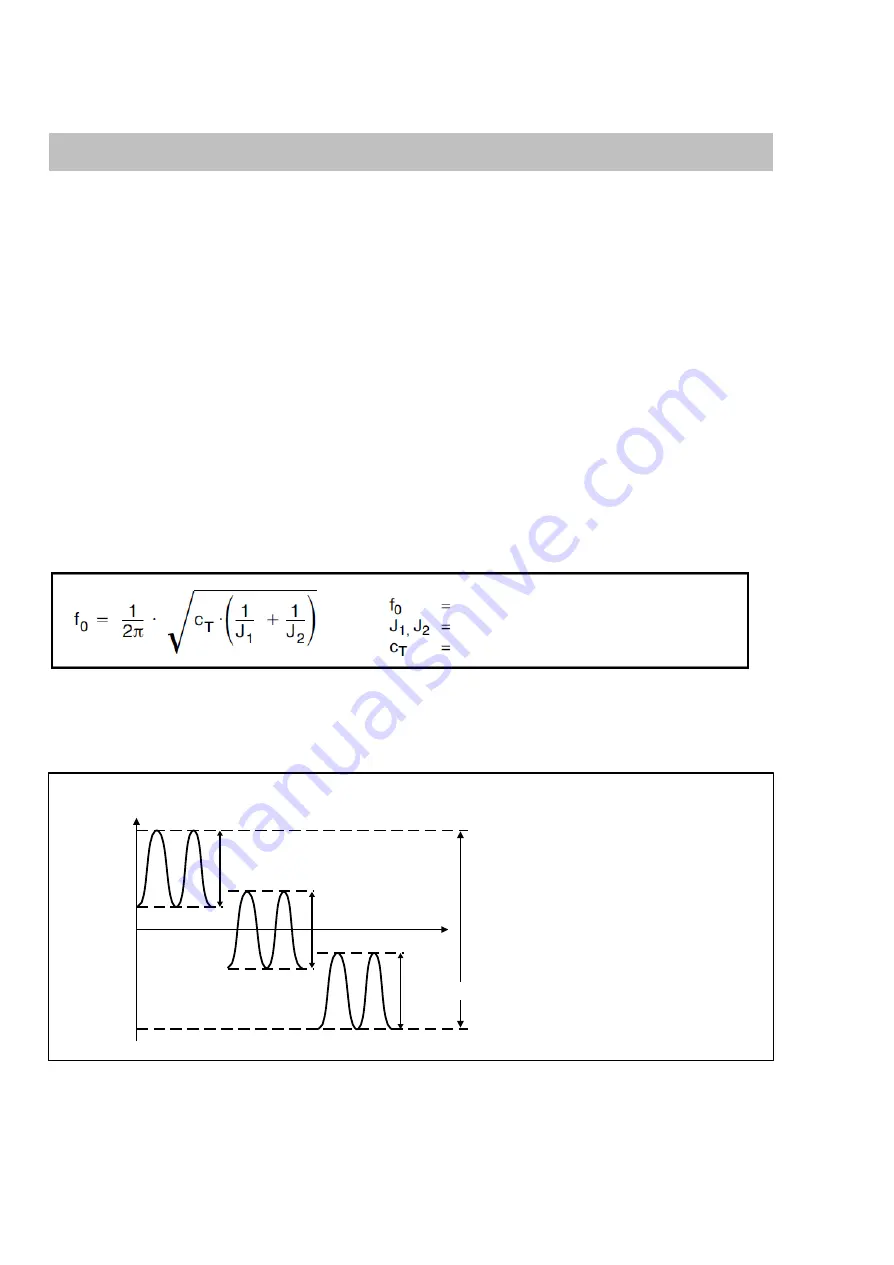
32
HBM T40MS 2020 en (11.03.2020) HBM: public
8 Loading capacity
Nominal torque can be exceeded statically up to the limit torque. If the nominal torque is
exceeded, additional irregular loading is not permissible. This includes longitudinal forces,
lateral forces and bending moments. Limit values can be found in the chapter
"Specifications" (Chapter 13, Page 34).
Measuring dynamic torque
The T40MS torque flange can be used to measure static and dynamic torques. The
following rule applies to the measurement of dynamic torque:
•
The transducer calibration performed for static measurements is also valid for
dynamic torque measurements.
•
The natural frequency f0 of the mechanical measurement setup depends on the
moments of inertia J1 and J2 of the connected rotating masses, and the torsional
stiffness of the transducer.
Use the equation below to approximately determine the natural frequency f0 of the
mechanical measuring arrangement:
•
The permissible mechanical vibration bandwidth (peak-peak) can also be
found in the specifications.
Nominal (rated) torque Mnom in %
+ Mnom
Oscillation width
Oscillation width
0
time
t
200% oscillation width
- Mnom
Oscillation width
Fig. 8.1:
Permissible dynamic loading
Natural frequency in Hz
Mass moment of inertia in kg·m^2
Torsional stiffness in N m/rad
Summary of Contents for T40MS
Page 1: ...HBM T40MS 2020 en 11 03 2020 HBM public Mounting Instructions English T40MS...
Page 2: ...HBM T40MS 2020 en 11 03 2020 HBM public...
Page 38: ...34 HBM T40MS 2020 en 11 03 2020 HBM public 11 Dimensions 11 1 Without speed measuring system...
Page 39: ...35 HBM T40MS 2020 en 11 03 2020 HBM public 11 2 With speed measuring system...