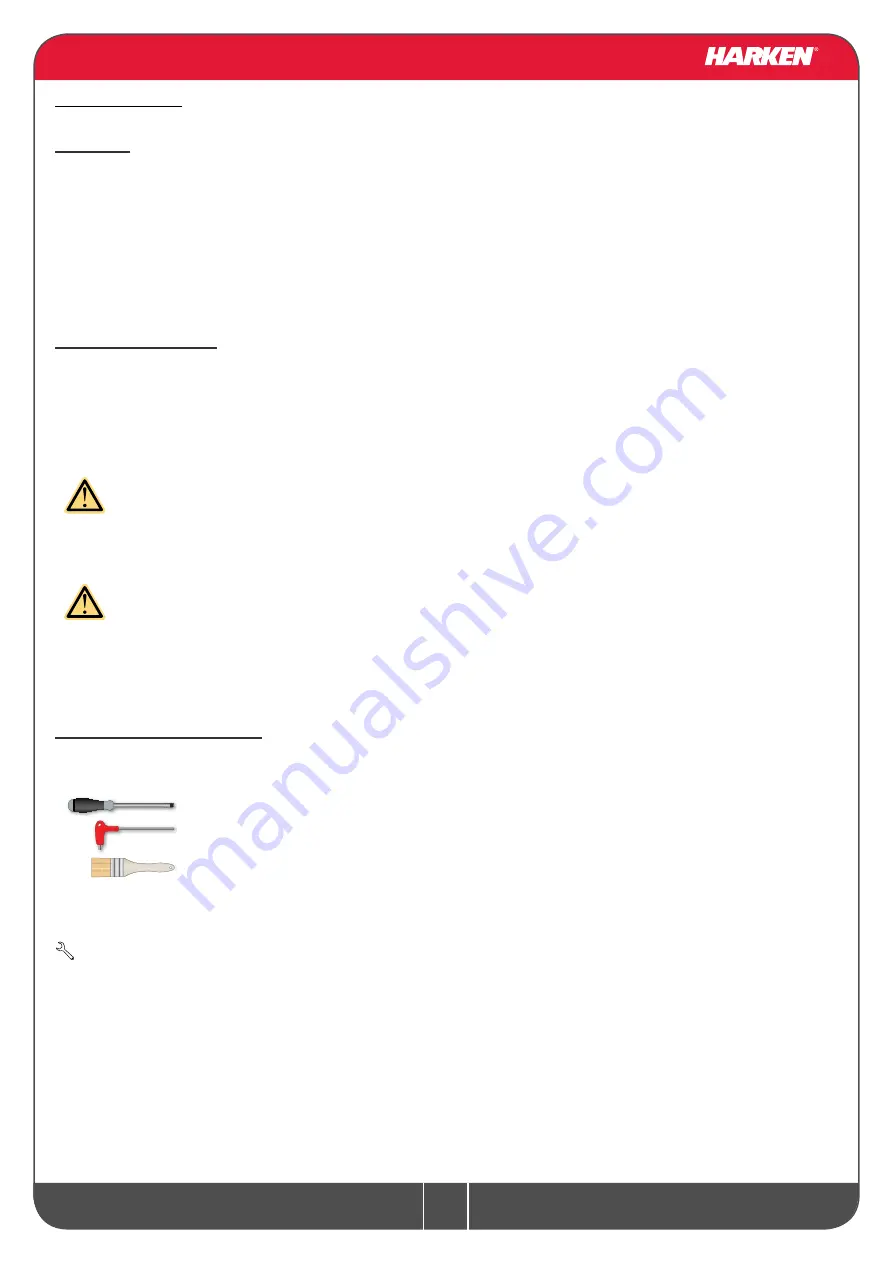
14
Radial Winch
40.2 ST EL
Installation and Maintenance Manual - Mod.E
Maintenance
Washing
Winches must be washed frequently with fresh water, and in any case after each use.
Do not allow teak cleaning products or other cleaners containing caustic solutions to come into
contact with winches and especially anodised, chrome plated or plastic parts.
Do not use solvents, polishes or abrasive pastes on the logos or stickers on the winches.
Do not use polishes or abrasive pastes on anodised, chromed plated or plastics surfaces.
Make sure that the holes and drainage channels in the base of the winch are not obstructed so that
water does not collect.
Maintenance table
Winches must be visually inspected at the beginning and end of every season of sailing or racing.
In addition they must be completely overhauled, cleaned and lubricated at least every 12 months.
After an inspection, replace worn or damaged components. Do not replace or modify any part of the
winch with a part that is not original.
WARNING!
Periodic maintenance must be carried out regularly. Lack of adequate maintenance shortens the
life of the winch, can cause serious injury and also invalidate the winch warranty.
Installation and maintenance of winches must be carried out exclusively by specialized
personnel.
WARNING!
Make sure that the power is switched off before installing or carrying out maintenance on
the winch.
In the case of doubt contact Harken
®
Tech Service at techservice@harken.it
Disassembly procedure
Tools needed:
One medium flat-bladed screwdriver
A number five hex key
Brush
Rags
To identify the various parts refer to the exploded view at the end of this Manual.
Torque to be applied in assembly phase
Maintenance