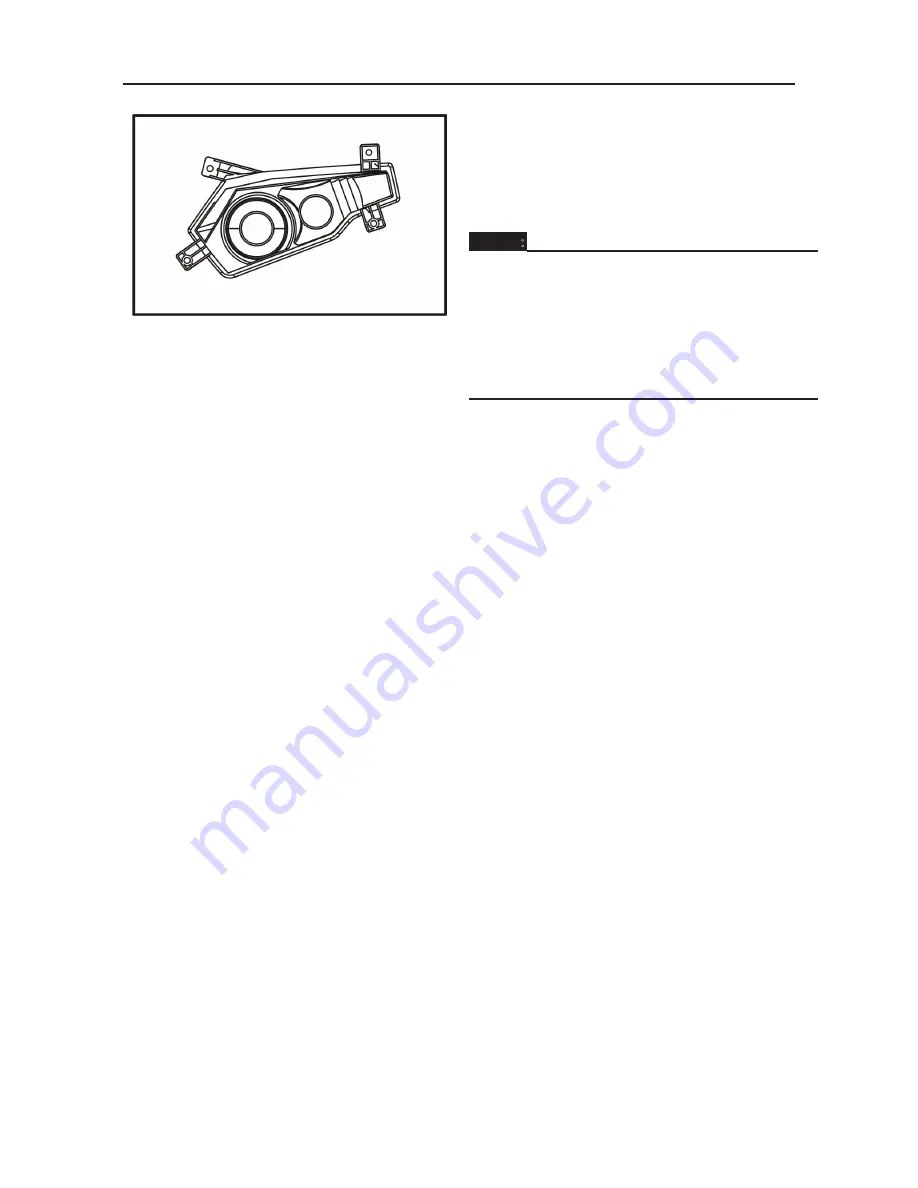
-123-
MAINTENCE AND ADJUSTMENT OF THE UTV
- 123 -
2. Install:
• bulb new
Secure the new bulb with the tail/brake light bulb
holder.
NOTE
:
Avoid touching the glass part of the bulb. Keep
it free from oil; otherwise, the transparency of
the glass, life of the bulb, and luminous flux will
be adversely affected. If oil gets on the bulb,
thoroughly clean it with a cloth moistened with
alcohol or lacquer thinner.
• tail/brake light bulb holder (with bulb)
Summary of Contents for HS200UTV
Page 3: ......
Page 15: ......
Page 94: ... 79 SPECIFICATIONS 79 HYDROGRAPHIC CHART Hydrographic chart Pressure ...
Page 95: ... 80 SPECIFICATIONS 80 LUBRICATION OIL WAY LUBRICATION OIL WAY Pressure splashing oil ...
Page 248: ... 233 CHASSIS 233 Fuel tank cap Remove the fuel tank cap by turning it counterclockwise ...
Page 263: ... 248 ...
Page 304: ... 289 ...
Page 305: ... 290 ...
Page 306: ... 291 ...
Page 307: ... 292 ...
Page 308: ... 293 ...
Page 309: ... 294 ...
Page 310: ... 295 ...
Page 311: ... 296 ...