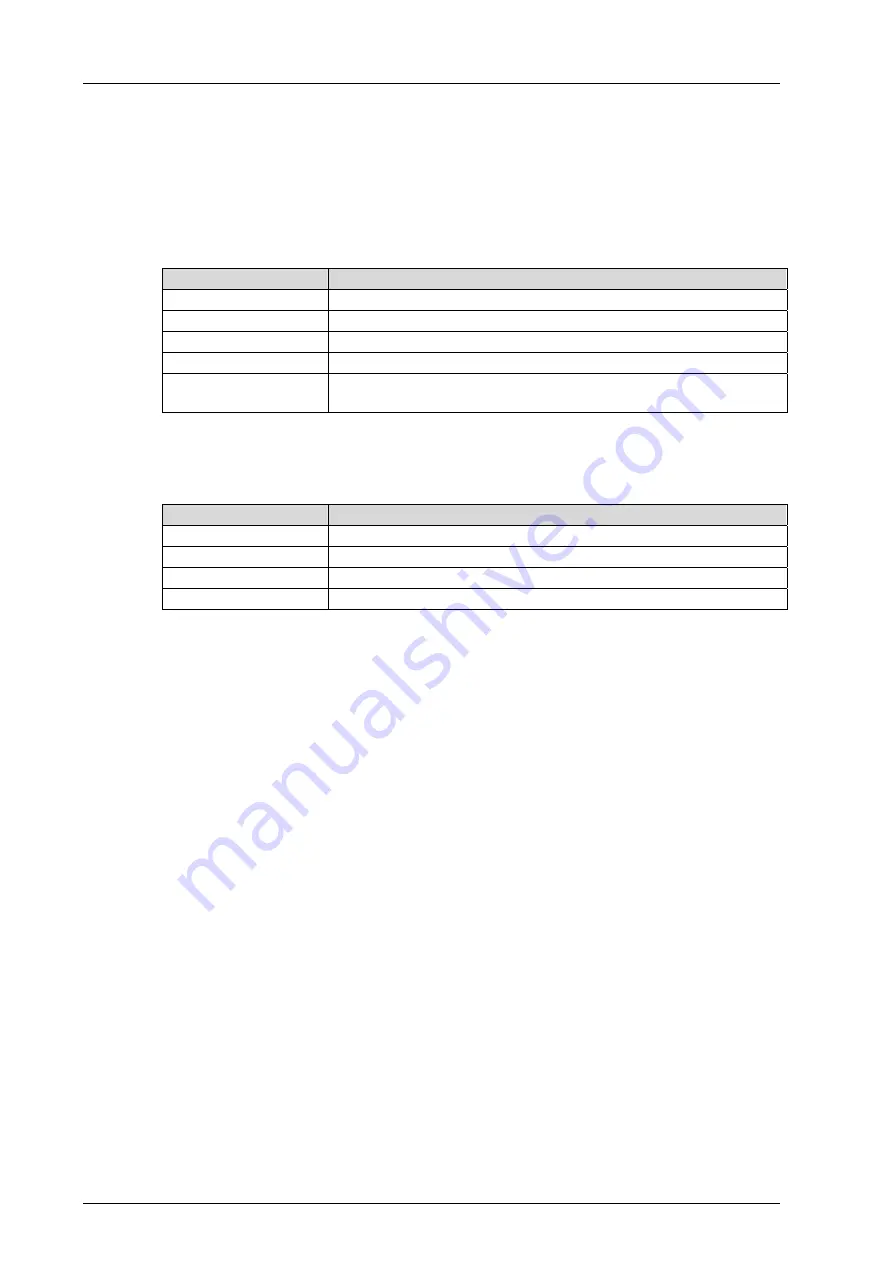
3 Product Description
X-AI 32 51
Page 18 of 58
HI 801 181 E Rev. 4.00
3.6 Connector
Boards
A connector board connects the module to the field zone. Module and connector board
form together a functional unit. Insert the connector board into the appropriate slot prior to
mounting the module on the base plate.
The following connector boards are available for the module:
Connector board
Description
X-CB 008 51
Connector board with screw terminals
X-CB 008 52
Redundant connector board with screw terminals
X-CB 008 53
Connector board with cable plug
X-CB 008 54
Redundant connector board with cable plug
X-CB 008 55
Redundant connector board with cable plug, redundant field
termination assembly
Table 10: Available Connector Boards
For high precision measurements, the following connector boards must be used:
Connector board
Description
X-CB 019 51
Connector board with screw terminals
X-CB 019 52
Redundant connector board with screw terminals
X-CB 019 53
Connector board with cable plug
X-CB 019 54
Redundant connector board with cable plug
Table 11: Connector Boards for High Precision Measurements
3.6.1
Mechanical Coding of Connector Boards
I/O modules and connector boards are mechanically coded starting from hardware revision
AS
0
0 to prevent them from being equipped with invalid I/O modules. Coding avoids
incorrect installation of invalid I/O modules thus preventing negative effects on redundant
modules and field zone. A part from that, invalid equipment has no effect on the HIMax
system since only I/O modules that are correctly configured in SILworX enter the RUN
state.
I/O modules and the corresponding connector boards have a mechanical coding in form of
wedges. The coding wedges in the female connector of the connector board match with the
male connector recesses of the I/O module plug, see Figure 5.
Coded I/O modules can only be plugged in to the corresponding connector boards.
Summary of Contents for X-AI 32 51
Page 1: ...X AI 32 51 HIMax Analog Input Module Manual ...
Page 57: ......