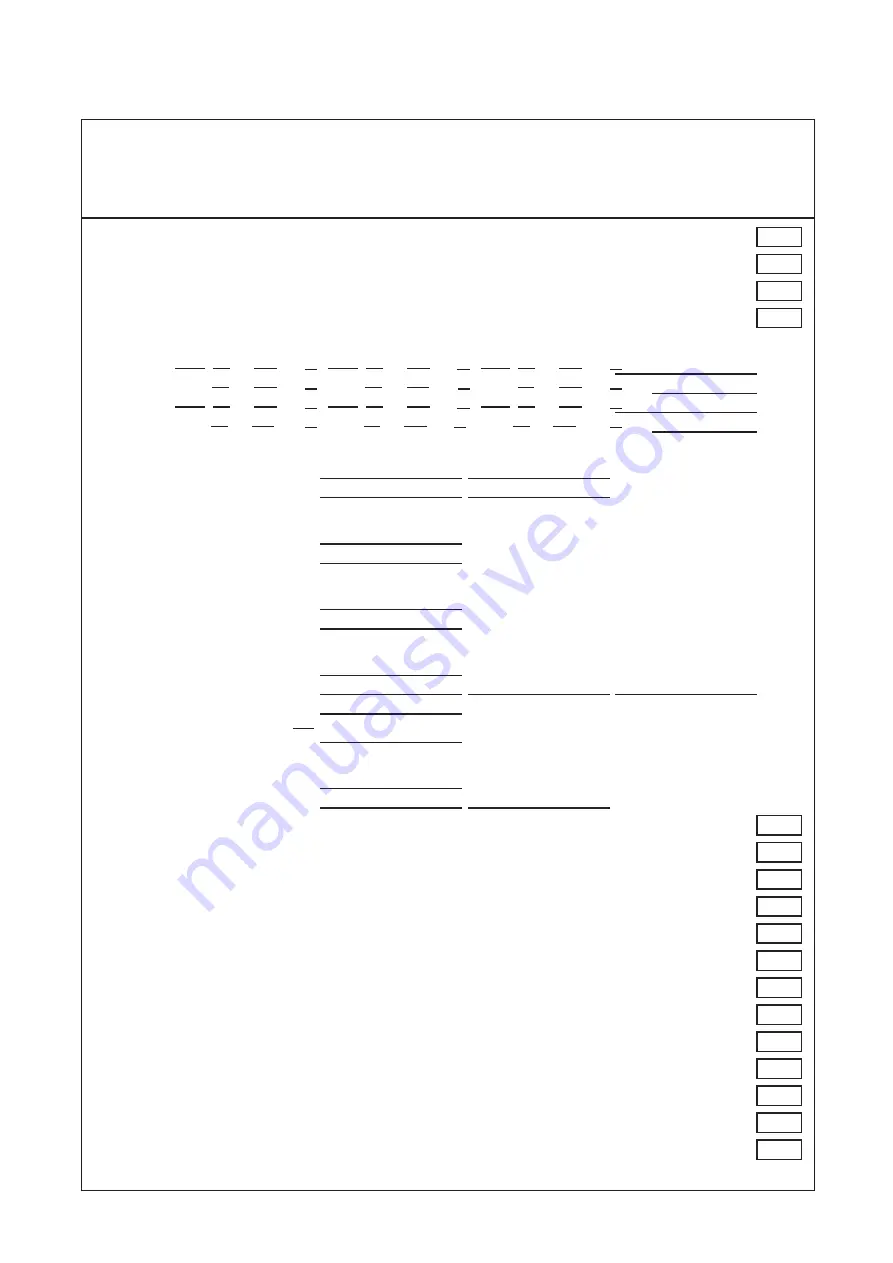
57
Table 10.1 Test Run and Maintenance Record
MODEL:
SERIAL. No.
COMPRESSOR MFG. No.
CUSTOMER'S NAME AND ADDRESS:
DATE:
1. Is the rotation direction of the indoor fan correct?
2. Is the water source unit inlet and outlet water pipe connection correct?
3. Are there any abnormal compressor sounds?
4. Has the unit been operated at least twenty (20) minutes?
5. Check Room Temperature
o
C
o
C
o
C
Inlet: No. 1 DB
/WB
o
C, No. 2 DB
/WB
o
C, No. 3 DB
/WB
o
C, No. 4 DB
/WB
Outlet:
DB
/WB
o
C,
DB
/WB
o
C,
DB
/WB
o
C,
DB
/WB
Inlet: No. 5 DB
/WB
o
C, No. 6 DB
/WB
o
C, No. 7 DB
/WB
o
C, No. 8 DB
/WB
Outlet:
DB
/WB
o
C,
DB
/WB
o
C,
DB
/WB
o
C,
DB
/WB
o
C
6. Check Water Source Unit Entering and Leaving Water Temperature and Pressure.
Entering Water:
o
C,
MPa
Leaving Water:
o
C,
MPa
7. Check Refrigerant Temperature
Liquid Temperature:
o
C
Discharge Gas Temperature:
o
C
8. Check Pressure
Discharge Pressure:
MPa
Suction Pressure:
MPa
9. Check Voltage
Rated Voltage:
V
Operating Voltage:
L
1
-L
2
V, L
1
-L
3
V, L
2
-L
3
V
Starting Voltage:
V
V
Vm
10. Check Compressor Input Running Current
Input:
kW
Running Current:
Comp. No.1
A Comp. No.2
A
11. Is the water flow adequate?
12. Is the refrigerant charge adequate?
13. Do the water flow switch operate correctly?
14. Do the operation control devices operate correctly?
15. Do the safety devices operate correctly?
16. Has the unit been checked for refrigerant leakage?
17. Is the unit clean inside and outside?
18. Are all cabinet panels securely closed?
19. Are all cabinet panels free from rattles?
20. Is the filter clean?
21. Is the heat exchanger clean?
22. Are the stop valves open?
23. Does the condensate water flow smoothly from the condensate pipe?
Phase Imbalance:
1-
=
THE RESULT OF ALL PERIODIC ROUTINE TESTS
:
24. Are the components of the system changed and replaced?
Summary of Contents for AVWW-114FKFW
Page 2: ......