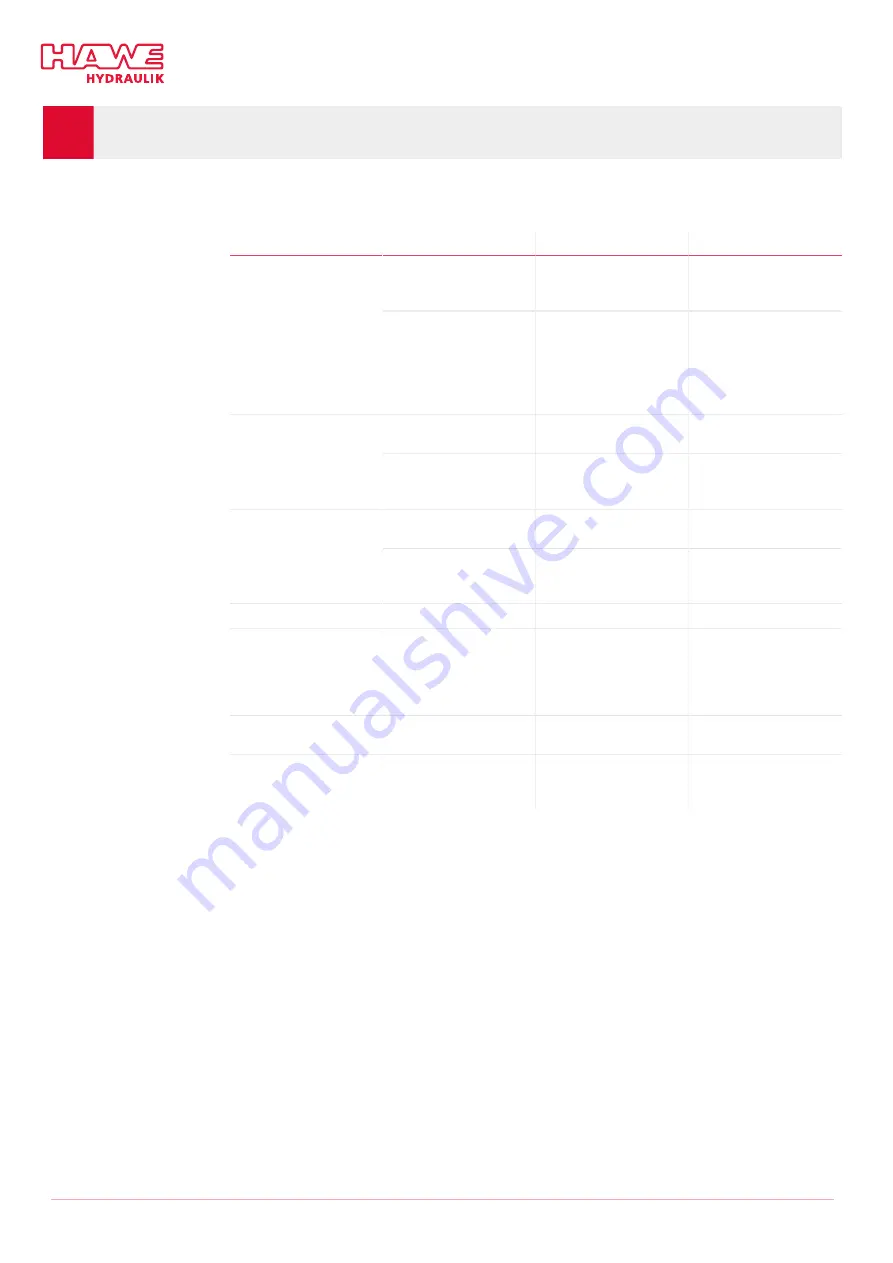
10
Troubleshooting
The following table lists possible faults and measures to eliminate these. Contact the manufacturer in
case of faults that cannot be remedied by following the descriptions here.
Fault
Possible cause
Test
Rectification
Faults with the motor
cable
Check the motor cable for
abrasion points, breaks,
for example
Replace motor
Motor does not start
For motor A4D and B2D:
triggering of the internal
temperature switch
due to the permitted
motor temperature being
exceeded.
Allow it to cool down
Hydraulic uid level in the
tank too low
Check the hydraulic uid
level
Top up hydraulic uid
Motor is running but pump
has no suction – hydraulic
power pack does not
convey hydraulic uid
Air in hydraulic system
Hydraulic system operates
irregularly due to air in
the system
Vent the hydraulic system
Incorrect rotation
direction of the motor
Check the motor rotation
direction
Correct the motor rotation
direction
No pressurization/pressure
too low
Incorrect setting of
pressure-limiting valve
Check the seal on the
pressure-limiting valve for
damage.
Contact HAWE.
Hydraulic uid is escaping Seal is faulty
Check the hydraulic lines
Replace the seal.
Contamination of the
hydraulic uid
Floating or deposited
contamination in the
hydraulic uid due to
debris, dirt, by-products
from ageing
Visual check
Hydraulic locking unit
must be replaced. Contact
HAWE.
Cylinder cannot be retract-
ed
Solenoid M faulty
Check resistance R; if R
→
∞, solenoid M faulty.
Replace 2/2-directional
seated valve SP3.
Cylinder does not hold
position
(For version H)
2/2-directional seated
valve SP3 is not tight
Replace 2/2-directional
seated valve SP3.
26/34
B 6025 - 12-2021 - 1.1en
HAWE Hydraulik SE