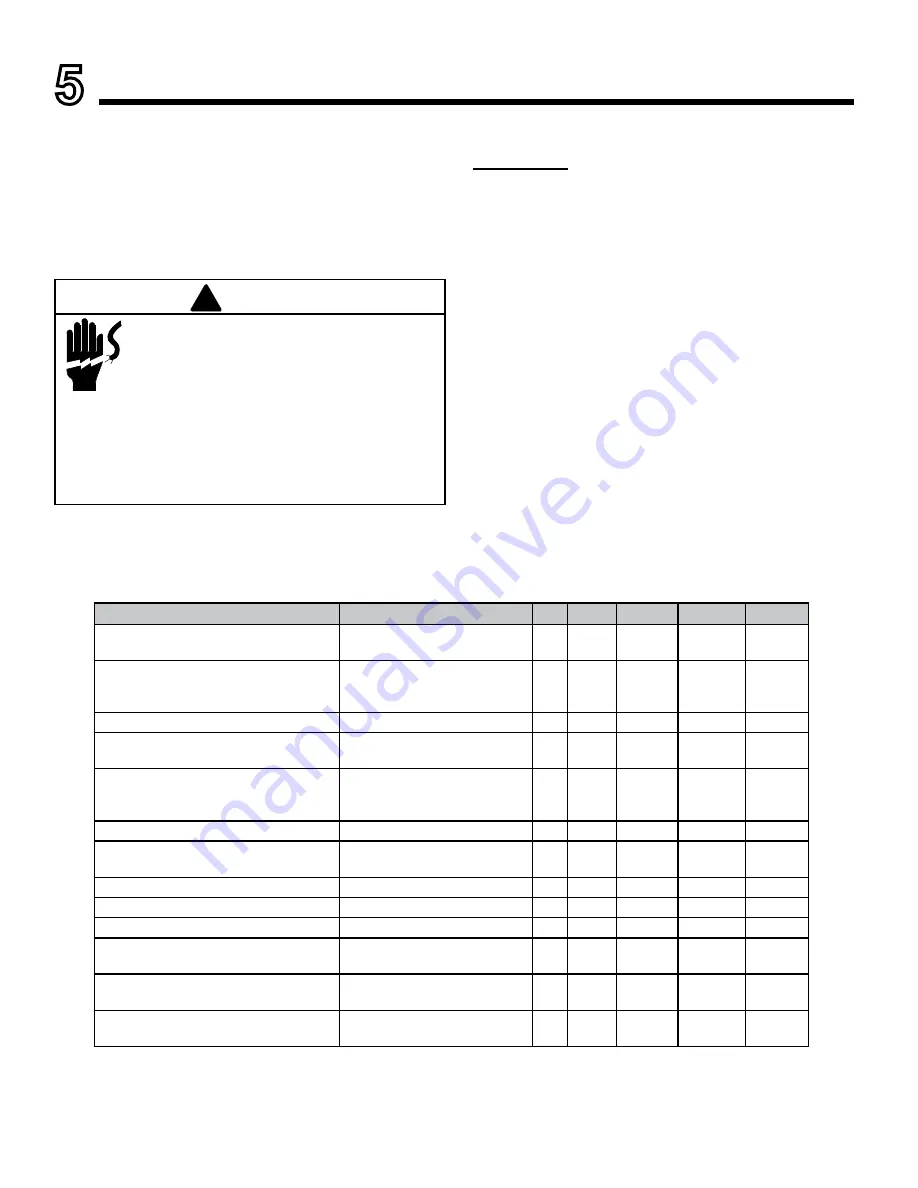
Harman® • Advance Owner’s Manual_R38 • 1999 - ___ • 09/15
16
3-90-436168c
B. Quick Reference Maintenance Chart
Follow the detailed instructions found in this
section for each step listed in the chart below
.
Cleaning or Inspection
Frequency
Daily Weekly Monthly Yearly
Ash Pan
Every 5 bags of fuel depending
on the fuel type or ash build-up
OR
X
Ash Removal from Firebox
Every 5 bags or more
frequently depending on the
fuel type or ash build-up
OR
X
Heat Exchanger
Every 1 ton of fuel
OR
X
Blower, Combustion (Exhaust)
More frequently depending on
the fuel type
OR
X
Blower, Distribution
Every 25 bags or more
frequently depending on the
fuel type
OR
X
Door Gasket Inspection
Prior to heating season
OR
X
Exhaust Path
More frequently depending on
ash build-up
OR
X
Firebox - Prepare for Non-Burn Season At end of heating season
OR
X
Burnpot - Burning pellets - hardwood
Every 3 bags
OR
X
Burnpot - Burning pellets - softwood
Every 5 bags
OR
X
Glass
When clear view of burnpot
becomes obscure
OR
X
Hopper / Hopper Lid Gasket
Every 50 bags of fuel or when
changing fuel types
OR
X
Venting System
More frequently depending on
the fuel type
OR
X
NOTICE:
These are recommendations. Clean more frequently if you encounter heavy build-up of ash at the recommended
interval or you see soot coming from the vent.
Not properly cleaning your appliance on a regular basis will void your
warranty.
5
Maintenance & Service
Shock and Smoke Hazard
• Turn unit to the off position, let appliance
completely cool and combustion blower must
be off. Now you can unplug appliance before
servicing.
• Smoke spillage into room can occur if appliance
is not cool before unplugging.
• Risk of shock if appliance not unplugged before
servicing appliance.
A. Proper Shutdown Procedure
C. General Maintenance
Types of Fuel
The type of fuel you are burning will dictate how often you have
to clean your burnpot.
If the fuel you are burning has a high dirt or ash content it may
be necessary to clean the burnpot more than once a day.
Dirty fuel will cause clinkers to form in the burnpot. A clinker is
formed when dirt, ash or a non-burnable substance is heated
to 2000°F (1093°C) and becomes glass-like.
When properly maintained, your stove will give you many
years of trouble-free service.
Contact your dealer
to answer
questions regarding proper operation, trouble-shooting and
service for your appliance. Visit www.harmanstoves.com to
find your closest dealer. We recommend annual service by
a qualified service technician.
CAUTION
!