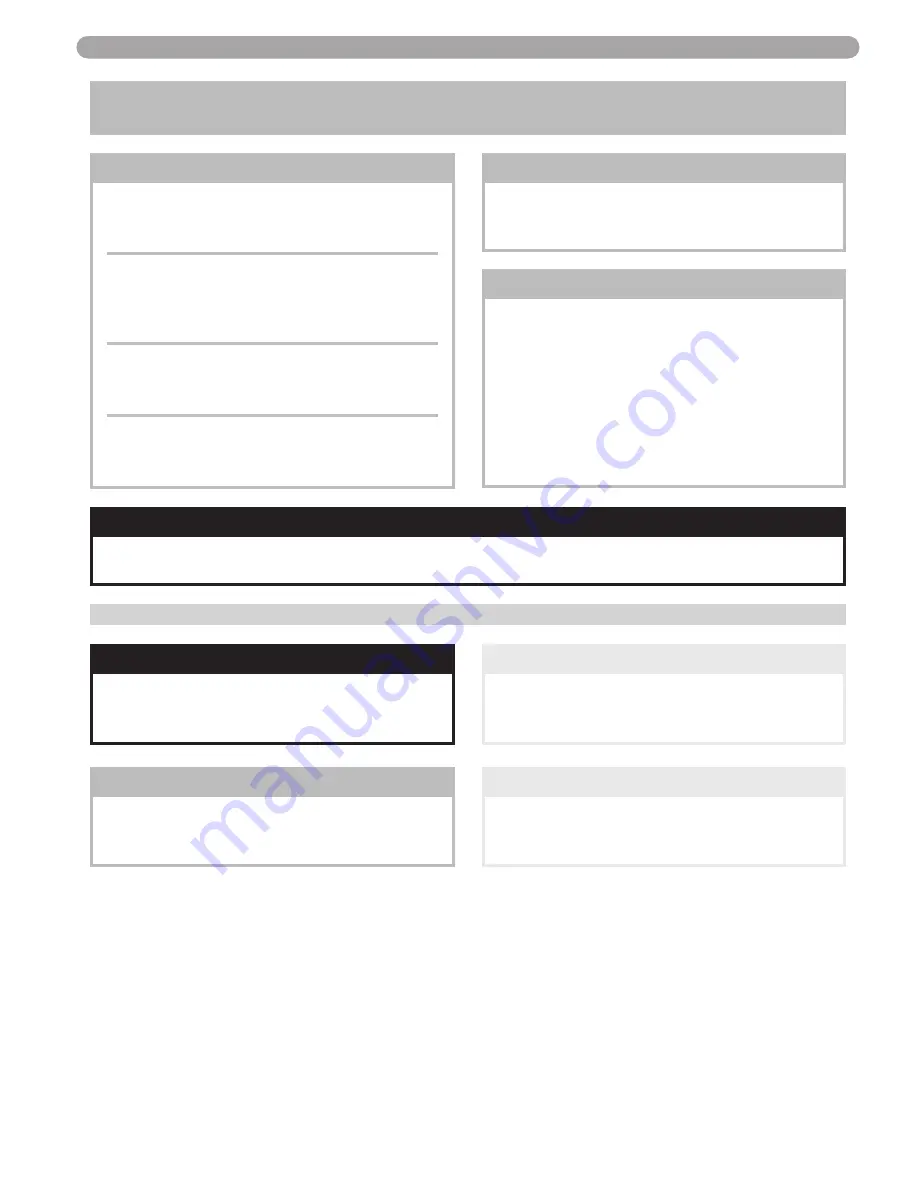
PRODUCT AND SAFETY INFORMATION
4
PART 1: PRODUCT AND SAFETY INFORMATION
n
WARNING
Installer
— Read all instructions in this manual,
and the Venting section, before installing.
Perform steps in the order given.
User
— This manual is for use only by a
qualified heating installer/service technician.
Refer to User’s Information Manual for your
reference.
User
— Have this appliance serviced/
inspected by a qualified service technician
annually.
Failure to comply with the above could result in
severe personal injury, death or substantial
property damage.
n
WARNING
Failure to adhere to the guidelines on this page
can result in severe personal injury, death or
substantial property damage.
n
WARNING
WHAT TO DO IF YOU SMELL GAS
• Do not try to light any appliance.
• Do not touch any electric switch; do not use
any phone in your building.
• Immediately call your gas supplier from a
neighbor's phone. Follow the gas suppliers'
instructions.
• If you cannot reach your gas supplier, call the
fire department.
SPECIAL ATTENTION BOXES
The following defined terms are used throughout this manual to bring attention to the presence of
hazards of various risk levels or to important information concerning the product.
n
DANGER
DANGER indicates an imminently hazardous
situation which, if not avoided, will result in
death or serious injury.
n
WARNING
WARNING indicates a potentially hazardous
situation which, if not avoided, could result in
death or serious injury.
n
CAUTION
CAUTION Indicates a potentially hazardous
situation which, if not avoided, may result in
minor or moderate injury.
CAUTION
CAUTION used without the safety alert symbol
indicates a potentially hazardous situation which,
if not avoided, may result in property damage.
DEFINITIONS
Summary of Contents for Phoenix Evolution
Page 71: ...70 ...
Page 72: ...71 ...
Page 73: ...72 MAINTENANCE NOTES ...
Page 74: ...73 MAINTENANCE NOTES ...
Page 75: ...74 MAINTENANCE NOTES ...
Page 76: ... 2009 Heat Transfer Products Inc www htproducts com LP 314 REV 12 21 09 ...