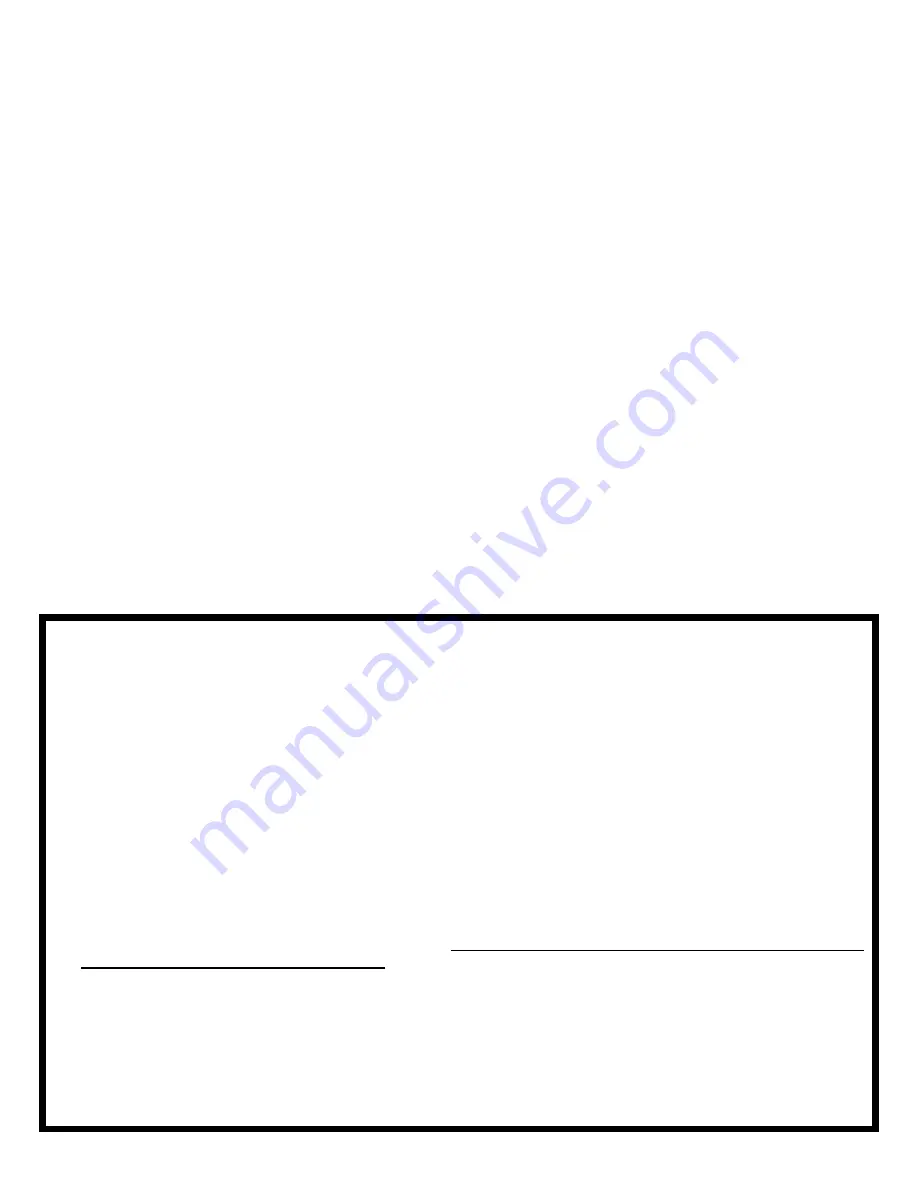
Table of Contents
A. Purpose………………………………………………………………………………………………………….Page 2
B. Installation
Precautions…………………………………………………..………….… ……………Pages 2 and 3
C. Installation………………………………………………………………………………… ………….…Pages 3 to 6
•
Regulations
•
Location
•
Venting
•
Gas Supply
•
Electrical
D. Electronic
Ignition……………………………………………………………………………… ……………..Page 7
E. Operation…………………………………………………………………………………………….………..Pages 7
F. Trouble
Shooting……………………………………………………………………………… .. …….Pages 8 to 11
G. Cleaning………………………..……………………………………………………… …….………Page 11 and 12
H. Flue Vent Arrangement Diagrams….……………………………………………….……………Pages 13 and 14
I. Illustration.……………………………………………….……………………………..……… …..…Page 15 & 16
J. Factory
Service….………………………………………………………………………….…… ………..…Page 16
A. PURPOSE:
The Hastings (I) (IS) HRDV series is a complete line of duct furnaces suitable for both INDOOR or OUTDOOR
APPLICATIONS. The (I) (IS) HRDV models100-400 are design certified by A.G.A. and C.G.A. and approved
for installation either upstream or downstream from cooling coils used in air conditioning systems and for
applications where make-up air is specified. The purpose of this manual is to present a guide for proper
installation, operation, and maintenance of the (I) (IS) HRDV furnace, and to supplement, BUT NOT TO
REPLACE, the services of qualified field service personnel. This manual should be made readily available to
operating personnel as an aid in maintenance and trouble shooting. If there are questions pertaining to the
installation or operation of this unit, consult manufacturer.
WARNING
B. INSTALLATION
PRECAUTIONS:
NOTE: GUARANTEE OF THIS EQUIPMENT IS SUBJECT TO CONFORMANCE WITH THE FOLLOWING:
1 Heater Location Requirements:
a. Outdoor units with poor venting, pilot outage, and other undesirable operating conditions may be caused by a
negative pressure condition or high pressure zones created by walls or other obstructions. Therefore, the furnace
must be located as far as possible from the source of such turbulence and at least six feet from the edge of the roof.
