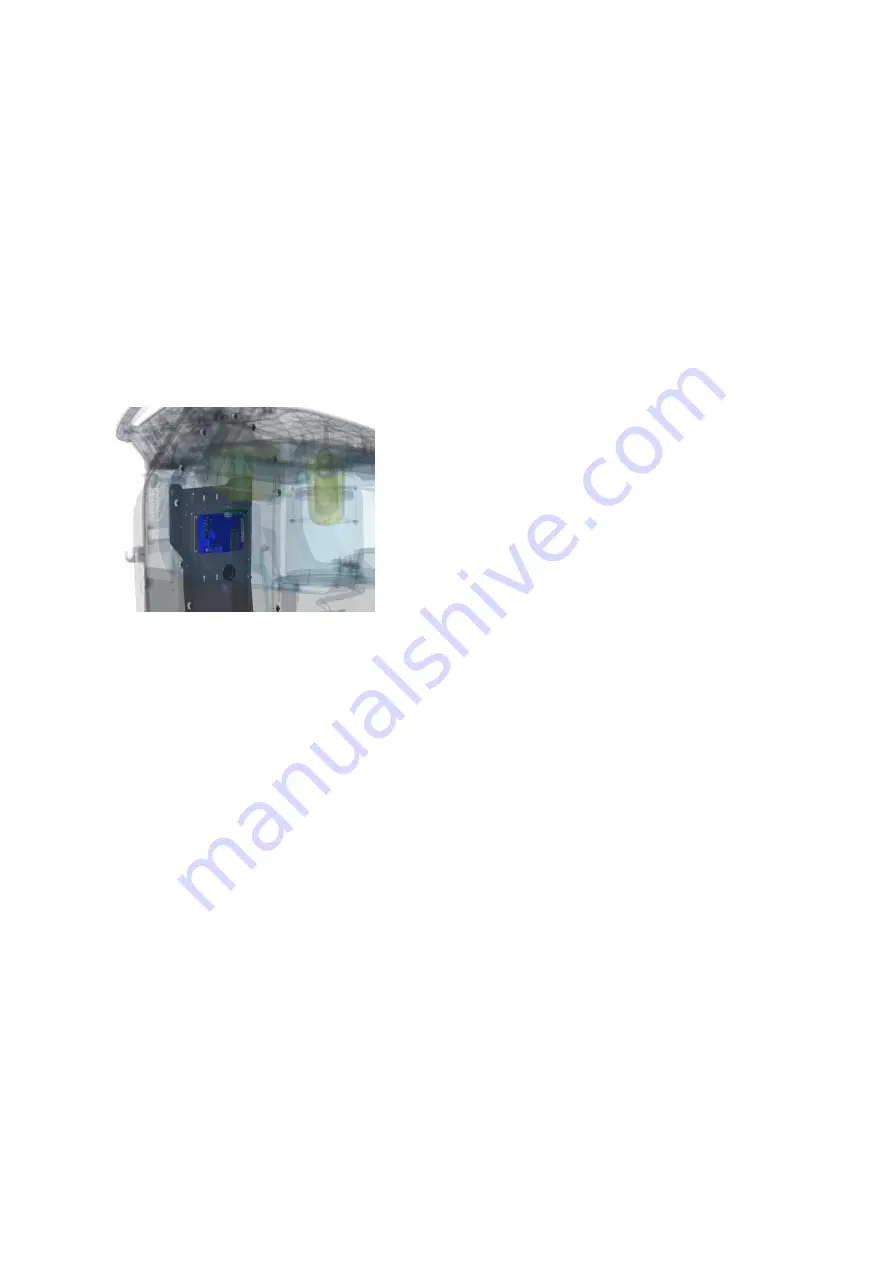
Chapter 5
Electrical System
5.1
Structure T20SC PRO
Figure 5.1: Electrical System T20SC PRO
5.2
Description
T20SC
PRO
A main board
runs all the functions of
the machine, washing, drying, traction
and braking.
The main board
receive as input, all the
information from the control board, the
safety microswitch and all the electronic
devices of the machine.
These signals
are translated from the
main board to run correctly the scrubber
dryer and to prevent any safety problem
to the operator.
The dash board
can be used also as
a programmer console to
modify
the
parameter of all the machine’s functions
(washing, drying and traction) and, also,
to
check in real time
:
- The battery status
- The consumption of the motors
29
Summary of Contents for TRIDENT T20SC PRO
Page 1: ...SERVICE MANUAL TRIDENT T20SC PRO Version AB Date November 7 2018 Document Number 10077483...
Page 4: ...Part I Product Introduction 4...
Page 8: ...Part II Anomalies Resolution Guide 8...
Page 28: ...Part III Machine Description 28...