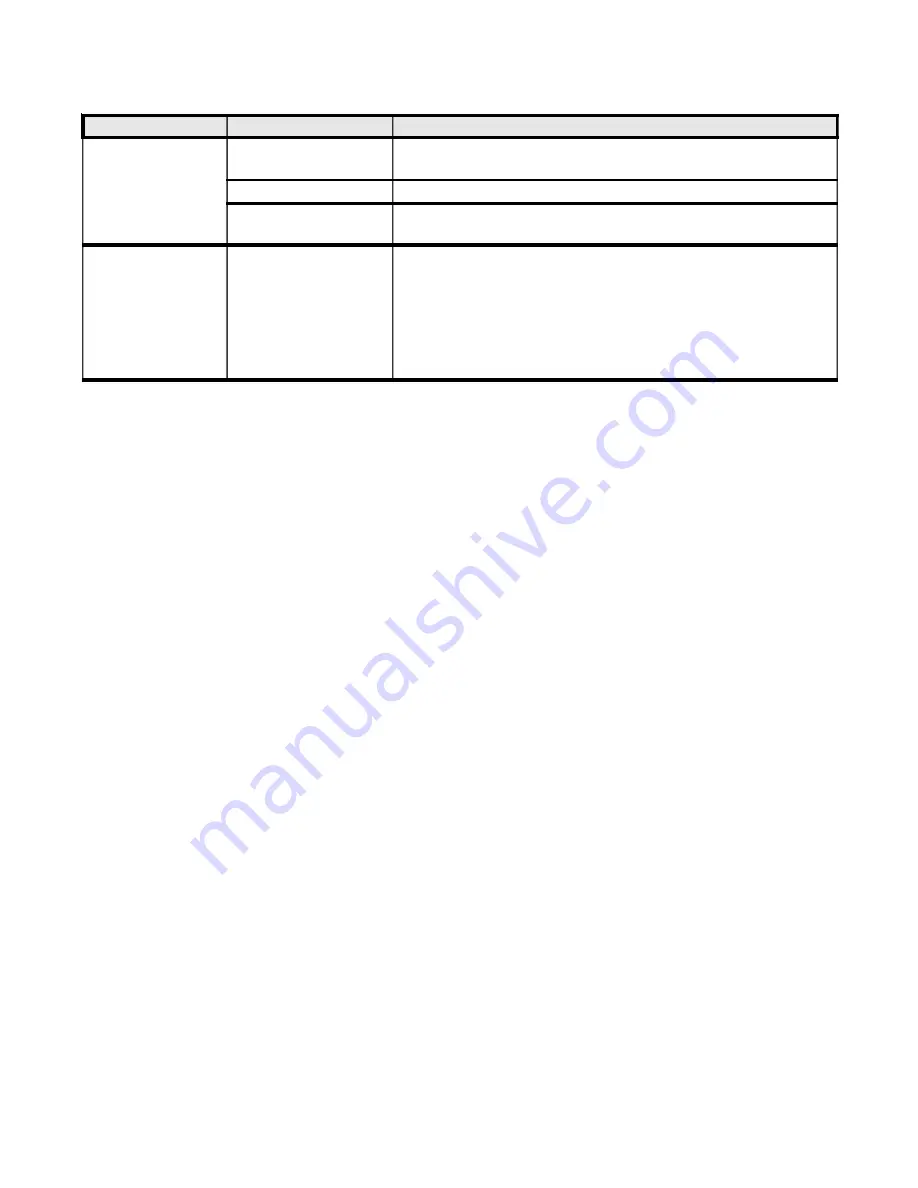
Heat & Glo • SL-550TRSI-AUE • 2079-902 Rev. B • 7/06
36
Electronic Ignition System - (continued)
Symptom
Possible Causes
Corrective Actions
10. Glass soots.
a. Flame impingement on
logs.
Adjust the log set so that the flame does not impinge on it.
b. Improper venturi setting.
Adjust the air shutter at the base of the burner.
c. Debris around venturi.
Inspect the opening at the base of the burner. It is imperative that NO
material be placed in this opening.
11.
Flame burns blue
and lifts off burner.
a. Insufficient oxygen
being supplied.
1. Check to make sure flue cap is installed properly and free of debris.
Make sure that flue system points are tight and have no leaks.
2. Check to make sure that no material has been placed in the opening at
the burner base or in the area of the air holes in the center of the base
pan beneath the burne.
3. Be sure glass is tighened properly on unit, particularly on top corners.