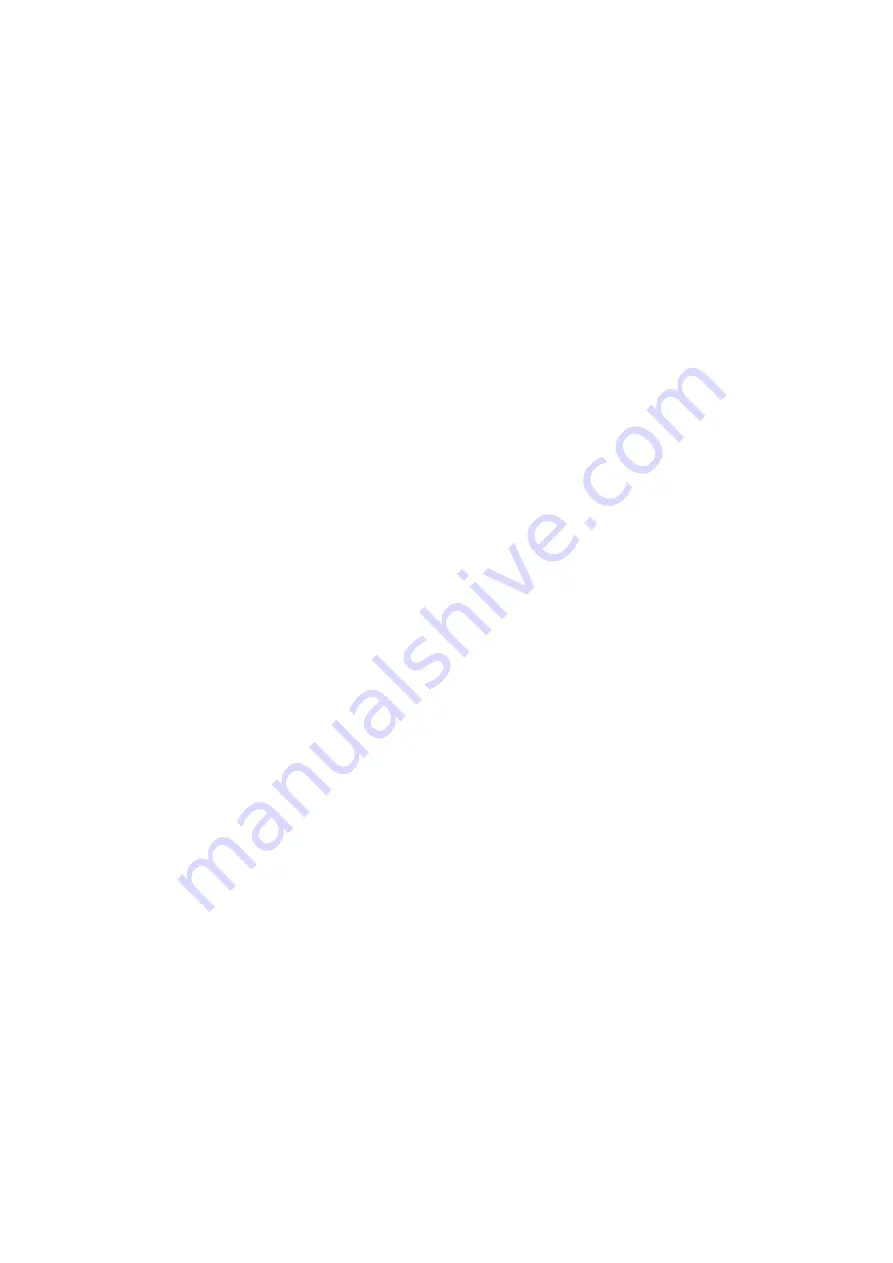
7
…BREAK IN CONTINUED
During break in, carburetor setting should be completed. Max allowable CHT - 535 F. Max
allowable EGT
–
1256 F at full power. Max EGT in mid range
–
1330 F. Engines should be
jetted to run at approximately 100 to 150 degrees EGT below maximum
Run-in engine easily for the first two hours. Avoid full power in the first hour of operation.
When engine is first started find the best idle RPM. This is the lowest RPM the engine will
run smoothly at and will vary depending on application. If supplied with a clutch very low
idle Rpms are possible (800 to 1200 Rpm). When supplied with the belt drive idle speed will
be higher 1600 to 2200 Rpm. Heavy props require higher idle speeds than lighter props. Now
is the time to adjust the air screw (s) on the carburetor (s) and to get the idle stop screw (s)
set.
After your idle adjustments are complete advance Rpm to 2500 for 20 minutes. After 20
minutes return to idle speed until engine cools and then advance Rpm to 3000 for 20 minutes.
After 20 minutes at 3000 Rpm return to idle speed until engine cools and then advance Rpm
to 3500 for 20 minutes. After 20 minutes at 3500 return to idle for a cool down and then
advance to 4000 Rpm for 20 minutes. At the end of the 4000 Rpm run you will have 1 hour
and 20 minutes break in time on the engine. During each of these 20-minute runs you should
record the EGT and CHT for each run. If temperatures are out of range stop break in and
rectify cause.
After 20 minutes at 4000 return to idle speed for a cool down. Advance to full throttle for 3 to
4 seconds and then smoothly return to idle. This is to determine if your prop is pitched
correctly. If engine exceeds peak Hp Rpm (6150 Rpm) stop break in and add pitch. Restart,
warm up at idle and then go to full throttle again to check if your pitch adjustments now hold
the engine to peak RPM. If engine is more than 200 Rpm below peak Rpm prop pitch will
have to be reduced to allow engine to come up to proper speed. If engine is more than 100
Rpm above peak Rpm prop pitch will have to be increased to bring engine Rpm down to
proper speed. If your prop is not pitched correctly the EGT’s and CHT’s you record for the
2
nd
half of the break in will not be accurate. Also serious engine damage can occur when
running without enough load to keep engine at peak Hp Rpm.
After your prop adjustments are complete restart and warm up engine at idle. Advance Rpm
to 4500 for 20 minutes. After 20 minutes return to idle speed until engine cools and then
advance Rpm to 5000 for 20 minutes. After 20 minutes at 5000 Rpm return to idle speed until
engine cools and then advance Rpm to 5500 for 20 minutes. After 20 minutes at 5500 return
to idle for a cool down and then advance to full power for 2 minutes. If CHT exceeds
maximum (535 deg. F.) before the end of the 2-minute run reduce power to idle for a short
cool down and then complete the remainder of the 2-minute full power run. EGT should be
below 1150 at full power. During each of these 20-minute runs you should record the EGT
and CHT for each run. If temperatures are out of range stop break in and rectify cause.
After break in is complete allow engine to cool completely and then check the torque of the
head bolts, cylinder base nuts, intake manifold bolts and exhaust bolts. It will take several
hours for engine to completely cool down. Do not re-torque when engine is warm. If not
possible to re-torque after break in it is imperative that top end re-torque is done within the
1
st
. 10Hrs.
Summary of Contents for F-23
Page 17: ...17 Note 1 inch 25 4 millimeters ...
Page 23: ...23 ...