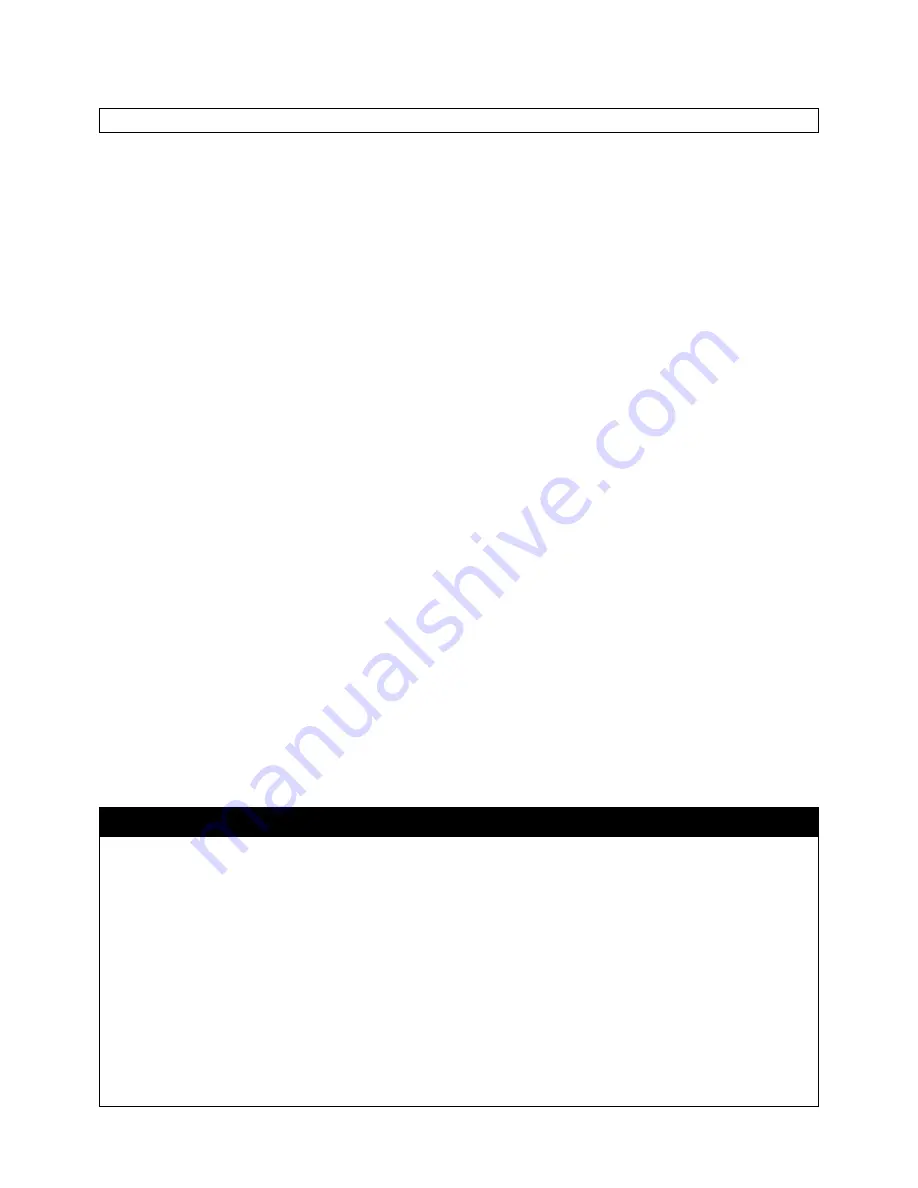
MGD Gas Furnace
Service Manual
RETRIES
A retry occurs when an attempt to achieve ignition fails and no flame is detected. The main valve
is turned off and the ignition cycle re-started. If three tries occur in a given operation sequence, the
furnace is shut down for one hour. During the one-hour period, safety conditions are still
monitored. Detection of an unsafe condition (such as flame not sensed, main valve energized,
limit open) the proper action as previously described will be followed.
CONTROL (LOW) VOLTAGE
In order to insure proper unit operation the transformer secondary output must be maintained at a
nominal 24 Volts. The 24 VAC Class 2 Transformer is protected from damage due to accidental
short circuits with a 3 AMP fuse.
GAS PIPING
Supply piping must be sized in accordance with recommendations found in National Fuel Gas
Code ANSI Z223.1/NFPA-54. In addition materials used in manufactured homes must comply
with requirements contained in HUD Title 24, Section 3280.705 as well as A119.1 and A119.2 for
recreational vehicles.
See chart in this manual for minimum sizes for NAT and LP pipe and tubing
serving the furnace
only
.
NOTE: The gas inlet on the gas control valve is ½” NPT. The gas line may be installed through the
bottom casing or on left or right side of furnace
.
An adequately sized gas supply to the unit is required for proper operation. Gas piping which is
undersized will not provide sufficient capacity for proper operation.
WARNING
Take care when connecting the gas line to the furnace gas valve. Use suitable wrenches
to support the gas valve when tightening fittings to prevent miss-alignment
of the attached burner orifice. Do not damage the gas valve as improper heating,
explosion, fire or asphyxiation may result.
Do not use matches, lighters, candles or other open flame to check for leaks. Use a soap
or water solution or a leak detector.
Do not pressure test the fuel system at more than 14” W.C. pressure once furnace has
been connected to the gas line. Overpressure may void the warranty and damage the
valve, which could cause an explosion, fire or asphyxiation.
6 of 22