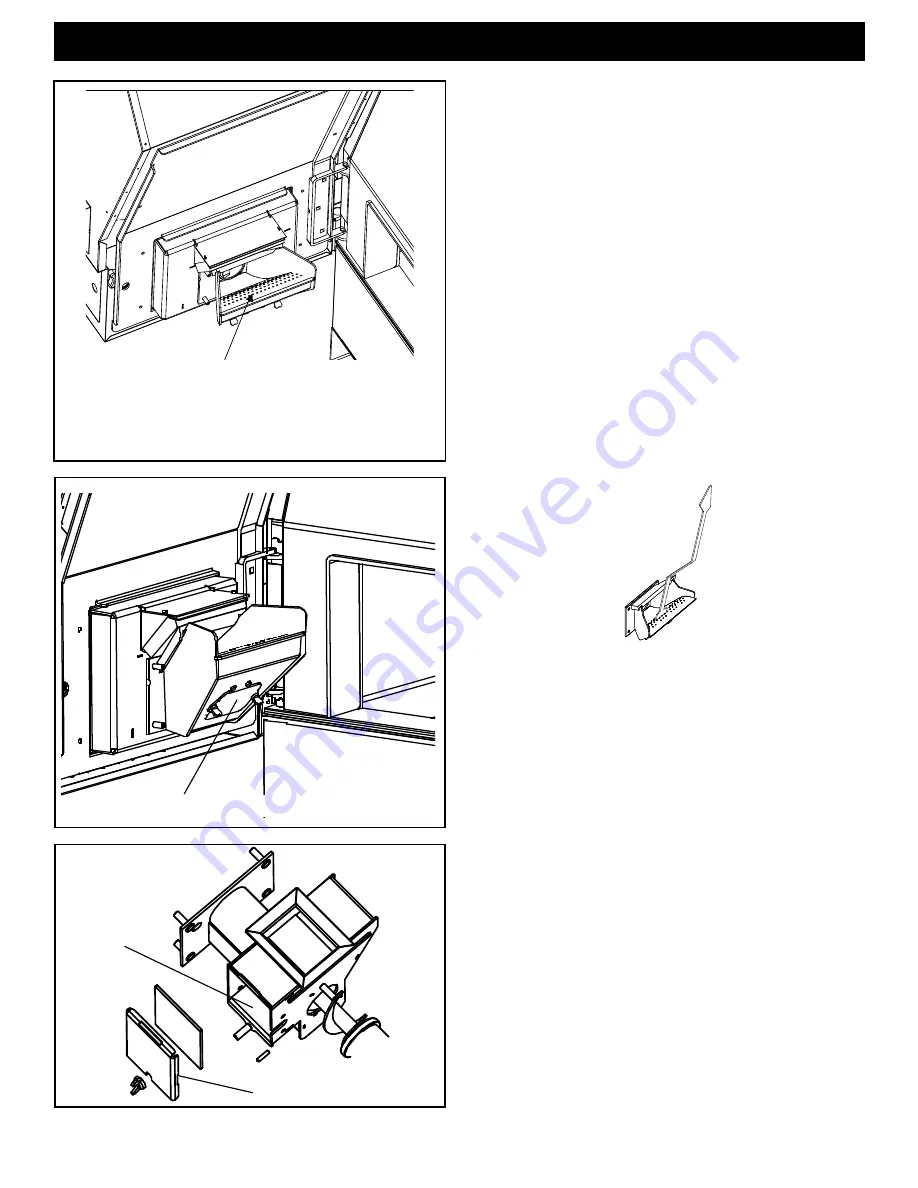
30
Fig. 18
Burnpot Cleaning:
The burnpot should be cleaned no less than once a week.
For best operation the burnpot should be cleaned every time
the hopper is filled with pellets. The fire does not have to be
out to scrape the burnpot although it is recommended the
boiler be on minimum burn at the time of cleaning.
Note:
Scraping can be done while in operation if performed
through the firebox door opening. See Fig. 17
Use the flat end of the scraper provided to scrape down
over the holed surface of the burnpot grate. See Fig. 18. It
is not necessary to clean out the scrapings from this cleaning
because they will be pushed out the next time the auger
operates.
Note:
Make a special effort to scrape the bottom inside
corners of the burnpot where the auger tube enters the
burnpot. Carbon deposits can build up over time in this
area that may cause a restriction to the flow of pellets into
the burnpot.
Note:
An old long shank screwdriver with the end
sharpened is an ideal aid in the removal of these deposits.
Cleaning the Burnpot Air Chamber:
This area only needs to be cleaned twice a heating season,
unless excessive buildup is noticed during scheduled
cleanings.
There is a cover on the front of the burnpot to gain access
to the air chamber. The cover is held into place by two thumb
screws. Loosen the thumb screws and remove the cover. See
Fig. 19. The air chamber can be cleaned of any ash that has
fallen through the holes during operation and cleaning. Also
at this time, remove the feeder assembly cover and remove
any fines that may have accumulated.
NOTE:
ALWAYS REMEMBER TO CLOSE THE
CLEANOUT COVER AFTER CLEANING.
Feeder Chamber (Fig. 20):
This chamber may get a buildup of fines from the feeder
mechanism movement. This area should be checked and
cleaned at least once a year.
To remove the feeder cover:
• Loosen the 5/16” wing nut.
• Slide the cover off of the threaded stud and lift upward.
• Inspect and clean the inner chamber if necessary. See Fig. 20.
• Reinstall the cover making certain it is centered on the
feeder body and hand-tighten the wing nut.
maintenance
Cleanout Cover
Fig. 19
Fig. 20
Fines area
Feeder cover
Fig. 17
Scrape burnpot to remove any carbon
build-up that may have occurred
Scraping can be done while in operation
Scrape the burnpot to remove any carbon
deposits which may have formed.
Scraping can be done while the boiler
is in operation, accessed through the
firebox door opening.
Summary of Contents for PB 105
Page 2: ......
Page 45: ...45 Service Record Notes...
Page 46: ...46 Service Record Notes...