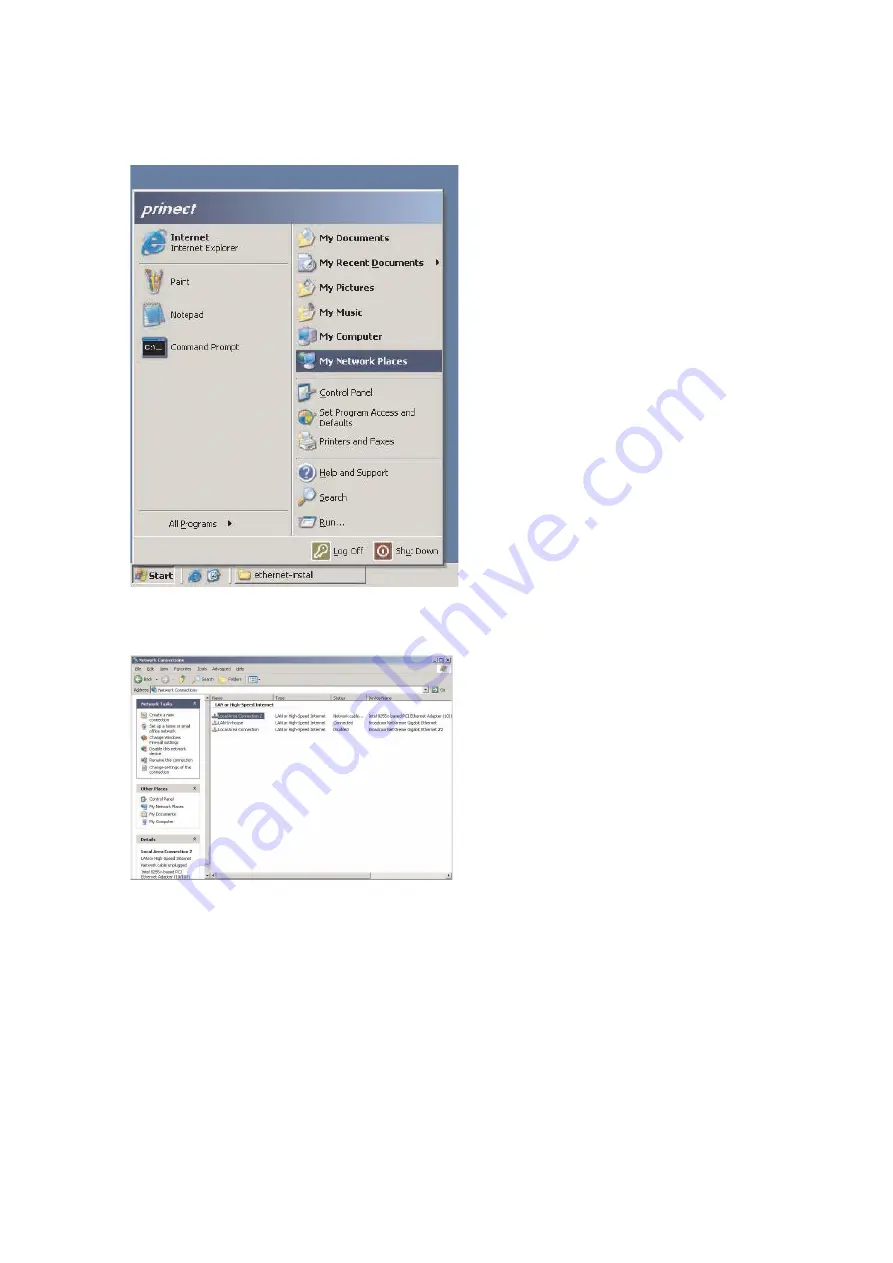
Installation
Suprasetter A52/A75 – Installation
Fig. 55 Network
Fig. 56 Network Connections
Select the network.
Select Network Connections and select "Local
Area Connection 2".
Summary of Contents for Suprasetter A52
Page 6: ......
Page 24: ...Safety 22 Fig 24 Filter replacement Fig 13 4 On the filter unit ...
Page 26: ...Safety 24 Fig 26 Warning sign copy template ...
Page 36: ...Installation Preparation 34 Pallet Installation Instructions ...
Page 82: ...Technical Data 80 Resolution 1000 pixels cm 2540 dpi Type Value Comment ...
Page 84: ......
Page 85: ......