b. Indoor units must NOT be operated in the presence of CHLORINATED SOLVENTS. Even slight traces of chlorine
combined with products of combustion will cause serious damage.
c. Indoor units must have adequate COMBUSTION AIR. If heaters are installed in a closed room, provide outside
opening of one square inch per 1,000 BTU for combustion air alone.
d. Indoor units must not operate in an area with a negative air pressure condition. Provide adequate MAKE-UP AIR.
e. Indoor units installed where there is sawdust, lint, soot, dirt, etc., areas of high air contamination, must be cleaned
FREQUENTLY or serious damage will result. Refer to section on CLEANING for recommended frequency.
2. WARNING: Installer/Service Technician must remove burner tray to inspect burner assemblies, to insure proper
alignment. Prior to installing gas supply line to unit gas inlet, remove the “L” locking bracket and disconnect the
electrical connections and slide the burner tray out of the heater. Once inspection is completed, replace the burner
tray assembly and install the “L” locking bracket.
Failure to perform this inspection could result in fire,
explosion, loss of warranty, or even death.
3. Firing rate must NOT be increased above the BTU input shown on the specification plate.
4. For U.S. installations at elevations above 2,000 feet (610 M), the appliance shall be derated 4 percent for each 1,000
feet (305 M) of elevation above sea level. For Canadian installations, appliances are certified for altitudes of 0 to
2,000 feet (0-610 M) and 2,000 to 4,500 feet (610-1,370 M). High altitude ratings may be obtained by a change in
orifice size and/or manifold pressure. Contact the manufacturer or gas company before changing spud sizes or
pressure regulator setting. Use ½ inch socket wrench to remove spuds. NOTE: L.P. GAS UNITS ARE EQUIPPED
WITH SPECIAL TAPER REAMED SPUDS WHICH MUST NOT BE RESIZED IN THE FIELD.
5. Air starvation is a common cause of heat exchanger burn out. Air handling system design MUST POSITIVELY
ASSURE adequate and evenly distributed air flow through the heat exchanger. See ILLUSTRATIONS on page 15.
2