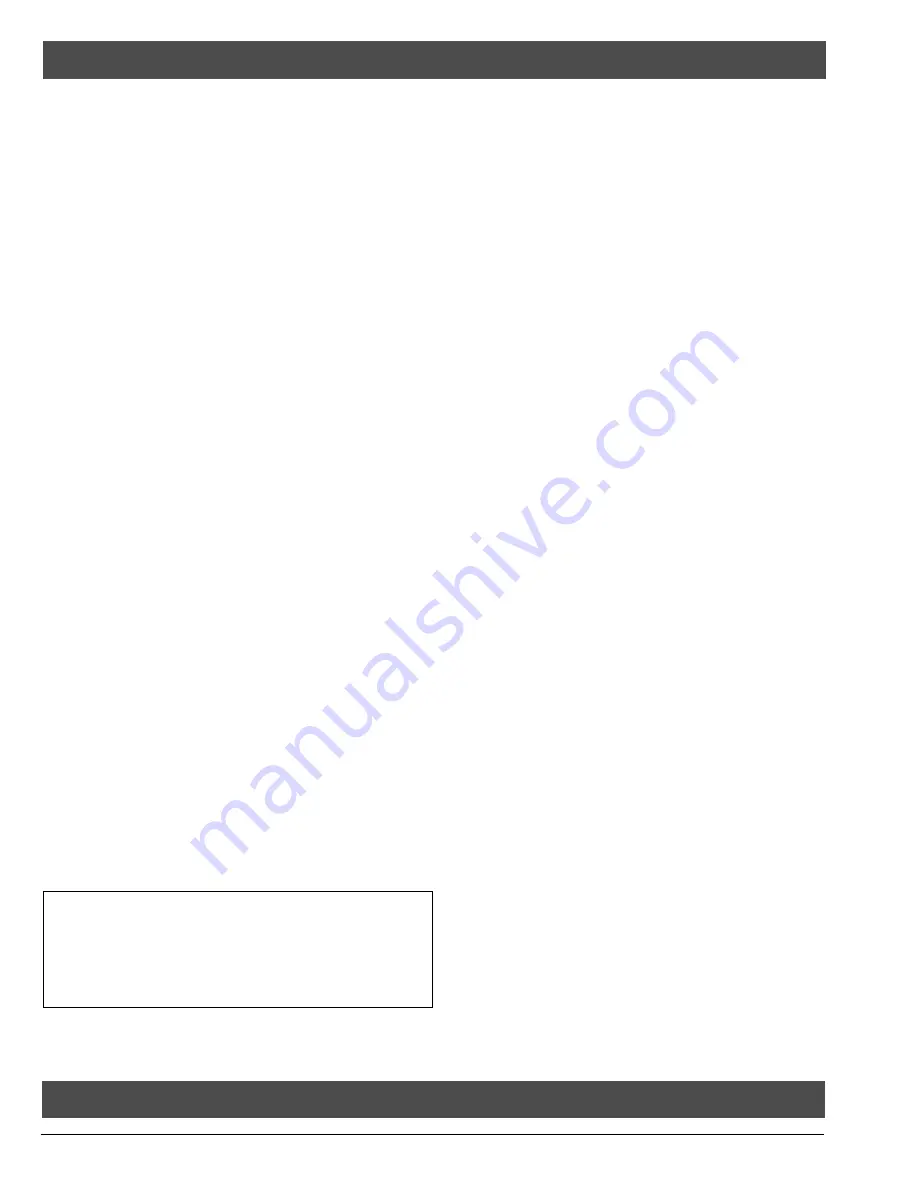
vi • AMMCO 800 On-The-Vehicle Brake Lathe
SAVE THESE INSTRUCTIONS
READ ALL INSTRUCTIONS
When using your portable garage equipment, basic
safety precautions should always be followed, includ-
ing the following:
1.
KEEP GUARDS IN PLACE and in working order.
2.
