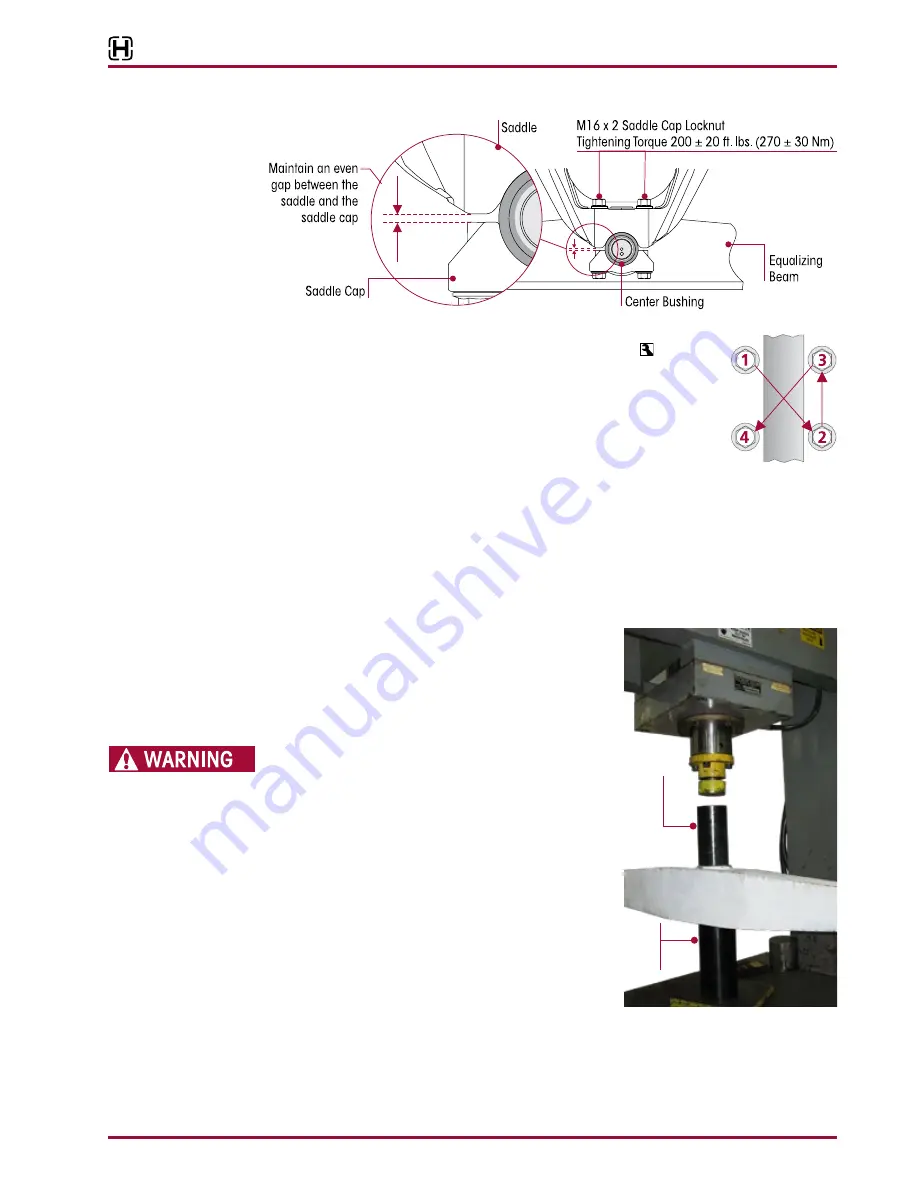
17730-299
41
Component Replacement
ULTIMAAX
®
for Fire and Rescue Vehicles
FIGURE 8-19
FIGURE 8-20
11 . Tighten the saddle cap fasteners evenly in several steps to 200 ± 20
foot pounds torque in proper sequence to achieve uniform bolt tension,
see Figure 8-20 .
12 . Install the tires .
13 . Remove the support from the axles and lower the vehicle onto the ground .
14 . Remove the wheel chocks .
EQUALIZING BEAM CENTER BUSHING
You will need:
■
Vertical shop press with a capacity of at least 100 Tons .
■
Center bushing tools – Receiving Tool No . 66086-112, Installation Tool No . 66086-107 and
Removal Tool No . 66086-110, see Special Tools Section of this publication .
FIGURE 8-21
DISASSEMBLY
1 . Remove the equalizing beam assembly
from the vehicle . Follow the equalizing
beam disassembly procedure in this
section .
DO NOT USE A CUTTING TORCH TO REMOVE
ANY FASTENERS OR BUSHINGS . THE USE
OF HEAT ON SUSPENSION COMPONENTS
WILL ADVERSELY AFFECT THE STRENGTH OF
THESE PARTS . A COMPONENT DAMAGED IN
THIS MANNER CAN RESULT IN THE ADVERSE
VEHICLE HANDLING AND POSSIBLE PERSONAL
INJURY OR PROPERTY DAMAGE .
2 . Place the equalizing beam assembly in
a shop press with the center hub firmly
supported on the receiving tool or on the
press, see Figure 8-21 .
3 . Install the center bushing removal tool,
ensure it is centered on the center
bushing .
4 . Push directly on center bushing removal tool until the center bushing is pressed out of the
equalizing beam bore, see Figure 8-21 .
5 . Inspect the beam bore .
Equalizing Beam Assembly
Center Bushing
Removal Tool
Part No. 66086-110
Center Bushing
Receiving Tool
Part No. 66086-112