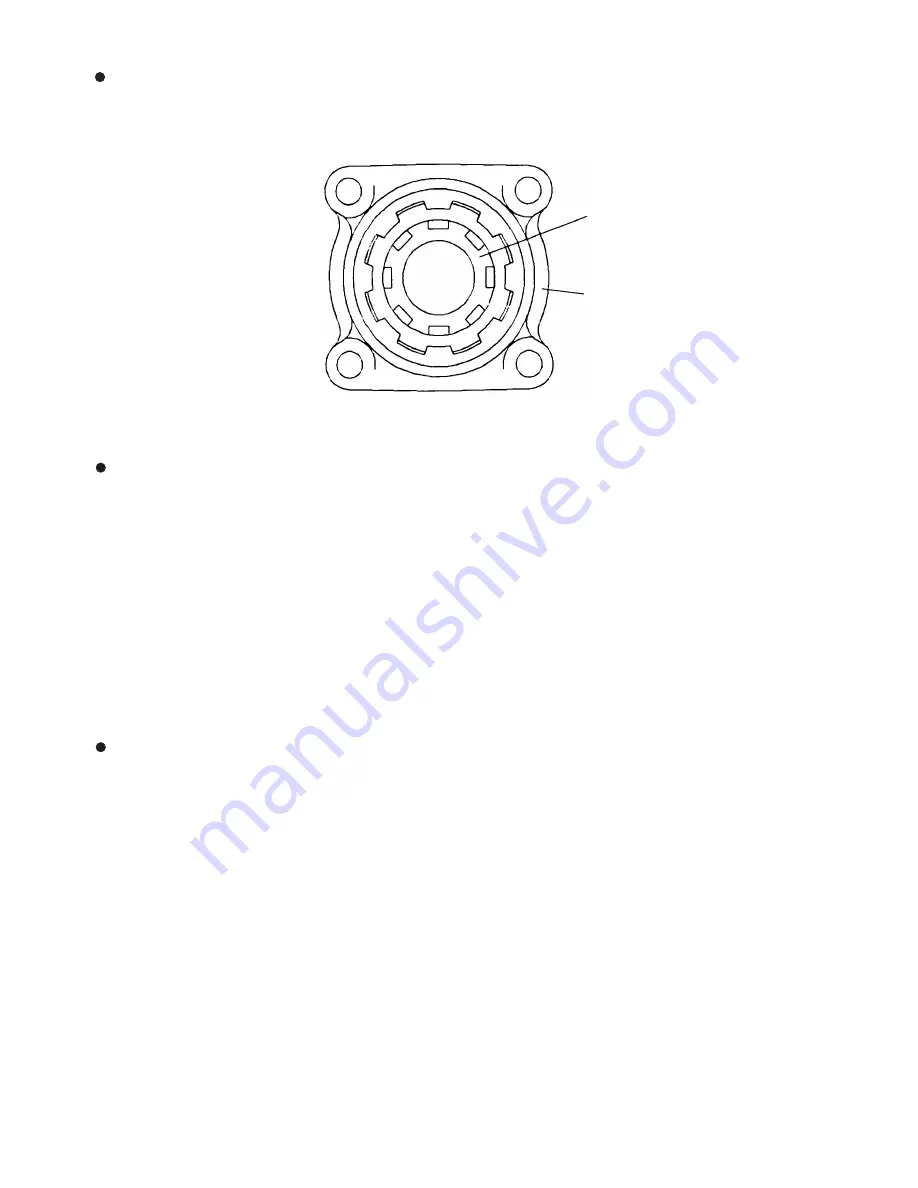
--- 18 ---
Oil seals
Be very careful not to damage the O-ring (S-46)
[11]
on the Cylinder Case
[9]
, O-ring (S-36)
[12]
in the
Cylinder Case
[9]
, O-ring (S-48)
[45]
on the Crank Case Cover
[42]
, O-ring (A)
[16]
in the Cylinder Holder
[15]
, O-ring (S-32)
[49]
in the Crank Case
[46]
, O-rings
[27]
,
[34]
,
[35]
on the Second Hammer
[26]
, on the
Striker
[33]
and on the Piston
[37]
and Oil Seal (B)
[48]
in the Crank Case
[46]
.
Lubrication
Apply Hitachi Motor Grease No. 29 to the following places:
Apply 10 g (0.35 oz) on the gears in the Gear Cover
[54]
and the Crank Case
[46]
, and coat grease on the
Needle Bearing (M661)
[53]
(motor ass'y), Steel Ball D7.0
[23]
, pinion of armature ass'y.
Apply special grease (grease for electric impact drill) to the following places:
Apply 22 g (0.88 oz) on the Connecting Rod
[38]
in the crank case, coat grease on the inside diameter portion
of the Piston
[37]
, O-ring
[35]
, sliding portion of the Second Hammer
[26]
, Damper
[29]
, O-ring (C)
[27]
, inside
diameter portion of Oil Seal (B)
[48]
(lip portion), inside diameter portion of Slide Sleeve (A)
[21]
, inside
diameter portion of Slide Sleeve (B)
[20]
and the inside diameter portion of the Needle Holder
[17]
.
Lock sleeve reassembly
Be careful of the slot position of the Cylinder
[24]
and the Cylinder Case
[9]
when inserting the Lock Sleeve
[6]
between the Cylinder
[24]
and the Cylinder Case
[9]
(Fig. 29).
Cylinder
Cylinder case
Fig. 29
Summary of Contents for H 25PV
Page 28: ......