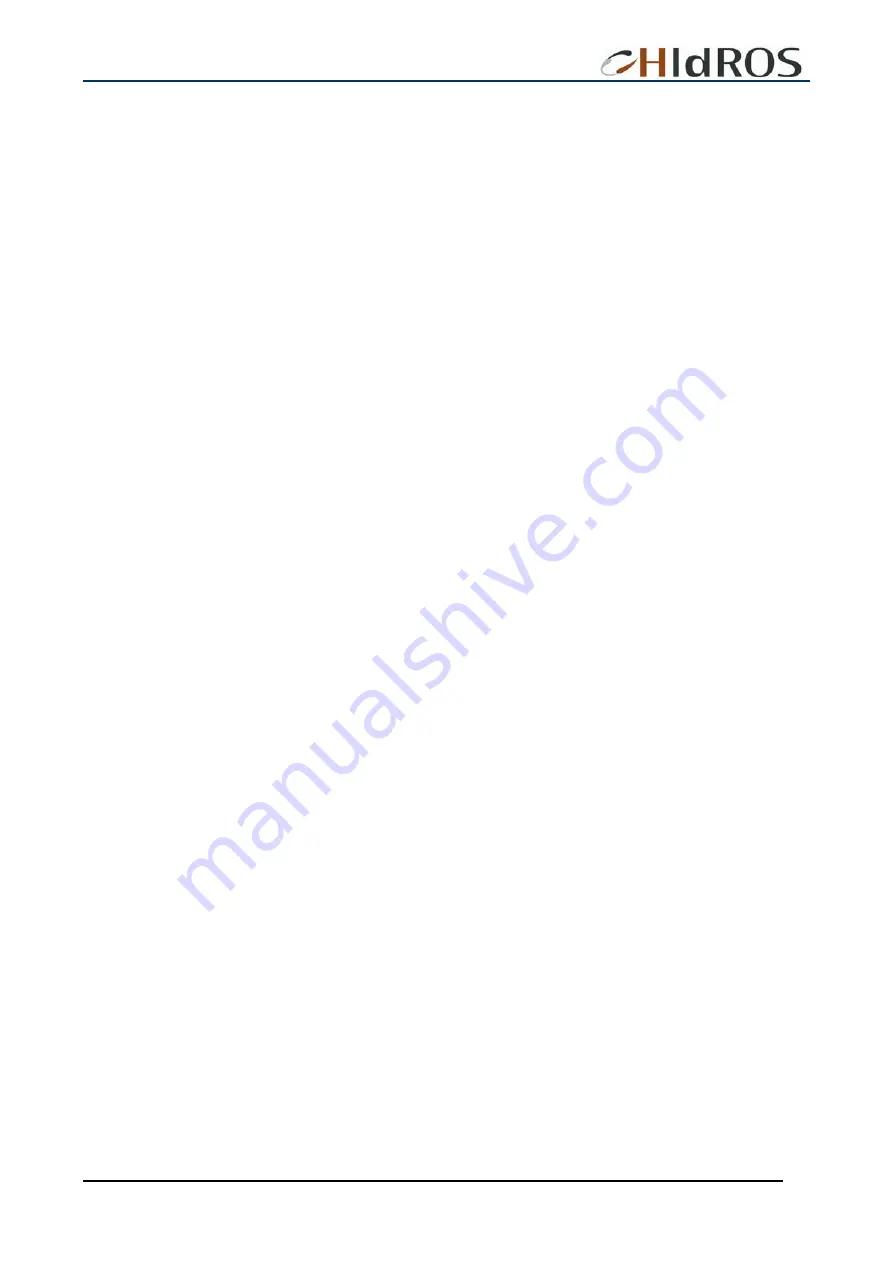
SRH
Swimming Pools Dehumidifiers
MTSRHGB
9
REV.072008
TECHNICAL CHARACTERISTICS
SRH dehumidifiers series are highly performances units designed for swimming pool applications where it is necessary to control
humidity and to prevent condensation to guarantee optimal comfort.
