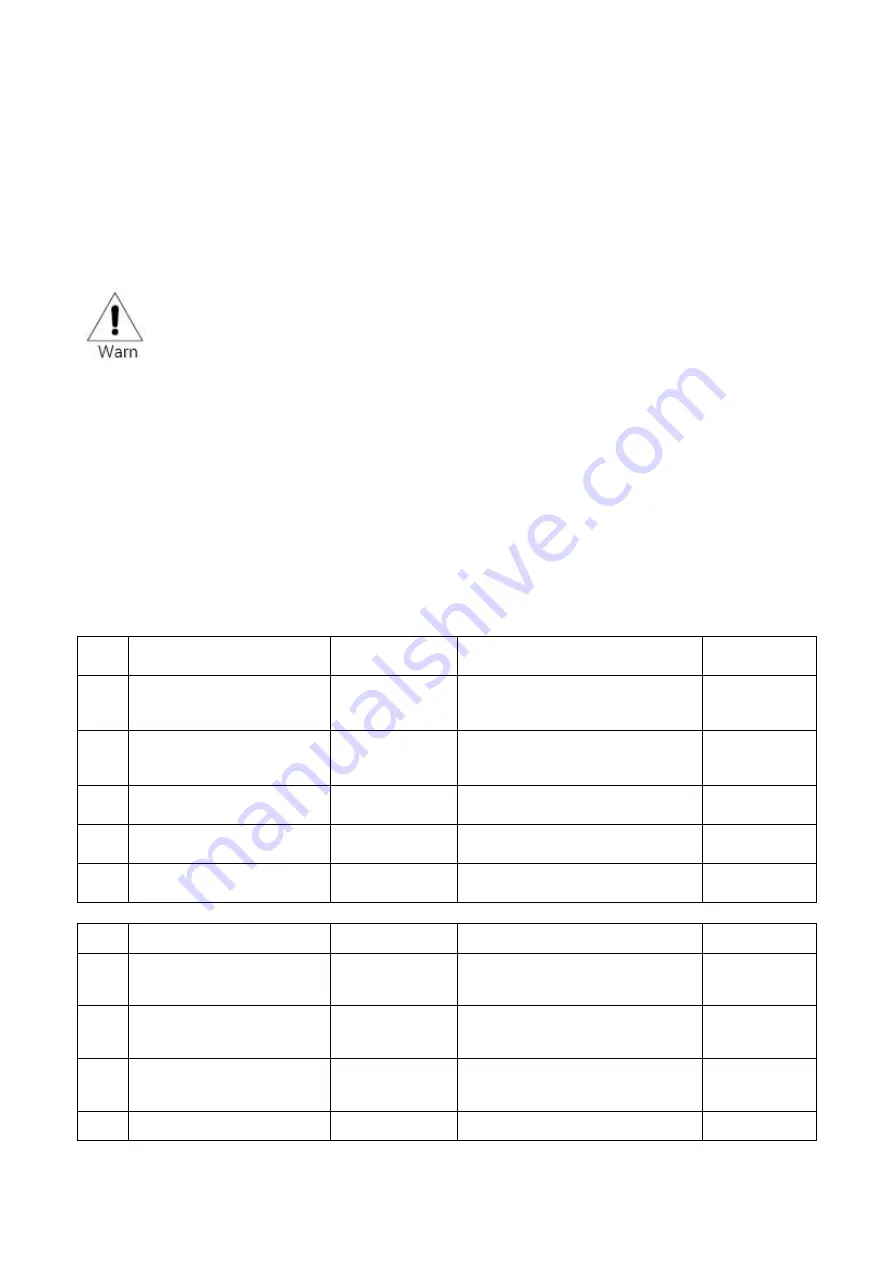
No.:GC-JS-21 Version: 01/00
Effective date
:
2020-03-30
31
9. Maintenance
In order to make this equipment work safely and reliably within the life span, periodic inspection, cleaning and
maintenance should be done.
9.1 Safety matters that should be paid attention to during equipment maintenance
:
⚫
Equipment maintenance should be carried out under sufficient light environment, and the light intensity should
not be less than 100lx;
⚫
Equipment maintenance should be carried out with the power cord disconnected and the equipment fully
cooled;
⚫
Consumables and accessories that need to be replaced should be provided by the manufacturer, otherwise it
may cause unpredictable problems;
⚫
The maintenance of the equipment should not be completed by the user, but must be performed by the
manufacturer or the personnel designated by the manufacturer.
⚫
The consumables or accessories that may be replaced by the user are:
1. Air filter; 2. Door sealing ring; 3. Safety valve 4. Power cord, 5. Other internal accessories
9.2 Maintenance plan
9.2.1 Cleaning plan
No.
Cleaning items
Cycle
Requirement
Remark
1
Sterilization
cleaning
chamber once a week
Keep clean without sewage
Refer to 9.3.1
2
Clean water tank
Once a month
No dirt on the surface of the water
tank
Refer to 9.3.2
3
Drain filter
Once a month
Filter is transparent
Refer to 9.3.3
4
Door seal
once a week
No dirt on the surface
Refer to 9.3.4
5
Water tank filter
Once a month
Filter is transparent
Refer to 9.3.5
9.2.2 Checking plan
序号
Checking items
Cycle
Requirement
Remark
1
Inspection of safety valve in
sterilization room
Every half year
Can be opened, and not opened
during the sterilization phase
Refer to 9.3.6
2
Storage tank liquid level
sensor
Every half year
There will be a reminder when
there is no water
Refer to 9.3.7
3
Water quality detection
function
Every half year
There will be a reminder when the
water quality exceeds the standard
Refer to 9.3.8
4
power cable
Every half year
No damage to external insulation
Refer to 9.3.9