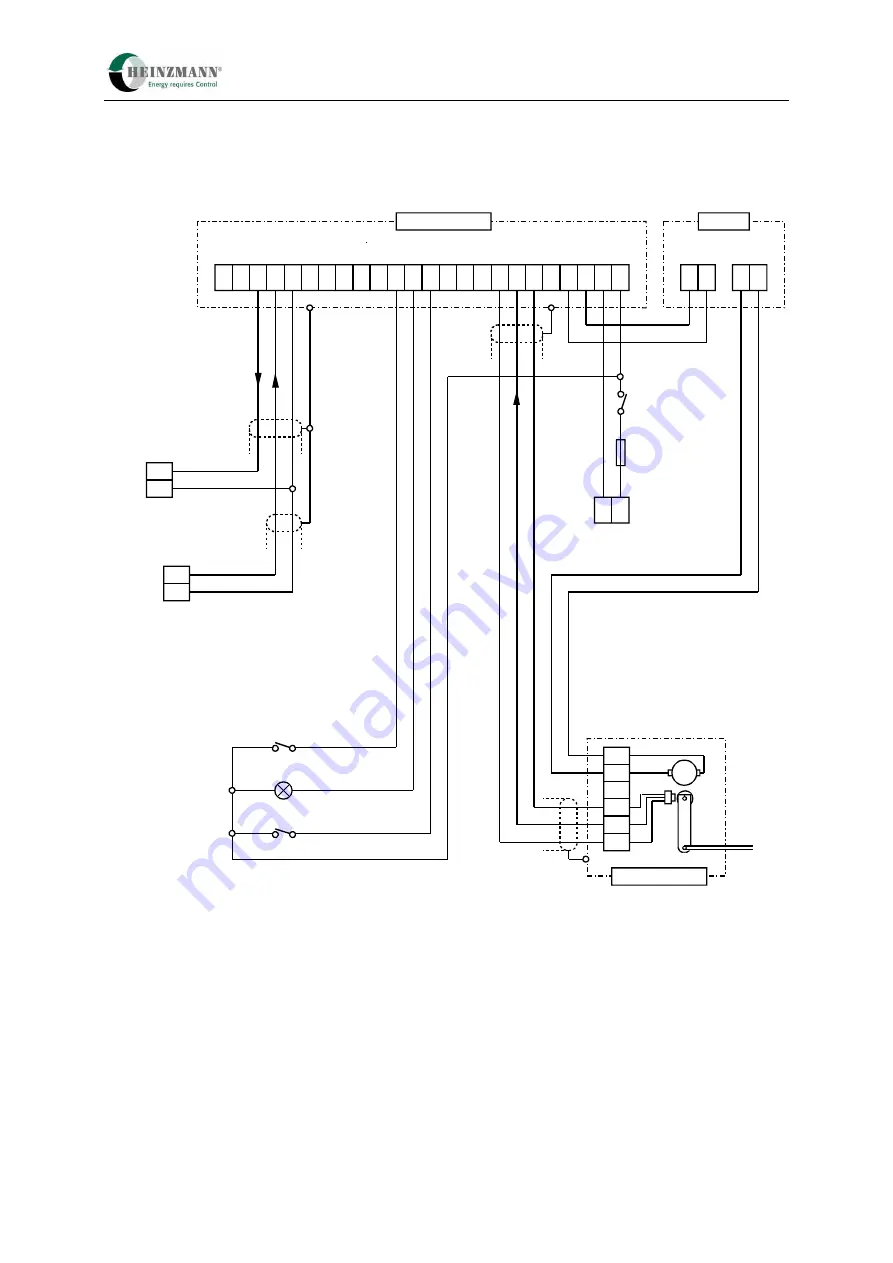
7 Technical data
44
Positioner DC 6-06
7.3.3
PWM setpoint, stop signal digital, actuator with disc rotor motor
2 3 4 5 6 7 8 9 10 11 12 13 14 15 16 17
T
18
C
B
D
A
E
M
DC ... 6-06
StG 6 .. 40 - 01
Actuator
Fuse
12 A
Control
on
Control unit
Common alarm
Stop digital
22 23
24 25
CU-01
1
L
H
19 20 21
StG actual position
with Analogue signal
or PWM signal
0 V
analog/PWM
PWM setpoint
Error reset
Supply voltage
12 V DC or 24 V DC
+
-
0 V
PWM
Fig. 4 Terminal connection diagram 3 – PWM setpoint, stop signal digital, actuator with disc rotor motor
Summary of Contents for PANDAROS DC 6-06
Page 2: ......