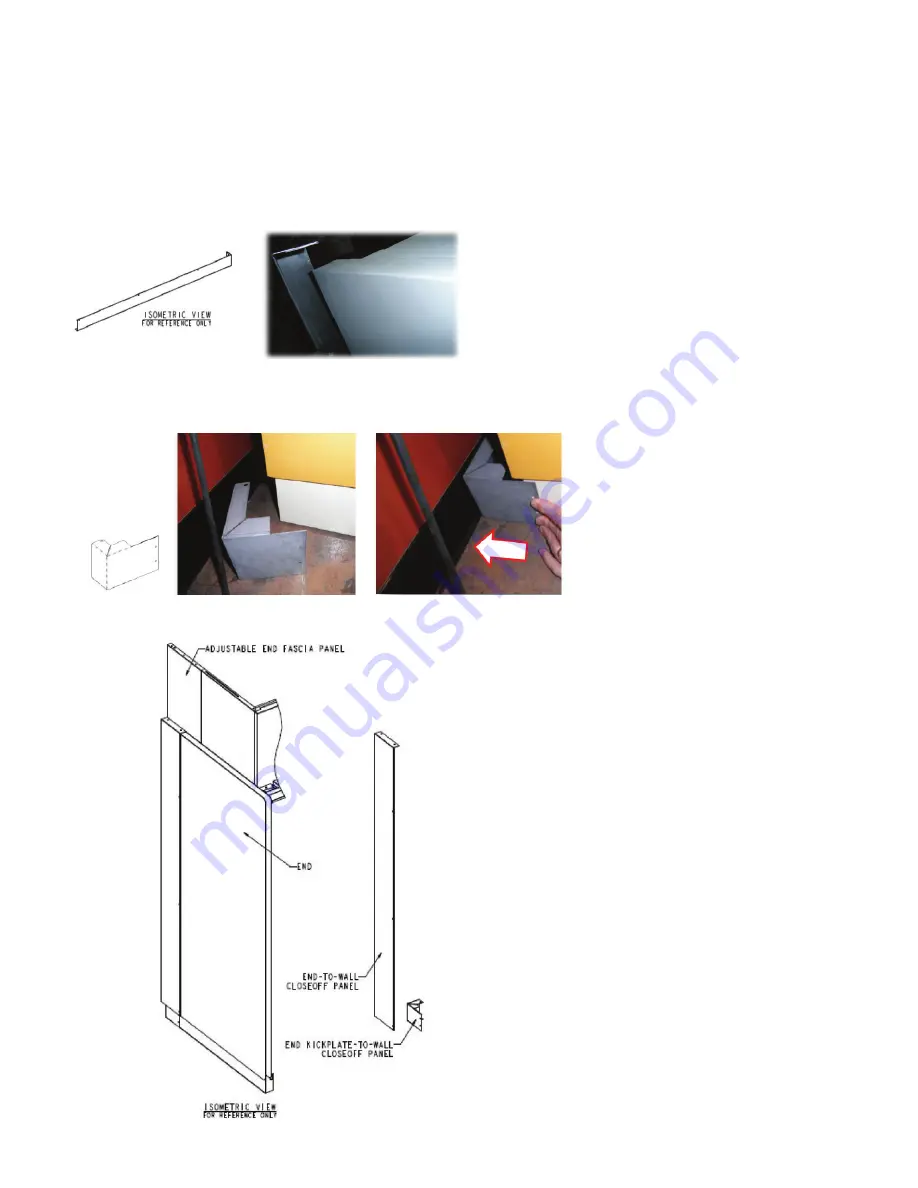
H1: END TO WALL CLOSE-OFF PANELS
If ordered, the 4 shipped-loose items, trims from the ends of the case to the wall behind.
Close-off panel: Insulated End to Wall Right Hand shown. Nominal 77” Height. Hemmed top rests on
top of insulated end panel. Slide back to close any gaps to the wall behind. Fasten with #8 screws at
holes provided.
Close-off panel: End kick-plate to Wall. Nominal 7” x 5” x 3” (same part right / left ).
Summary of Contents for JNRBHSA
Page 2: ...ii ...
Page 33: ...B2 SEISMIC BRACKETS 5 BRACKETS ...
Page 34: ...C1 SPORLAN PRESSURE TEMPERATURE CHART ...
Page 38: ...Display Cases 5XIILQ 0LOO 5RDG RORQLDO HLJKWV 9 E3 ELECTRICAL WIRING DIAGRAM ...
Page 39: ...Display Cases 5XIILQ 0LOO 5RDG RORQLDO HLJKWV 9 E4 ELECTRICAL WIRING DIAGRAM ...
Page 46: ...G1 FASCIA FRAME ...
Page 47: ...G2 FASCIA FRAME ...
Page 48: ...G3 FASCIA FRAME ...
Page 49: ...G4 FASCIA FRAME ...
Page 50: ...G5 FASCIA FRAME OPTIONAL MOTION SENSOR INSTALLATION ...
Page 51: ...G6 FASCIA FRAME OPTIONAL MOTION SENSOR INSTALLATION ...
Page 53: ...G8 FASCIA FRAME JNRZHSA 5 BALLOON GUARD INSTALLATION ...
Page 55: ...I1 CASE LIFTING LOCATIONS Base Frame Lifting Locations for Forklift JNRBHSA JNRZHSA ...
Page 56: ...I2 CASE LIFTING LOCATIONS Base Frame Lifting Locations for Forklift JNRBHSA JNRZHSA ...
Page 57: ...v Ϯ Z Ͳ ϱ Z EZ v Ϯ Z Ͳ ϰ Z EZ v ϱ EZ J1 CONDENSING UNIT LOCATIONS ...