Frame
All SRH units are made from hot-galvanised thick sheet metal, painted with polyurethane powder enamel at 180°C to ensure the
best resistance against the atmospheric agents. The frame is self-supporting with removable panels. All screws and rivets are in
stainless steel. The colour of the units is RAL 7035
Refrigerant circuit
The refrigerant gas used in these units is R407C. The refrigerant circuit is made by using international primary brands components
and according to ISO 97/23 concerning welding procedures. All units are supplied with two circuits, each refrigerant circuit is totally
independent from the other. Any incorrect operation of one circuit does not influence the other circuit. The refrigerant circuit includes:
SRH
liquid line manual shut-off valve, sight glass, filter drier, thermal expansion valve with external equalizer, Schrader valves
form maintenance and control, pressure safety device (according to PED regulation).
SRH/WZ
these versions are supplied with one refrigerant circuit identical to the SRH version, the second circuit includes: one way
valves, solenoid valves, liquid receiver, water heat recovery, liquid line shut-off valve, sight glass, filter drier, thermal expansion valve
with externalequalizer, Schrader valves formaintenance andcontrol,pressuresafety device.
Compressors
The compressors are scroll type with crankase heater and thermal overload protection by a klixon embedded in the motor winding.
The compressors are mounted on rubber vibration dampers and they can be supplied wih sound attenuation jacket to reduce the
noise emission (option). The compressor crankcase heater is always powered when the unit is in stand-by. The inspection on the
compressors is possible only through the unit front panel.
Condensers and evaporators
Condensers and evaporators are made of copper pipes and aluminium fins. All evaporators are painted with epoxy powders to
prevent corrosion problem due to their use in aggressive environments.The diameter of the copper pipes is 3/8” and the thickness of
the aluminium fins is 0,1 mm. The tubes are mechanically expanded into the aluminium fins to improve the heat exchange factor.
The geometry of these heat exchangers guarantees a low air side pressure drop and then the use of low rotation (and low noise
emission) fans. All units are supplied, standard, with a Stainless steel drip tray and all evaporators are supplied with a temperature
sensor used as automatic defrost probe.
Heat recovery
It is supplied on the SRH/WZ, factory mounted, it is composed by a plate heat exchanger in molibdenum alloy, suitable for operation
with chlorine water; the heat recovery is designed to reject on water about 50% of the total thermal load generated by the unit. When
the heat recovery is activated, the supply air temperature of the unit is, basically, the same of the return air.
Fans
The fans are made of galvanized steel, centrifugal type, double inlet with forward curved blades. They are statically and dynamically
balanced and supplied complete of the safety fan guard according to EN 294. They are mounted on the unit frame by interposition of
rubber vibration dampers. The electric motors are 4 poles (about 1500 rpm), three-phase power supply. The motors are connected to
the fans by pulleys and belts. The protection class of the motors is IP 54.
Air Filter
Supplied as standard with the unit, it is made of G3 class sysnthetic fibre filtering media (efficiency 85% by weight), 48 mm
thickness.
Electric enclosure
The electric switch board is made according to electromagnetic compatibility norms CEE 73/23 and 89/336. The accessibility to the
board is possible after removing the front panel of the unit and the OFF positioning of the main switch. The moisture protection
degree is IP55. In all SRH units are installed, standard, the compressors sequence relay who disables the operation of the
compressor in case the power supply phase sequence is not the correct one (scroll compressors in fact, can be damaged if they
rotate reverse wise). The following components are also standard installed: main switch, magnetic-thermal switches (as a protection
fans and compressors), control circuit automatic breakers, compressor contactors, fan contactors. The terminal board is supplied
with voltage free contacts for remote ON-OFF and general alarm.
Summary of Contents for SRH Series
Page 1: ...SWIMMING POOLS DEHUMIDIFIERS SRH SERIES TECNICAL MANUAL ...
Page 2: ...SRH Swimming Pools Dehumidifiers MTSRHGB 2 REV 072008 ...
Page 3: ...SRH Swimming Pools Dehumidifiers MTSRHGB 3 REV 072008 ...
Page 4: ...SRH Swimming Pools Dehumidifiers MTSRHGB 4 REV 072008 ...
Page 40: ......
Page 41: ......
Page 42: ......
Page 43: ......
Page 44: ......
Page 45: ......
Page 46: ......
Page 47: ......
Page 48: ......
Page 49: ......
Page 50: ......
Page 51: ......
Page 52: ......
Page 53: ......
Page 54: ......
Page 55: ......
Page 56: ......
Page 57: ......
Page 58: ......
Page 59: ......
Page 60: ......
Page 61: ......
Page 62: ......
Page 63: ......