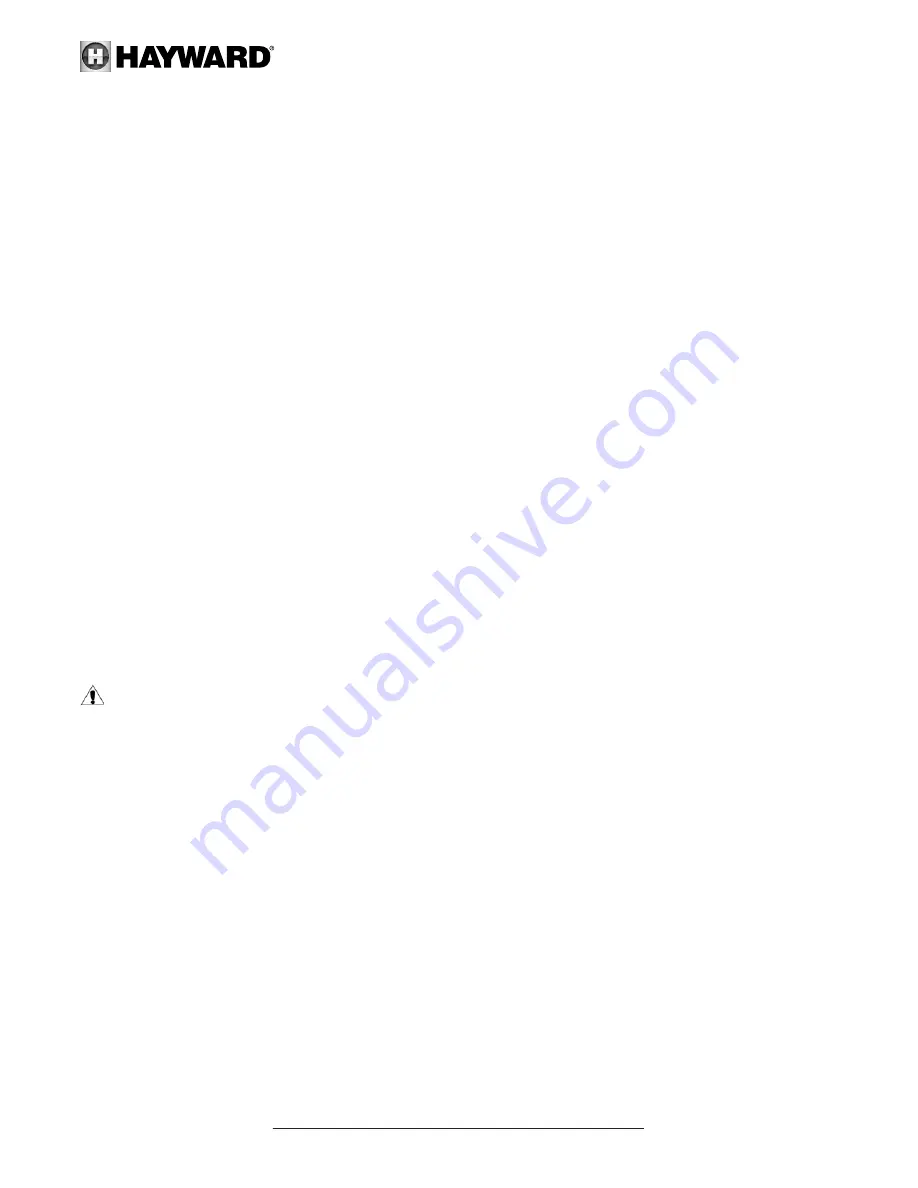
USE ONLY HAYWARD GENUINE REPLACEMENT PARTS
TriStar Variable Speed Pump
Page 11
Shaft Seal Change Instructions
IMPORTANT SAFETY INSTRUCTIONS
PLEASE READ AND FOLLOW ALL INSTRUCTIONS
When servicing electrical equipment, basic safety precautions should always be observed including the following.
Failure to follow the instructions may result in injury.
• Disconnect the pump motor power cord from the power outlet before beginning the shaft seal replacement.
• Only qualified personnel should attempt to replace the shaft seal. Contact your local authorized Hayward Dealer
or service center if you have any questions.
• Exercise extreme care in handling both the rotating and stationary sections of the two-part replacement seal.
Foreign matter or improper handling will easily scratch the graphite and ceramic sealing surfaces.
• See the “Parts Diagram” on page twelve (12) for the pump component locations.
Removing the Motor Assembly
1. Remove the six (6) 5/16” x 2” hex head bolts (Item #17), which hold the motor assembly to the pump/strainer
housing (item #3), using a 1/2” AF spanner or socket.
2. Slide the motor assembly out of the pump/strainer housing (item #3), exposing the diffuser (item #9). Remove the
two (2) diffuser screws (item #7), and pull the diffuser (item #9) off the seal plate (item #15) to expose the impeller
(item #12).
Removing the Impeller
1. To prevent the motor shaft from turning, insert a 6mm Allen Key through the center hole in the fan cowling and into
the socket on the end of the motor shaft.
2. Rotate the impeller screw (item #10) clockwise
(NOTE: this screw has a left-hand thread)
and remove. Remove
the impeller (item #12) by rotating it counterclockwise.
Removing the Ceramic Seat
1. Remove the spring seal assembly (item #13) and seal plate (item #15) from the motor by removing the four (4) 3/8”
x 1” bolts (item #18) that secure it to the motor, using a 9/16” AF spanner or socket. Remove the motor support
bracket (item #20) from the seal plate (item #15).
2. Press the ceramic seat with rubber cup out of the seal plate (item #15). If tight, use a small screwdriver to tap the seal
out from the back side of the seal plate.
IMPORTANT -
Clean all recesses and parts to be reassembled. Inspect gaskets and replace if necessary.
Seal, Impeller, and Diffuser Installation
1. Clean and lightly lubricate the motor shaft and seal recess in the seal plate (item #15) with a dilute solution of non
granulated liquid type soap. Gently wipe the polished face of the ceramic seal with a soft, lint free cotten cloth.
Lubricate the rubber cup on the ceramic seat and press it firmly into the recess of the seal plate (item #15), with the
polished ceramic surface facing towards you.
2. Reassemble the motor to the seal plate (item #15) using the four (4) 3/8” x 1” bolts (item #18) by tightening them in
a cross pattern. Ensure there is equal clearence between the motor shaft and ceramic seat. Re-attach the motor
support (item #20) to the seal plate (item #15).
3. Gently wipe the black, polished surface of the carbon spring seal assembly (item #13) with a soft, lint free cotton cloth.
4. Press the carbon spring seal assembly (item #13) onto the motor shaft, with the black polished surface facing the
ceramic seat.
5. Screw the impeller (item #12) onto the motor shaft in a clockwise direction and tightn snugly by holding the motor
shaft with the 6mm Allen Key as explained earlier. Screw the impeller screw (item #10) into the motor shaft in a
counterclockwise direction. Place the impeller ring (item #11) back onto the impeller (item #12), with its flange facing
towards the diffuser (item #9).
6. Place the diffuser (item #9) over the impeller (item #12) and onto the seal plate (item #15), aligning the three (3)
pins on the diffuser (item #9) with the three (3) holes on the seal plate (item #15). Replace the two (2) diffuser
screws (item #7).
7. Replace the motor Assembly into the pump/strainer housing in the reverse order of the removal steps. Ensure the
housing gasket (item #14) is lubricated and tighten the housing bolts (item #17) in a cross pattern evenly and to a
torque of 21 Newton Meters.
30-LITINSB004 Rev-B