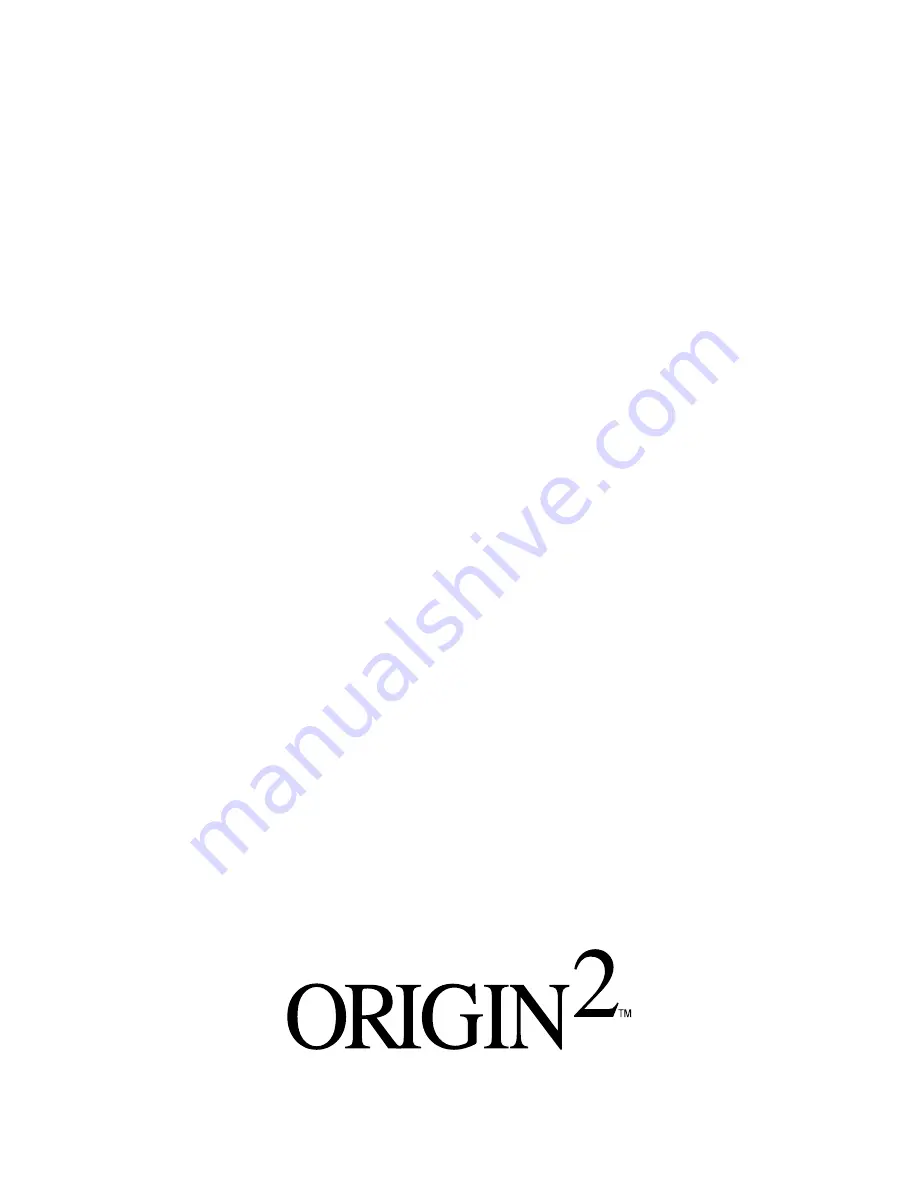
GENERAL INFORMATION
DESCRIPTION OF CASES
: The refrigerated display cases described in this handbook
are part of the
Hill PHOENIX
,
Origin2
design series. Specifically covered in this manual is
model OSAA, self-contained service deli case.
STORE CONDITIONS
:
Hill PHOENIX
cases are designed to operate in an air conditioned
store with a system that can maintain 75
O
F (24
O
C) store temperature and 55 percent (maxi-
mum) relative humidity (CRMA conditions). Case operation will be adversely affected by
exposure to excessively high ambient temperatures and/or humidity.
REFRIGERATION SYSTEM OPERATION
: Air cooled condensing units require ventilation for
efficient performance of condensers. Machine room temperatures must be a minimum of
65
O
F in winter and a maximum of 95
O
F in summer. Minimum condensing temperatures
should be no less than 70
O
F.
RECEIVING CASES
: Examine fixtures carefully for shipping damage and shortages. For
information on shortages contact the Service Parts Department at 1-800-283-1109.
APPARENT DAMAGE
: A claim for obvious damage must be noted on the freight bill or
express receipt and signed by the carriers agent, otherwise the carrier may refuse the claim.
CONCEALED DAMAGE
: If damage is not apparent until after the equipment is unpacked,
retain all packing materials and submit a written request to the carrier for inspection within
15 days of receipt of equipment.
LOST ITEMS
: This equipment has been carefully inspected to insure the highest level of
quality. Any claim for lost items must be made to
Hill PHOENIX
within 48 hours of receipt
of equipment.
TECHNICAL SUPPORT
: If any technical questions arise regarding a refrigerated display
case contact our Customer Service Department in Richmond at 1-804-526-4455. For any
questions regarding our refrigeration systems or electrical distribution centers contact our
Customer Service Department in Conyers at 1-770-285-3200.
CONTACTING FACTORY
: Should you need to contact
Hill PHOENIX
regarding a specific
fixture, be sure to know the case model number and serial number. This information is on
the serial plate located on the rear panel of the case (see next page for details). Ask for a
Service Parts Representative at 1-804-526-4455.
2
Summary of Contents for Origin2 OSAA
Page 1: ...DELI C A S E S MODEL OSAA HANDBOOK INSTALLATION OPERATION 9 03 P061773M...
Page 2: ......
Page 4: ......
Page 29: ...25 NOTES...
Page 30: ...26 NOTES...