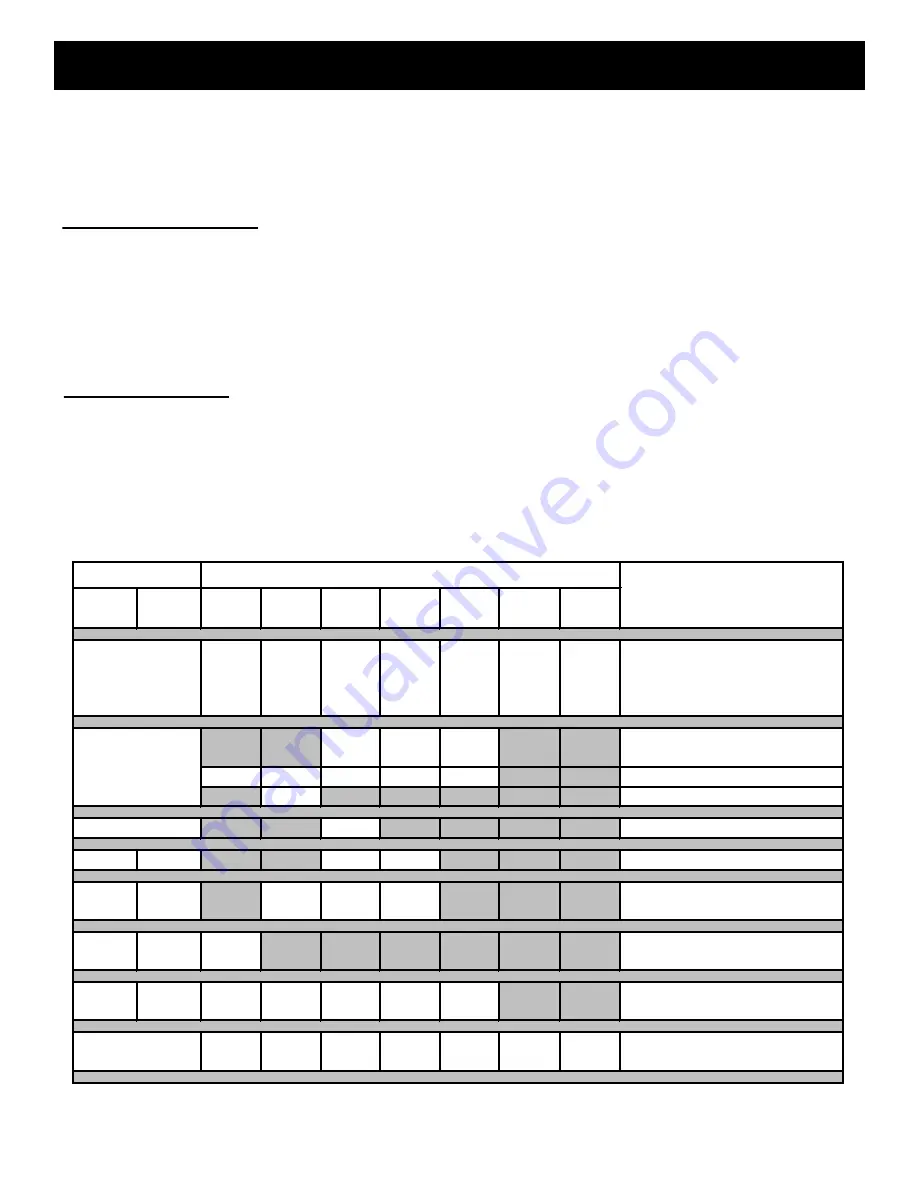
44
3-90-08101R23_06/13
warranty
4021-645F 02-18-13
Page 1 of 2
hearth & home Technologies
lImITEd lIFETImE wArrANTY
Hearth & Home Technologies, on behalf of its hearth brands (”HHT”), extends the following warranty for HHT
gas, wood, pellet, coal and electric hearth appliances that are purchased from an HHT authorized dealer.
wArrANTY COvErAgE:
HHT warrants to the original owner of the HHT appliance at the site of installation, and to any transferee taking ownership
of the appliance at the site of installation within two years following the date of original purchase, that the HHT appliance
will be free from defects in materials and workmanship at the time of manufacture. After installation, if covered compo-
nents manufactured by HHT are found to be defective in materials or workmanship during the applicable warranty period,
HHT will, at its option, repair or replace the covered components. HHT, at its own discretion, may fully discharge all of its
obligations under such warranties by replacing the product itself or refunding the verified purchase price of the product
itself. The maximum amount recoverable under this warranty is limited to the purchase price of the product. This warranty
is subject to conditions, exclusions and limitations as described below.
wArrANTY PErIOd:
Warranty coverage begins on the date of original purchase. In the case of new home construction, warranty coverage
begins on the date of first occupancy of the dwelling or six months after the sale of the product by an independent,
authorized HHT dealer/ distributor, whichever occurs earlier. The warranty shall commence no later than 24 months
following the date of product shipment from HHT, regardless of the installation or occupancy date. The warranty period for
parts and labor for covered components is produced in the following table.
The term “Limited Lifetime” in the table below is defined as: 20 years from the beginning date of warranty coverage for
gas appliances, and 10 years from the beginning date of warranty coverage for wood, pellet, and coal appliances. These
time periods reflect the minimum expected useful lives of the designated components under normal operating conditions.
See conditions, exclusions, and limitations on next page.
Parts
Labor
Gas
Wood
Pellet
EPA
Wood
Coal
Electric Venting
X
X
X
X
X
X
X
All parts and material except as
covered by Conditions,
Exclusions, and Limitations
listed
X
X
X
Igniters, electronic components,
and glass
X
X
X
X
X
Factory-installed blowers
X
Molded refractory panels
X
Firepots and burnpots
5 years 1 year
X
X
Castings and baffles
7 years 3 years
X
X
X
Manifold tubes,
HHT chimney and termination
10
years
1 year
X
Burners, logs and refractory
Limited
Lifetime 3 years
X
X
X
X
X
Firebox and heat exchanger
X
X
X
X
X
X
X
All replacement parts
beyond warranty period
Warranty Period
HHT Manufactured Appliances and Venting
1 Year
Components Covered
3 years
2 years
90 Days
Summary of Contents for PF100
Page 48: ...48 3 90 08101R23_06 13 ...