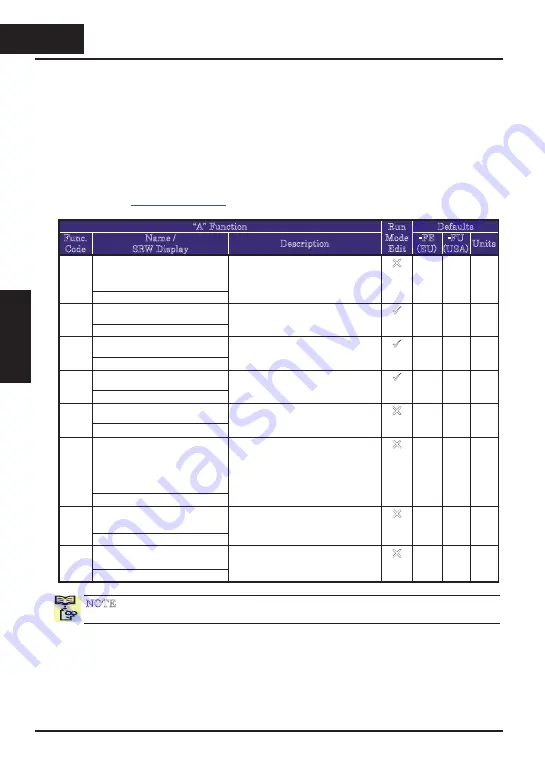
PID Control
When enabled, the built-in PID loop calculates an ideal inverter output value to cause a
loop feedback process variable (PV) to move closer in value to the set point (SP). The
frequency command serves as the SP. The PID loop algorithm will read the analog input
for the process variable (you specify the current or voltage input) and calculate the
output.
x
A scaled factor in A075 lets you multiply the PV factor, converting it into
engineering units for the process.
x
Proportional, integral, and derivative gains are all adjustable.
x
See “
PID Loop Operation” on page 4-56
for more information.
“A” Function
Defaults
Func.
Code
Name /
SRW Display
Description
Run
Mode
Edit
-FE
(EU)
-FU
(USA)
Units
PID enable
A071
PID Mode
OFF
Enables PID function,
two option codes:
00
}
PID Disable
01
}
PID Enable
U
00
00
PID proportional gain
A072
PID P
0001.0
Proportional gain has a range of
0.2 to 5.0
9
1.0
1.0
PID integral time constant
A073
PID I
0001.0s
Integral time constant has a
range of 0.0 to 150 seconds
9
1.0
1.0
sec
PID derivative time constant
A074
PID D
000.00s
Derivative time constant has a
range of 0.0 to 100 seconds
9
0.00
0.00
sec
PV scale conversion
A075
PID Cnv
001.00%
Process Variable (PV), scale
factor (multiplier), range of 0.01
to 99.99
U
1.00
1.00
PV source setting
A076
PID INP
OI
Selects source of Process Variable
(PV), option codes:
00
}
[OI] terminal (current in)
01
}
[O] terminal (voltage in)
02
}
ModBus network
10
}
Calculate function output
U
00
00
Reverse PID action
A077
PID MINUS
OFF
Two option codes:
00
}
PID input = SP-PV
01
}
PID input = -(SP-PV)
U
00
00
PID output limit
A078
PID Vari
0000.0%
Sets the limit of PID output as
percent of full scale,
range is 0.0 to 100.0%
U
0.0
0.0
%
NOTE: The setting A073 for the integrator is the integrator’s time constant Ti, not the
gain. The integrator gain Ki = 1/Ti. When you set A073 = 0, the integrator is disabled.
3
22
Config
uri
ng Driv
e
Parameters
3
−
22
&RQ¿JXULQJ'ULYH
Parameters