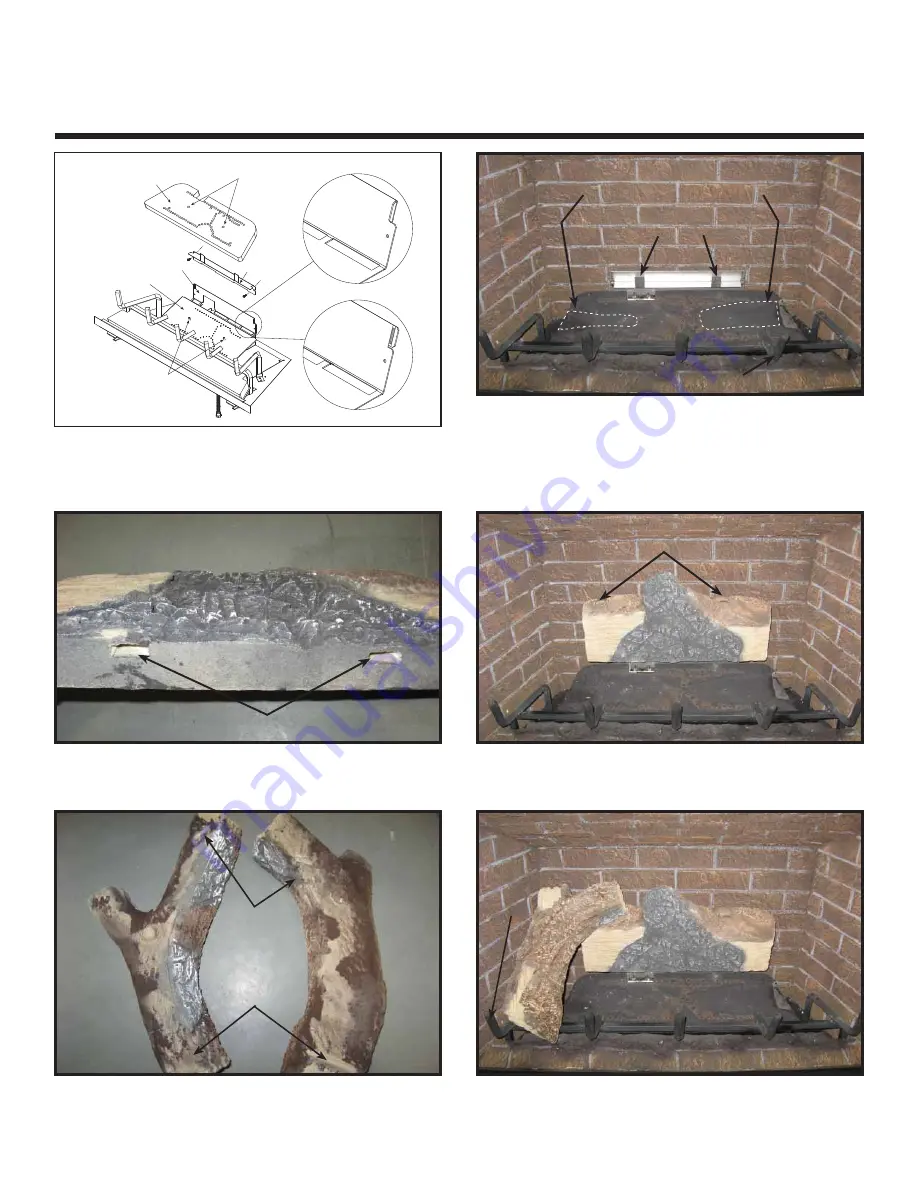
63
Heat & Glo • 6000C-IPI, 8000C-IPI • 2164-900 Rev. W • 8/14
Models: 8000C, 8000C-LP, 8000C-IPI,
8000C-IPILP, 8000CBV-IPI
Figure 3
Figure 4
GROOVES
GROOVES
SLOTS
SLOTS
Figure 5
Figure 6
1
1
22
11
LEFT GRATE TINE
LEFT GRATE TINE
CAUTION:
Logs are fragile, handle with care.
Log #1 (SRV2168-701)
: Locate log placement tabs on the pilot cover. Bend
tabs upward as shown in Figure 2. Locate the log placements slots on the bottom of Log # 1 (see Figure 3). Mate the slots
located on the bottom of Log #1 with the log placement tabs on the pilot cover. Log # 1 is properly installed when it sits
squarely and completely on pilot cover with tabs engaged. See Figure 4.
Figure 1
LOG PLACEMENT TABS
LOG PLACEMENT TABS
LOG PLACEMENT SLOTS
LOG PLACEMENT SLOTS
Log #2 (SRV2168-702)
: Mate the slot located on the bottom of Log #2 with the left log placement tab on top of Log #1.
After slot and tab have been
fi
tted together, mate the groove located on the bottom of Log #2 with the horizontal grate bar
and slide Log # 2 toward the left until it rests against the far left grate tine.
Figure 4 shows the log placement tabs located on the top of Log # 1. The tabs will be mated with the slots located on the
bottom of Log #2 and Log #3 (see Figure 5). Log #2 and Log #3 also have grooves that allow the logs to be seated properly
on the grate (see Figure 5). Hold Log #1 upright while placing Log #2.
LOG PLACEMENT INDENTATIONS
LOG PLACEMENT INDENTATIONS
GRATE TINE
GRATE TINE
LOG PLACEMENT TABS
LOG PLACEMENT TABS
33
22
Bottom view of
Bottom view of
Logs # 2 and 3
Logs # 2 and 3
GUIDE SLEEVES
FIBER BURNER TOP
TAB BENT IN = NG
TAB NOT BENT = LP
BURNER ASSEMBLY
PILOT COVER
LOCATING HOLES
BURNER SHIELD
Log Assembly: LOGS-8C
G. Install the Log Assembly
(continued)
Figure 2. Log Placement Tabs