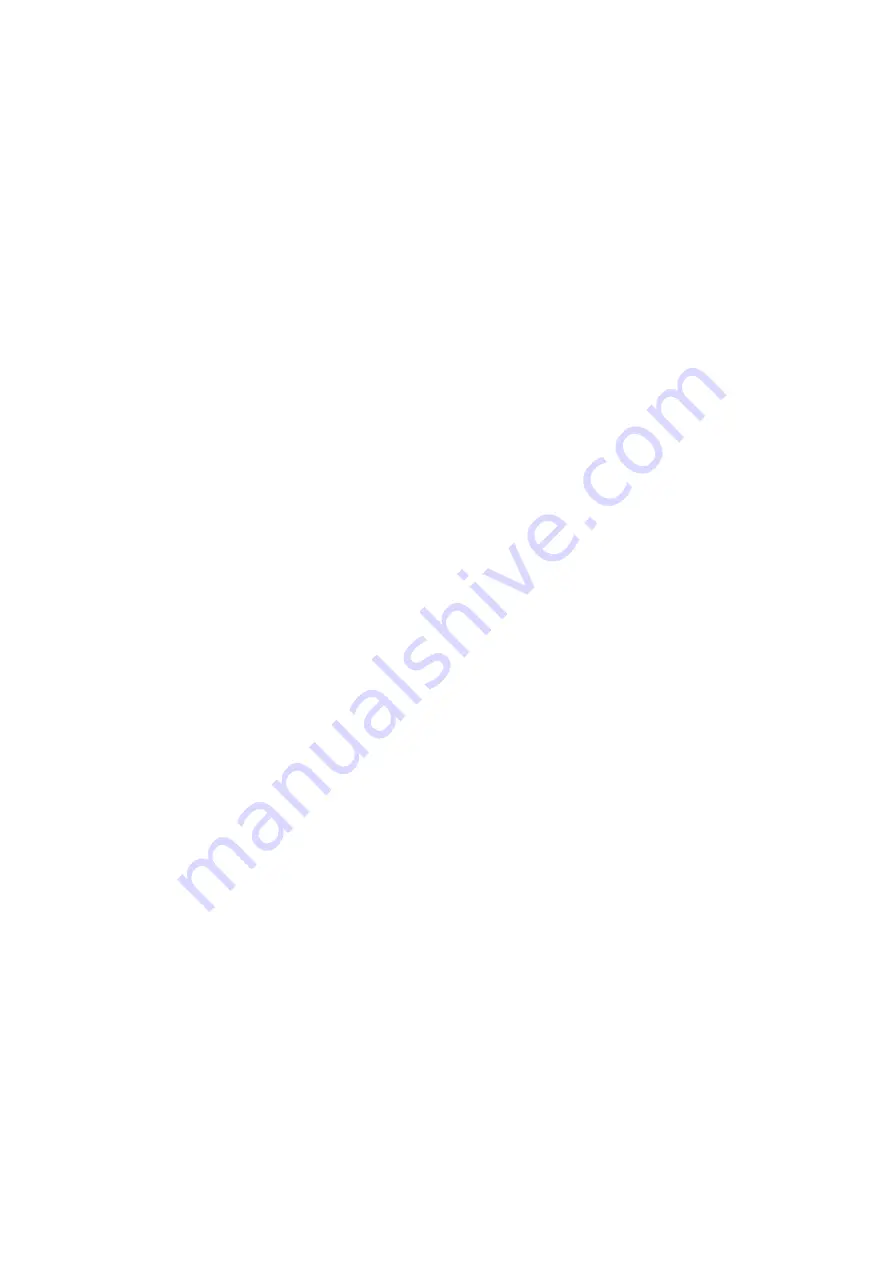
53
1019658 11/2014
Maximum DC bus voltage U
DC (max)
[VDC]
The maximum DC bus power supply for the correct operation of the actuator. This value may only be exceeded for a short
period during the braking or deceleration phase.
Maximum hollow shaft diameter d
H (max)
[mm]
For gears with a hollow shaft, this value is the maximum diameter of the axial hollow shaft.
Maximum input speed (grease lubrication) n
in (max)
[rpm]
Maximum allowed input speed for gearing with grease lubrication.
Maximum input speed (oil lubrication) n
in (max)
[rpm]
Maximum allowed input speed for gearing with oil lubrication.
Maximum motor speed n
max
[rpm]
The maximum allowable motor speed.
Maximum output speed n
max
[rpm]
The maximum output speed. Due to heating issues, this may only be momentarily applied during the operating cycle. The
maximum output speed can occur any number of times as long as the rated speed is greater than the permissible continuous
operation calculated in the duty cycle.
Maximum output torque T
max
[Nm]
Specifies the maximum allowable acceleration and deceleration torques. For highly dynamic processes, this is the maximum
torque available for a short period. The maximum torque can be parameterized by the control unit where the maximum
current can be limited. The maximum torque can be applied as often as desired, as long as the average torque is within the
permissible continuous operation calculated in the duty cycle.
Maximum power P
max
[W]
Maximum power output.
Mechanical time constant
τ
m
[s]
The mechanical time constant is the time required to reach 63% of its maximum rated speed in a no-load condition.
Momentary peak torque T
M
[Nm]
In the event of an emergency stop or collision, the Harmonic Drive® Gearing may be subjected to a brief collision torque.
The magnitude and frequency of this collision torque should be kept tom a minimum and under no circumstances should
the momentary peak torque occur during the normal operating cycle.
Moment of inertia J [kgm²]
Mass moment of inertia at motor side.
Moment of inertia J
in
[kgm²]
Mass moment of inertia of the gearing with respect to the input.
Moment of inertia J
out
[kgm
2
]
Mass moment of inertia with respect to the output.