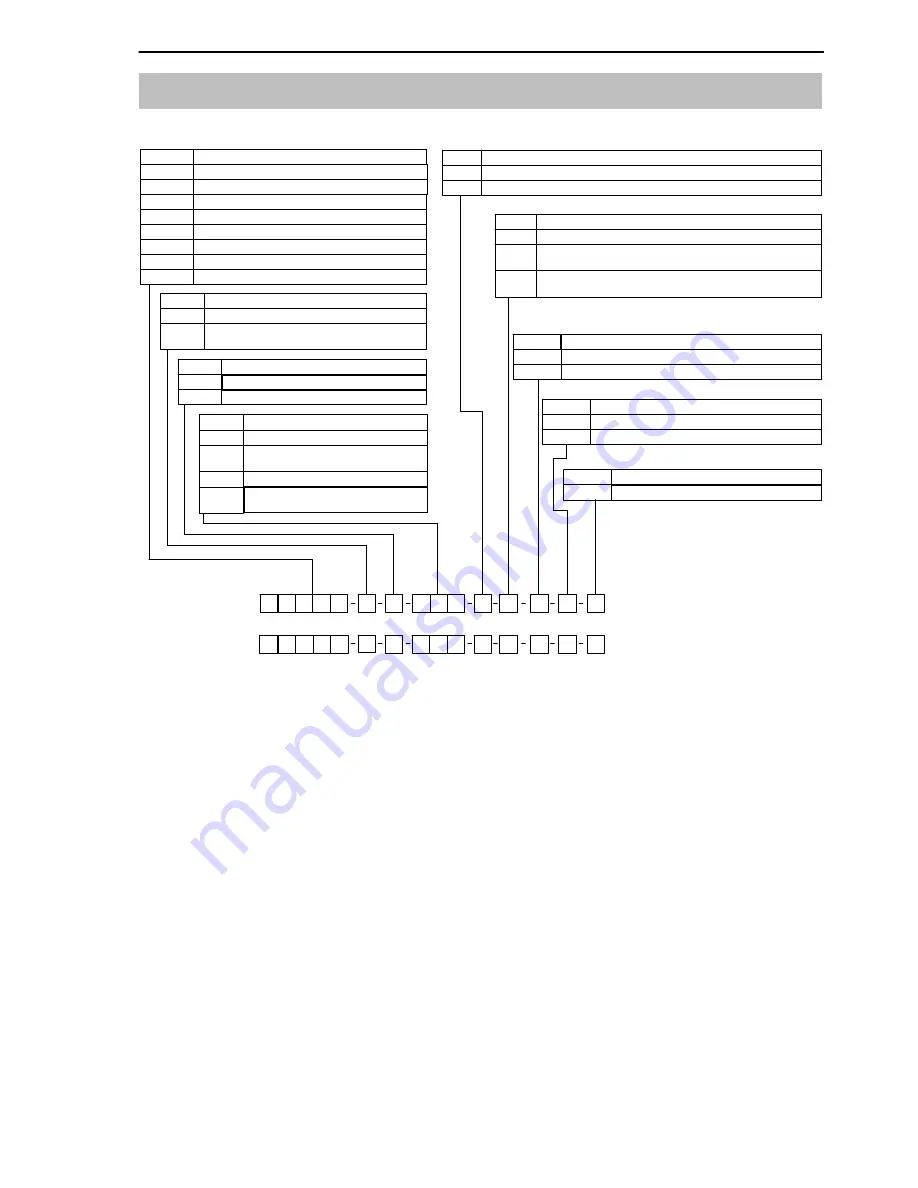
87
T12
A1979
−
10.0 en
HBM
19
Ordering numbers
L
Dependent on meas. range up to 15 000 rpm
Order no.:
K-T12
−
Ordering example:
K-T12
−
S F 1
C
5 0 0 Q
Code
Option 1: measuring range
S002R
2 kN
m
S003R
3 kN
m
Code
Option 7: protection against contact
Without protection against contact
Code
Option 2: accuracy
S
Standard
G
"
Greater accuracy
1)
Lin.
t"
0.01% and TK
0
t"
0.01%/10 K
L
Code
Option 6: rotational speed measuring system
1
With optical rotational speed measuring system;
360 or 720 pulses/revolution
With optical rotational speed measuring system;
360 or 720 pulses/revolution and reference signal
N
Without rotational speed measuring system
Code
Option 5: bus connection
P
CANopen and Profibus DPV1
C
CANopen (2 device plugs)
1
N
S
Code
Option 3: nominal (rated) rotational speed
H
Dependent on meas.range up to 18 000 rpm
S001R
1 kN
m
S500Q
500 N
m
Code
Option 4: electrical configuration
DF1
Output signal 60 kHz
"
30 kHz
DU2
Output signal 60 kHz
"
30 kHz and
"
10 V
SF1
Output signal 10 kHz
"
5 kHz
SU2
Output signal 10 kHz
"
5 kHz and
"
10 V
With protection against contact
Y
N
Code
Option 8: MODULFLEX
)
coupling
2)
Without coupling
N
With fitted coupling
N
A
Y
11)
For voltage output: lin.
t
"
0.05% ;
TK
0
t
"
0.1%/10 K
2)
For Option 3, code L only; see
data sheet B1957-xx de for
specifications.
S
Code
Option 9: Customized modification
No customized modification
N
N
S005R
5 kN
m
S010R
10 kN
m
S200Q
200 N
m
S100Q
100 N
m
Summary of Contents for T12
Page 1: ...A1979 10 0 en Digital Torque Transducer T12 Mounting Instructions ...
Page 2: ......
Page 89: ...89 T12 A1979 10 0 en HBM ...
Page 90: ...T12 90 A1979 10 0 en HBM ...
Page 91: ......