REMOVE ADJUSTING KEYS AND WRENCHES
from the tool before turning it on. Make this a habit.
3.
KEEP WORK AREA CLEAN and well lighted.
Cluttered areas and benches invite accidents.
4.
LOCATE POWER CORD SAFELY. Do not let cord
hang over edge of table, bench or counter or
come in contact with hot manifolds or moving fan
blades.
5.
REDUCE RISK OF FIRE. Do not operate equip-
ment in the vicinity of open containers of flamma-
ble liquids (gasoline) and their vapors.
6.
PROVIDE ADEQUATE VENTILATION when work-
ing on operating internal combustion engines.
7.
DRESS PROPERLY. Keep hair, loose clothing,
neckties, shop rags, jewelry, fingers, and all parts
of body away from moving parts. Non-slip
footwear is recommended.
8.
ALWAYS UNPLUG EQUIPMENT from electrical
outlet when not in use. Never use the cord to pull
the plug from the outlet. Grasp plug and pull to
disconnect.
9.
LET EQUIPMENT COOL completely before put-
ting away. Loop cord loosely around equipment
when storing.
10.
DO NOT TOUCH HOT PARTS. Care must be taken
as burns can occur from touching hot parts.
11.
PROPERLY MAINTAIN EQUIPMENT. Do not oper-
ate equipment with a damaged cord or if the
equipment has been dropped or damaged—until it
has been examined by a qualified serviceman.
12.
USE PROPER EXTENSION CORD. A cord with a
current rating equal to or more than that of the
equipment should be used. Cords rated for less
current than the equipment may overheat. Care
should be taken to arrange the cord so that it will
not be tripped over or pulled.
13.
REDUCE RISK OF SHOCK. Do not use on wet sur-
faces or expose to rain.
14.
KEEP CHILDREN AND UNAUTHORIZED PER-
SONNEL AWAY. All bystanders should be kept
completely away from the work area.
15.
MAKE WORKSHOP CHILD PROOF. Use padlocks
and master switches, and remove starter keys.
16.
DON’T FORCE TOOL. It will do the job better and
safer at the rate for which it was designed.
17.
USE RIGHT TOOL. Don’t force a tool or an attach-
ment to do a job for which it was not designed.
18.
ALWAYS USE SAFETY GLASSES. Everyday eye-
glasses only have impact resistant lenses, they
are NOT safety glasses. Safety glasses, goggles,
or a face shield will help protect the operator from
injury. Use a face shield and dust mask during
dusty operations.
19.
SECURE WORK properly to the unit for setup and
tool bit positioning. Do not attempt to hold a rotor
steady with your hands. Both hands must be free
to operate unit. When turning drive wheels,
secure opposite wheel during rotor resurfacing.
20.
DON’T OVERREACH. Keep proper footing and
balance at all times.
21.
MAINTAIN TOOLS WITH CARE. Keep tools sharp
and clean for best and safest performance. Follow
instructions for lubricating and changing acces-
sories.
22.
REMOVE POWER AND DISCONNECT TOOLS
before servicing the unit and when changing
accessories such as blades, bits, cutters, etc.
Follow lock-out and tag-out procedures as
required.
23.
AVOID UNINTENTIONAL STARTING. Make sure
the switch is in the OFF (O) position before plug-
ging the machine in or performing any mainte-
nance or service work.
24.
USE RECOMMENDED ACCESSORIES. The use
of improper accessories may cause risk of injury
to operator or bystanders. Use only as described
in this manual. Use only manufacturer’s recom-
mended attachments.
25.
NEVER LEAN OR STAND ON A LATHE. Serious
injury could occur if the lathe is tipped or if the cut-
ting tool is unintentionally contacted.
Before operating the lathe, review the warning information on the lathe and the cautions, warnings and dangers
in this manual. Also review the following general safety instructions. Failure to follow safety instructions could
result in personal injury to operator or bystanders and damage to the lathe or personal property.
IMPORTANT SAFETY INSTRUCTIONS