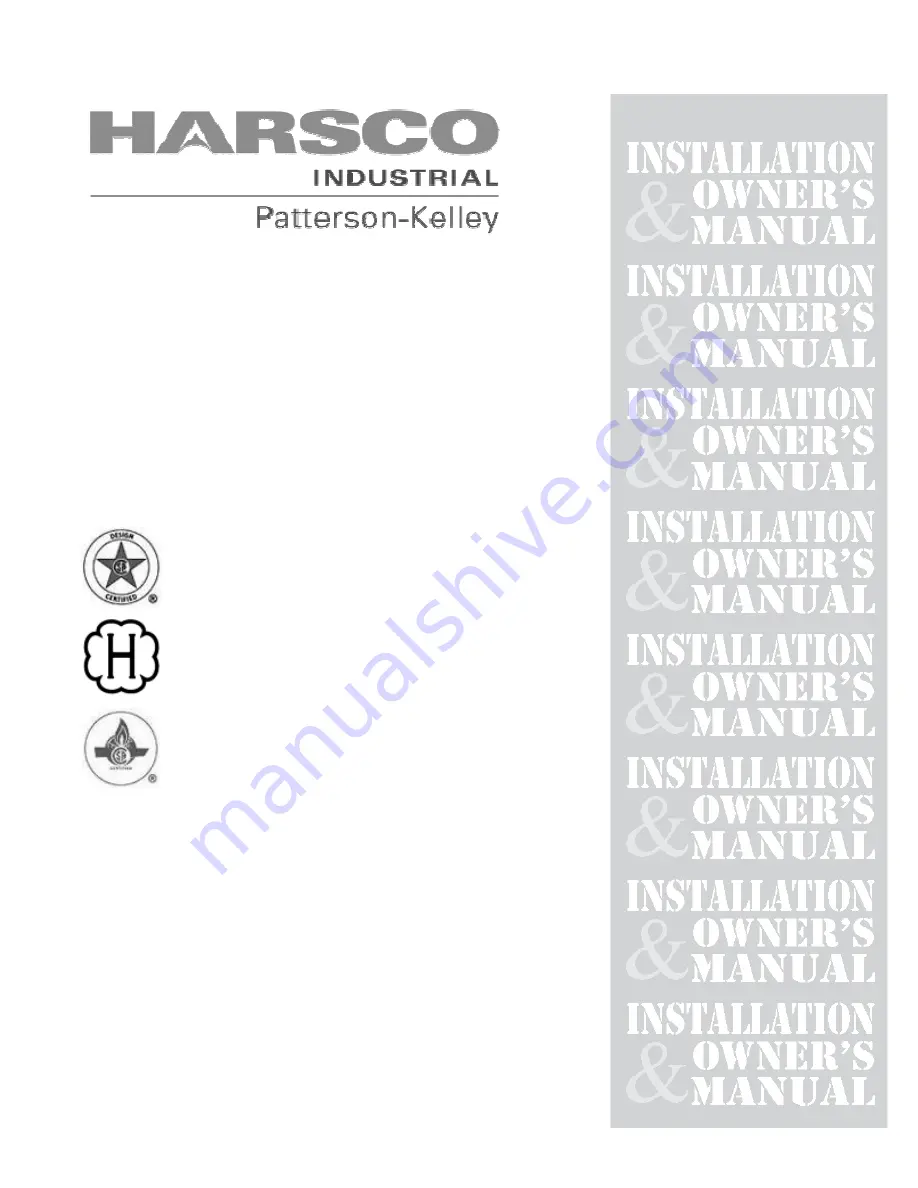
©2010 Harsco Industrial, Patterson-Kelley
Printed: 1/21/2010
Model #:_______ Serial #______________________
Start-Up Date:
_______________________
Harsco Industrial, Patterson-Kelley
100 Burson Street
East Stroudsburg, PA 18301
Telephone: (570) 476-7261
Facsimile: (570) 476-7247
www.harscopk.com
C.S.A. Design-Certified
Complies with ANSI Z21.13/CSA 4.9
Gas-Fired Low Pressure Steam and Hot Water Boilers
ASME Code, Section IV
Certified by Patterson-Kelley
C.S.A. Design-Certified
Complies with ANSI Z21.13/CSA 4.9
Gas-Fired Low Pressure Steam and Hot Water Boilers