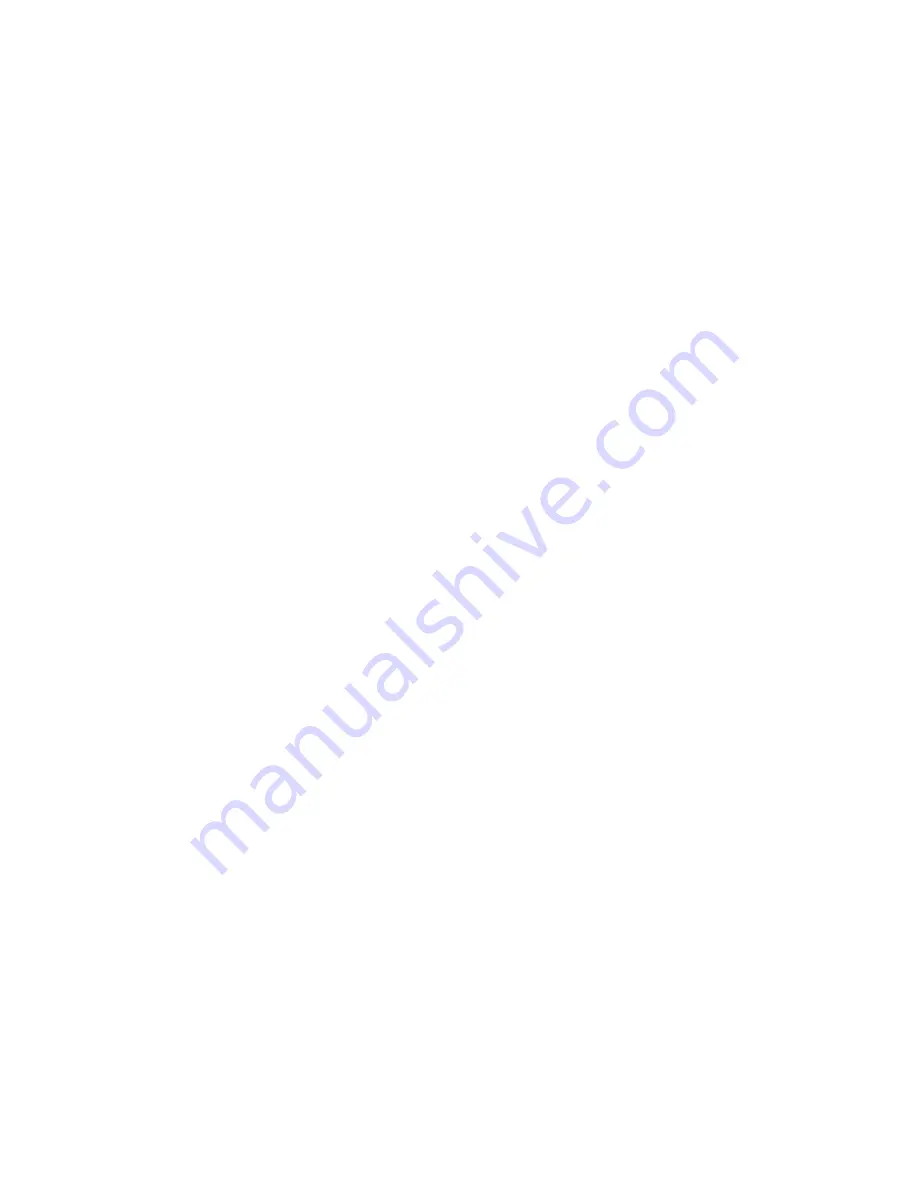
H.E.R.O. INDUSTRIES LTD.
330SES / 330SEL MANUAL - “B” VERSION
14
TROUBLESHOOTING
PAINT OUTGO VALVE (REF# 32, PART # 4-11A)
The paint outgo valve monitors and controls the flow of spray materials as it leaves the sprayer. It also
works together with the paint intake valve, to build paint pressure as specified by the setting made by the
hydraulic outgo valve (pressure control valve). A worn outgo valve will result in pulsation in the spray
material and cause the paint hose to jump and vibrate vigorously.
PRIME VALVE (REF# 49, PART # 4-606)
The prime valve is used at the beginning and end of the spray operation (see "setting up to spray"). The
function of the prime valve is to assist in removing air from the paint pump when beginning to spray. It is
necessary to remove all air from the paint pump so that the spray material can replace it. The pump will
function without the prime valve, however, the initial priming procedure would require considerably longer
to complete. During the priming procedure the hydrapulse membrane is exposed to its greatest amount of
stress. Use of the prime valve and a lightweight thinner, which is compatible with the intended spray
material, will reduce hydrapulse membrane stress and reduce priming time. The prime valve will also allow
you to remove any unused paint left in the pump and hose at the completion of a job. When the prime valve
is open the material is pumped through the paint intake and outgo and back to the source by way of the prime
valve. When closed, no material should be escaping from the prime valve return hose (ref# 50). If material
escapes through the prime valve return hose, when the valve is closed, spray pressure at the gun will be
reduced.
The solution to almost all problems can usually be found in the paint side valves. However, before
performing any repair or looking further, the following are things which can cause an apparent sprayer
failure, without any mechanical problem. ALWAYS check these items before preceding.
1. Circuit breaker open or fuse blown . 9. Gun handle filter plugged.
2. Motor not plugged in. 10. Paint hose plugged.
3. Motor not switched on. 11. Loose fitting or hole in siphon hose.
4. Motor thermal reset popped. 12. Intake siphon hose plugged.
5. Too light or too long of an extension cord. 13. Siphon screen missing or plugged.
6. Pressure control knob loose or missing. 14. Sprayer under pressure when restarting.
7. Spray tip plugged. 15. Strainer bag plugging siphon screen.
8. Spray tip worn out.
UNLESS YOU ARE KNOWLEDGEABLE ABOUT THE REPAIR OF HIGH PRESSURE
EQUIPMENT, DO NOT ATTEMPT TO REPAIR AN AIRLESS SPRAYER YOURSELF. ALWAYS
FOLLOW ALL SAFETY PRECAUTIONS. THE H.E.R.O. SERVICE VIDEO TAPE (1-620-VHS OR 1-
620-BETA) WILL PROVIDE COMPLETE SERVICE TRAINING. SEE YOUR H.E.R.O.
DISTRIBUTOR TO PURCHASE A COPY.