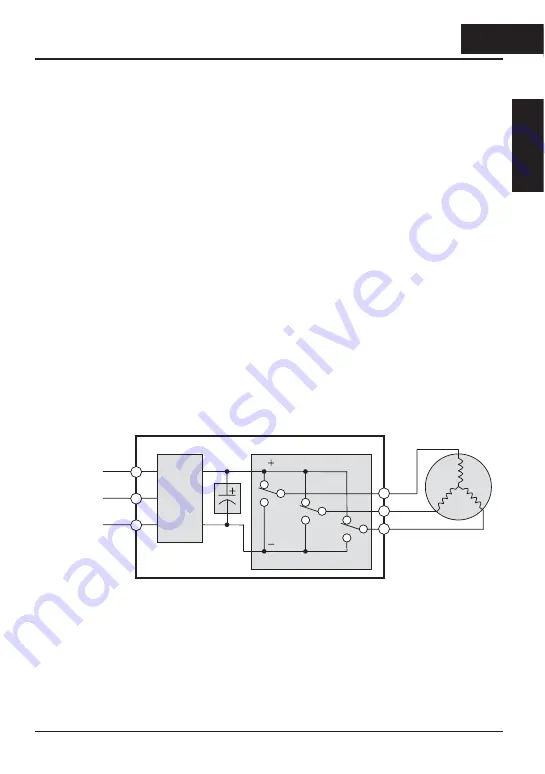
Introduction to Variable-Frequency Drives
The Purpose of Motor Speed Control for Industry
Hitachi inverters provide speed control for 3-phase AC induction motors. You connect
AC power to the inverter, and connect the inverter to the motor. Many applications
benefit from a motor with variable speed, in several ways:
x
Energy savings – HVAC
x
Need to coordinate speed with an adjacent process – textile and printing presses
x
Need to control acceleration and deceleration (torque)
x
Sensitive loads – elevators, food processing, pharmaceuticals
What is an Inverter
The term
inverter and variable-frequency drive are related and somewhat
interchangeable. An electronic motor drive for an AC motor can control the motor’s
speed by
varying the frequency of the power sent to the motor.
An inverter, in general, is a device that converts DC power to AC power. The figure
below shows how the variable-frequency drive employs an internal inverter. The drive
first converts incoming AC power to DC through a rectifier bridge, creating an internal
DC bus voltage. Then the inverter circuit converts the DC back to AC again to power the
motor. The special inverter can vary its output frequency and voltage according to the
desired motor speed.
The simplified drawing of the inverter shows three double-throw switches. In Hitachi
inverters, the switches are actually IGBTs (insulated gate bipolar transistors). Using a
commutation algorithm, the microprocessor in the drive switches the IGBTs on and off
at a very high speed to create the desired output waveforms. The inductance of the
motor windings helps smooth out the pulses.
Rectifier
Motor
Inverter
Converter
Internal
DC Bus
Power
Input
L1
L2
L3
U/T1
V/T2
W/T3
Variable-frequency Drive
1
19
Getting st
arted
1
−
19
Getting started