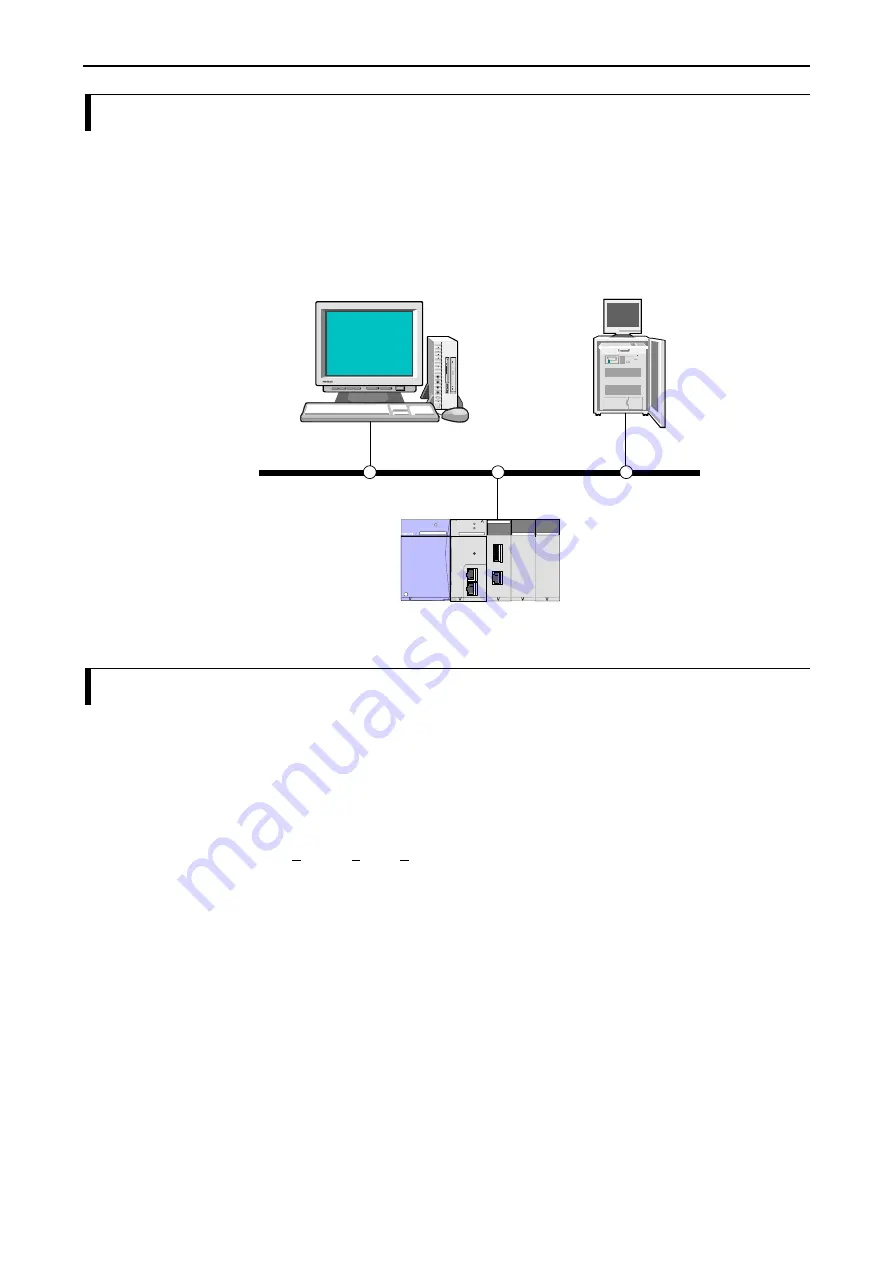
Chapter 1 Introduction
1.2 Outline
This product supports production control and system operation monitor, equipment monitor and maintenance by
connecting PLC to information network.
1.
EH-ETH2 (this module) can be mounted onto the basic base of EH-150 system and is the communication module
can be connected EH-150 system to Ethernet comforms to IEEE802.3.
2.
This module connected to Ethernet will operate as one of the station of the network system. For this operation this
module can exchange the data with personal computer or engineering workstation connected with network.
POWER
EH-150
Tx
Rx
H.ERR
C.ERR
POW
0
4
8
12
1
5
9
13
2
6
10
14
3
7
11
15
0
4
8
12
1
5
9
13
2
6
10
14
3
7
11
15
Server machine
EH-150 System
Personal computer(PC)
Ethernet
1.3 Feature
1. The data sending or receiving connection can be used 10 at once.
- 6 connections for automatic send/receive and 4 connections for H/EH-series protocol (Taskcode communication)
can be used.
- Sending data and receiving data can be done with one connection.
- It is selectable TCP/IP or UDP/IP as the communication protocol for each connection.
- The maximum sending or receiving data size on each ASR connection is 1,454 bytes.
ASR is omission of Automatic Sending/Receiving.
When you use cyclic transmission function and automatic transmission function of ASR, you can send/receive a
data without making a ladder(user) program.
Task code communication is original communication protocol for H/EH-series. You can make monitoring system
or data logging system by connecting SCADA system which supports its protocol.
2. Saving the developing power with using
ASR function
.
- The all configuration for communication can be done with using the dedicated software “EH-ETH2
Configurator” before to start communication. The configured data for communication can be saved with text
format file.
- By using ASR function, it is possible to save the development power for programming the user program to
communication.
3. Using programming software via Ethernet communication line.
- It is possible to monitor the I/O data or to handle the program of PLC with LADDER EDITOR for Windows® or
Control Editor via Ethernet communication line. You can save the time and cost for maintenance of the user
program or total system.
1-2