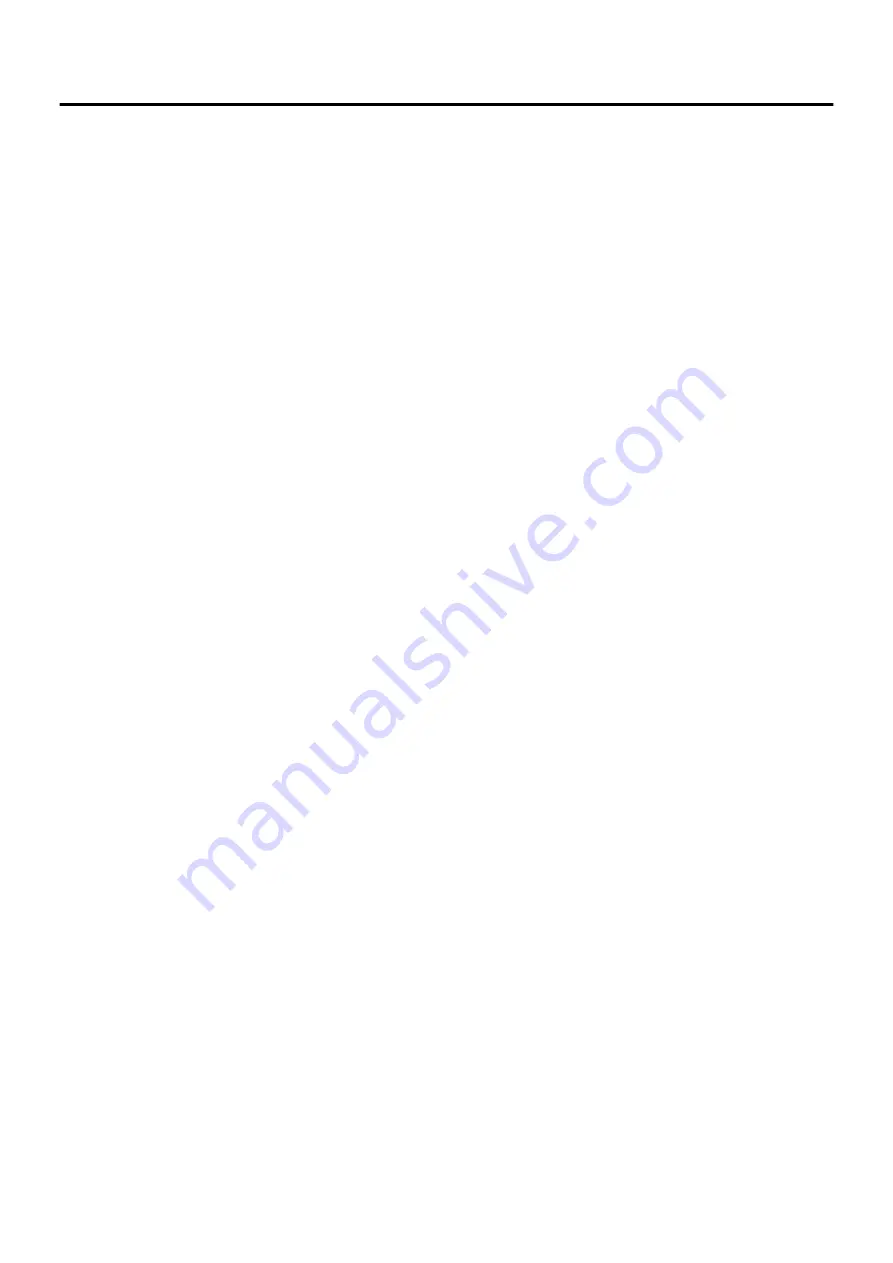
Introduction
Introduction
(All)
Table of Contents
Introduction........................................................................0-2
safety information..........................................................0-2
Introduction (All) 0-1
Find manuals at https://best-manuals.com
Find manuals at https://best-manuals.com