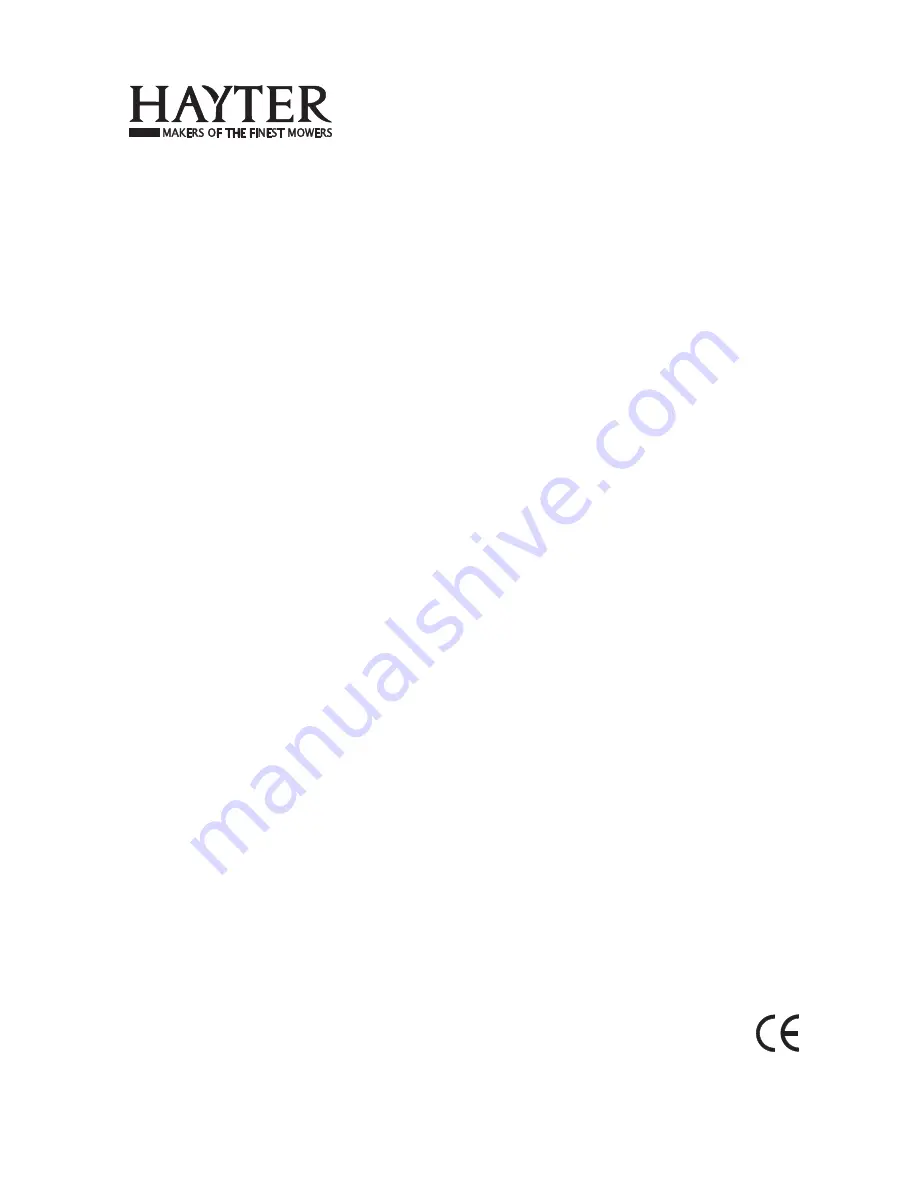
Part No. 111-5824 Rev A
CONDOR
HYDROSTATIC DRIVE
POWER UNIT Model No: 510D - Serial No. from 312030001
ATTACHMENTS - Serial No. from 312030001:
Verge Attachment 3 Blades - Code 214D
Verge Attachment 5 Blades - Code 243D
Rotary Attachment 30” - Code 212D
Operator’s Manual
Original Instructions (EN)
Date: 20.02.2012
Summary of Contents for CONDOR 510D
Page 2: ......
Page 4: ......
Page 49: ...1 49 1 49 NOTES ...
Page 50: ...1 50 1 50 NOTES ...
Page 52: ......