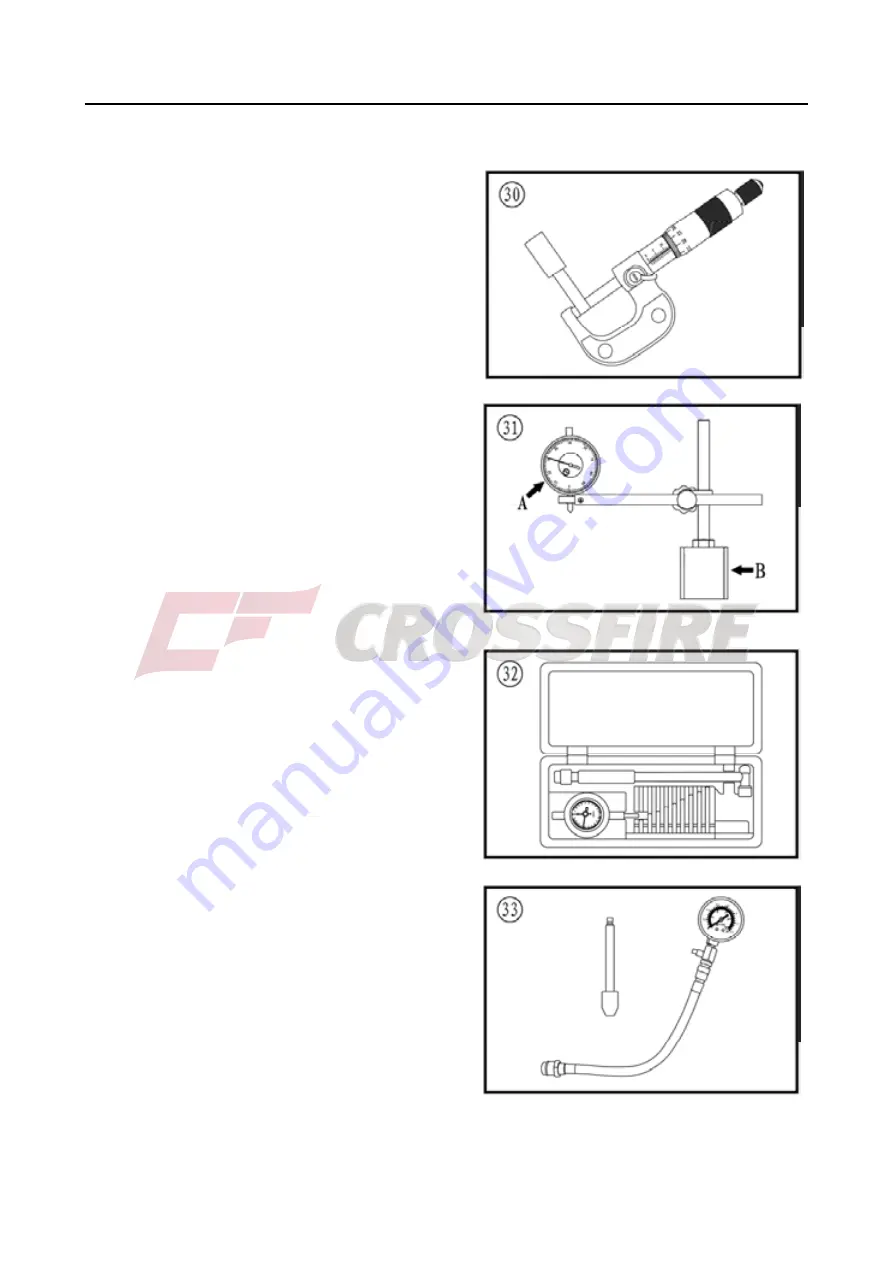
GENERAL INFORMATION
- 21 -
Telescoping and Small Bore Gauges
Use telescoping gauges (Figure 28) and small
bore gauges (Figure 29) to measure bores. Neither
gauge has a scale for direct readings. Use an outside
micrometer to determine the reading.
To use a telescoping gauge, select the correct
size gauge for the bore. Compress the movable post
and. Care fully insert the gauge into the bore. Carefully
move the gauge in the bore to make sure it is centered.
Tighten the knurled end of the gauge to hold the
movable post in position. Remove the gauge and
measure the length of the posts. Telescoping gauges
are typically used to measure cylinder bores.
To use a small bore gauge, select the correct size
gauge for the bore. Carefully insert the gauge into the
bore. Tighten the knurled end of the gauge to carefully
expand the gauge fingers to the limit within the bore.
Do not over tighten the gauge because there is no
built-in release. Excessive tightening can damage the
bore surface and damage the tool. Remove the gauge
and measure the outside dimension (Figure 30).
Small bore gauges are typically used to measure valve guides.
Dial Indicator:
A dial indicator (Figure 31) is a gauge with a dial
face and needle used to measure variations in
dimensions and movements. Measuring brake rotor
runout is a typical use for a dial indicator.
Dial indicators are available in various ranges and
graduations and with three basic types of mounting
bases: magnetic (B. Figure 31). Clamp, or screw-in
stud. When purchasing a dial indicator, select on with
a continuous dial (A, Figure 31).
Cylinder Bore Gauge
A cylinder bore gauge is similar to a dial indicator.
The gauge set shown in Figure 32 consists of a dial
indicator, handle, and different length adapters (anvils)
to fit the gauge to various bore sizes. The bore gauge
is used to measure bore size, taper and out-of-round.
When using a bore gauge, follow the manufacturer’s
instructions.