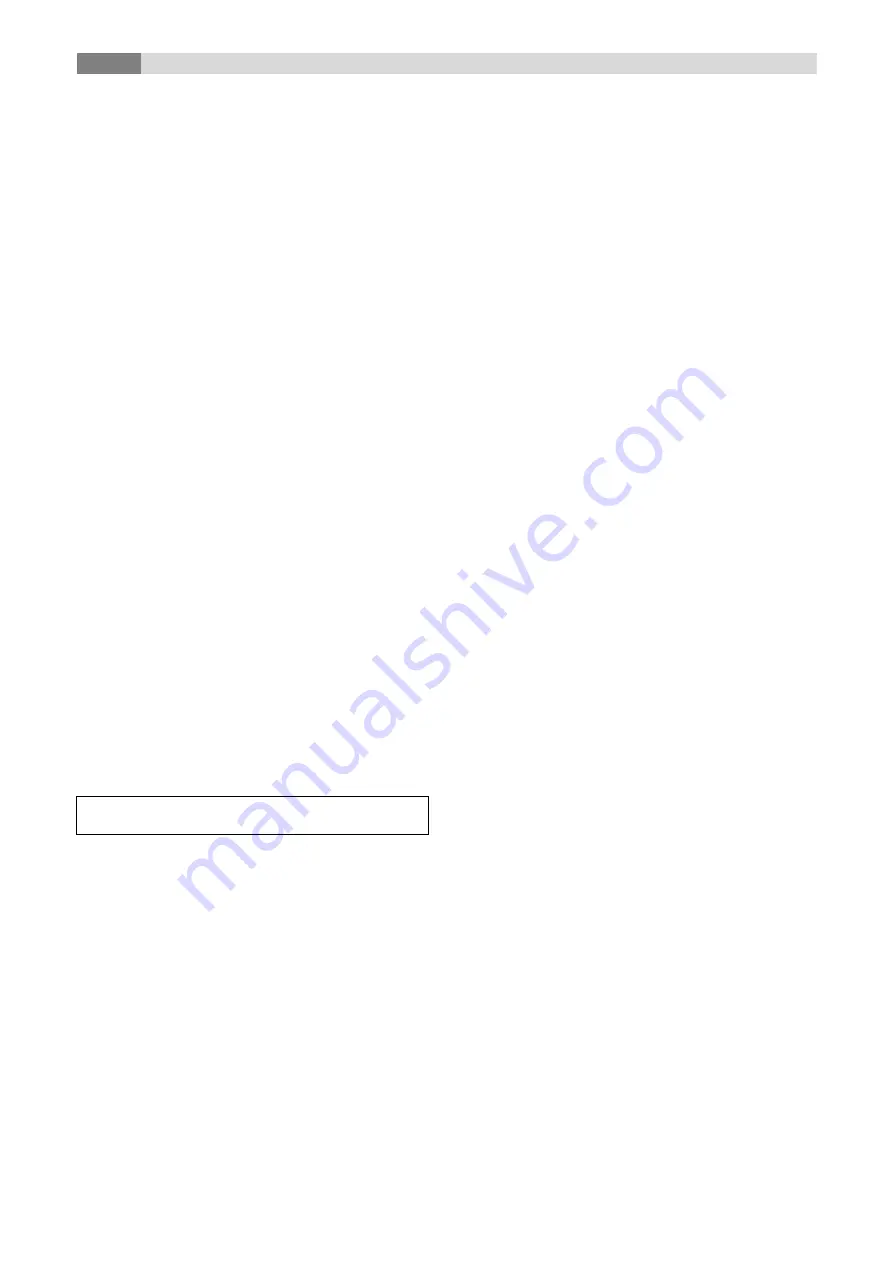
4
Safety devices
8
4
SAFETY DEVICES
The safety devices must be dimensioned and installed according to EN 12828.
The safety valve in the boiler circulation serves as a final safety device against malfunctions of the
equipment.
All legal safety regulations must be adhered to on-site via the authorised specialist company.
Earthing or potential equalisation must be carried out on the whole heating system according to EN 60204-1
by an authorised specialist company.
1 Safety temperature limiter
If the boiler temperature exceeds 95 °C, the
equipment must be switched off for safety
reasons. The safety temperature limiter (STL) will
lock in this case.
Possible causes may be:
◼
Performance decrease in the boiler was
interrupted abruptly. This can occur due to
the switching off a pump or sudden
shutting of the heating circuit mixer.
◼
The load pumps are being controlled by
the HERZ Control. The so-called excess
temperature
flue
gas
would
be
automatically activated by the HERZ
Control.
This
avoids
higher
boiler
temperatures.
◼
The boiler is too large.
◼
The fuel level is set too high.
◼
Loss of power supply
◼
Etc.
At First the cause of the failure must be found and
be corrected, afterwards the safety temperature
limiter can be unlocked.
The boiler temperature must be lower than 75
°C before unlocking.
Only then the problem can be acknowledged. For
this purpose, the cover of the STL is screwed off.
The STL can be unlocked by a light pressure with
a sharp object. After unscrewing the cover the
fault acknowledgement must be performed at the
switch box. The location of the STL is on the left
side next of the display.
2 and 3 automated extinguishing device
The Boiler features an automated extinguishing
device. The device consists of a thermal safety
valve, a thermostat valve (3) and a water tank (2).
If the feeding screw temperature gets exceeded,
the valve opens independently and flushes the
feeding pipe. This extinguishing device is used as
a safety device at burn back.
4 Burn-back safety unit
The burn-back safety unit prevents a burn-back
into the fuel storage room. It separates
additionally the combustion chamber and the fuel
storage room. The burn-back safety unit (or cell
wheel sluice) is conducted like a fire flap. It opens
only when fuel is fed to the boiler.
5 Safety valve
The safety valve automatically releases, when the
pressure or temperature exceeds preset limits.
The safety valve has to release at the maximum
allowable pressure (according to boiler plate).
6 Safety heat exchanger
The safety heat exchanger is a built-in safety
device and has to be connected to a thermal
release valve and installed, according to applied
standards. The safety heat exchanger has to be
connected directly to a cold water pipe (pressure
≤ 3 bar)
7 Ash container and burning chamber safety
device
The ash containers are connected contact-free
(inductive sensor) to the boiler.
Fuel storage room temperature monitoring
The fuel storage room temperature monitoring is
placed directly above the transport screw. There
is placed a temperature sensor which is setting to
the release temperature. If the storage room
temperature exceeds its preset limit, the boiler will
switch to the operate condition „HEATING OFF“
and displays a fault report. Additionally, a fault
sensor output gets active. Conduct alerting in
accordance with national standards.
Summary of Contents for firematic CONDENSATION 30
Page 1: ...OPERATING INSTRUCTIONS Wood chips pellets heating system firematic CONDENSATION 30 40 ...
Page 83: ...Annex 15 83 15 ANNEX 15 1 Additional boiler module Hydraulic recommendation 1 ...
Page 84: ...15 Annex 84 Hydraulic recommendation 2 ...
Page 85: ...Annex 15 85 15 2 Solar module Program 1 ...
Page 86: ...15 Annex 86 Program 2 ...
Page 87: ...Annex 15 87 Program 3 ...
Page 88: ...15 Annex 88 Program 4 ...
Page 89: ...Annex 15 89 Program 5 ...
Page 90: ...15 Annex 90 Program 6 ...
Page 91: ...Notes 16 91 16 NOTES ...