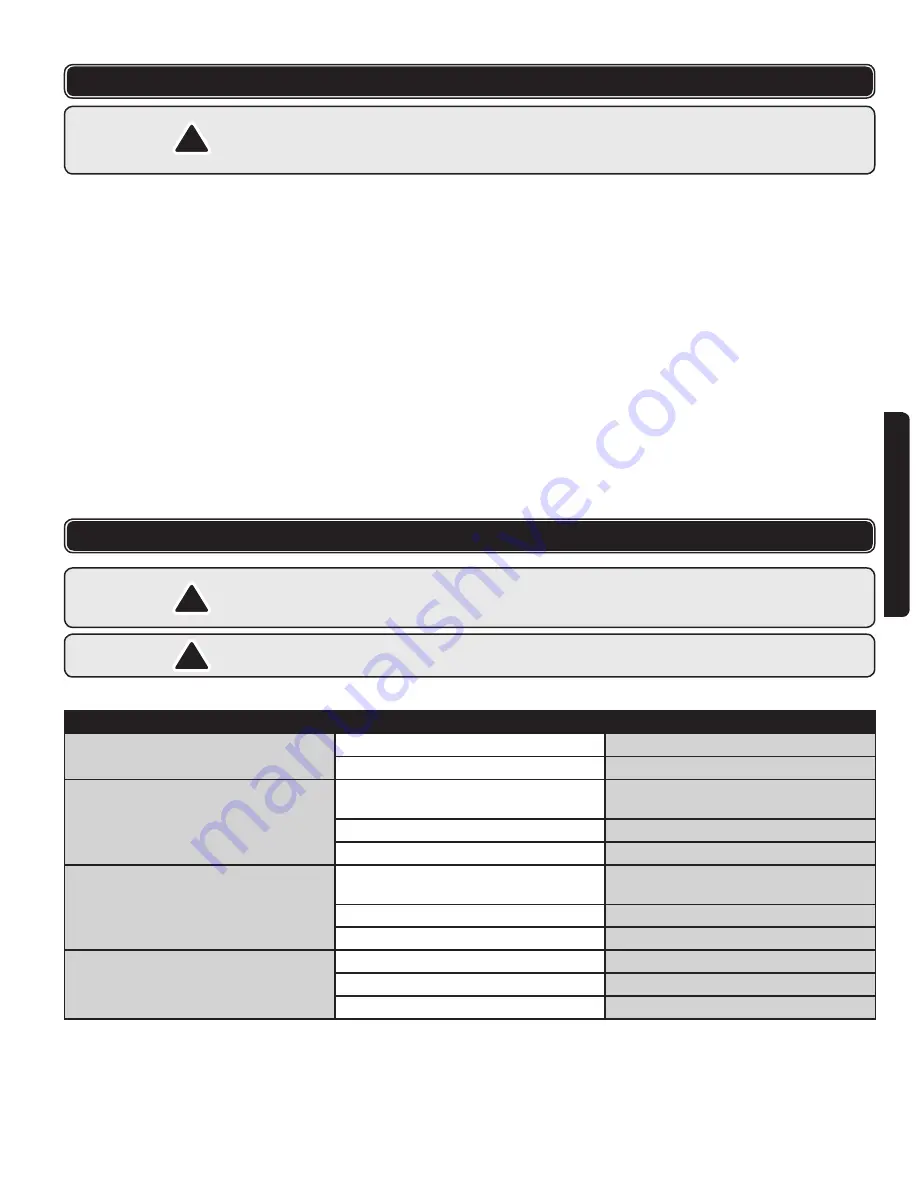
17
ENGLISH
!
!
!
MAINTENANCE
CAUTION:
z
Disconnect tool from air supply before cleaning and inspection.
z
Correct all problems before putting the tool back in service.
1.
Wipe tool clean and inspect for wear or damage. Use non-flamable cleaning
solutions to wipe exterior of tool only if necessary. Do not soak tool with
cleaning solutions. Such solutions can damage internal parts.
2. Inspect trigger and safety mechanism to assure system is complete and
functional: no loose or missing parts, no binding or sticking parts.
3. Keep all screws tight. Loose screws can cause personal injury or damage the
tool.
4. If the tool is used without an in-line oiler, place 2 drops of air tool oil into the
air inlet of the tool at the beginning of each workday and after about 1 hour
of continuous use. Frequent but not excessive lubrication is required for best
performance. Oil added through the airline connection will lubricate all internal
parts. Use only air tool oil. Do not use oil with detergents or other additives.
These can cause damage through accelerated wear to the seals in the tool.
5. Use a small amount of oil on all exterior moving parts and pivots.
6. Dirt and water in the air supply are major causes of pneumatic tool wear. See
the section on SETUP: AIR SYSTEM for more information.
7.
Keep tools clean for better and safer performance. Use non-flammable
cleaning solutions sparingly and only if necessary. Do not soak parts in the
solutions. Such solutions may damage O-rings and other parts.
TROUBLESHOOTING
WARNING:
Stop using the tool immediately if any of the following problems
occur. Serious personal injury may result. Any repairs or replacements must be
done by qualified personnel or by an authorized service centre only.
CAUTION:
Disconnect the tool from air supply before performing any service
procedure.
PROBLEM
CAUSE
CORRECTION
Air leak in cylinder cap
Loose nose screws (14)
Tighten, then re-check
Gasket (17) cracked or worn
Replace gasket
Tool lacks power or is slow to cycle.
Poor driving and re-setting power
Tool is dry and lacks lubrication
Use air tool oil
Air pressure is too low
Check air supply equipment
Exhaust is blocked
Clean exhaust channel
Tool skips fasteners or fasteners feed
intermittently
Damaged pusher spring
Replace spring
Fasteners are wrong size
Use correct fasteners
Magazine or wear plate is dirty
Clean magazine and nose
Fastener is jammed in tool
Driver channel is worn
Replace wear plate
Driver blade is broken or worn
Replace driver blade
Bent fasteners
Use correct fasteners
When inserting new or re-installing O-rings, make sure they are clean and lubricated with an O-ring lubricant.