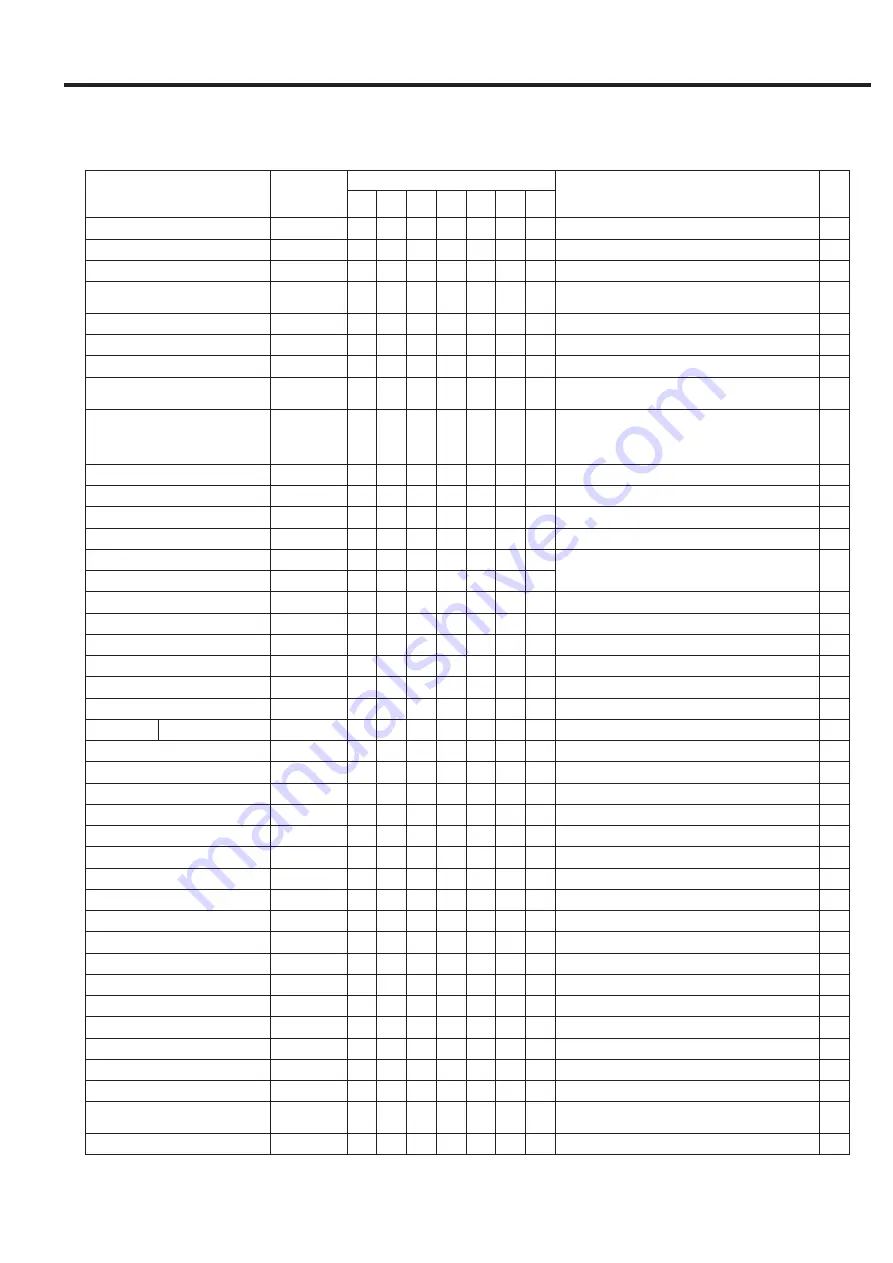
8.2 Typical Maintenance Standard (A) of Air Compressor
…
In case of annual run hour less than 6,000 hours
Maintenance part and item
Check
Inspection time
Note
Reference
page No.
Daily 1-Month 6-Month 1-Year 2-Year 4-Year 8-Year
Oil level gauge
Oil level check
○
Oil level must be within red lines during operation.
20
Discharge air temp.
Discharge air temp. check
○
Must be between 65
℃
and 100
℃
.
18
Relief valve
Performance check
○
Check by hand.
45
Lubricant (genuine synthetic oil)
Replenish/
Analysis
(○)
Replenish every 1,000 to 1,500 hours
Sampling analysis every 3,000 hours
20,21
Motor
Greasing
○
Use “RMS Grease”
52
Motor's cooling fin
Cleaning
○
52
Grease Reservoir
Cleaning
○
Clean once for every 2 grease replenishments.
52
Mechanical seal
Oil leak check
○
If the oil leak is 3 cc/h or higher, replace the seal even
before 8-year (48,000 hours) operation.
Air intake filter element
Replacement
○
Clean if the error code of an element clogging
appears on the digital monitor. Replace whenev-
er the number of times of cleaning has reached
5 times even within one year interval.
47
Oil filter element
Replacement
●
46
Oil separator element
Replacement
●
Replace the housing and square ring as well.
50
Solenoid valve
Performance check
●
Cooling fans
Crack check/Cleaning
●
DCBL controller cooling fan
Crack check/Cleaning
●
Clean cooling fins and duct.
53
Fan inverter
Crack check/Cleaning
●
Motor
Insulation check
●
1M ohm or more at DC500 V Mega.
Electric panel, instruments, sensors
Inspection/Cleaning
●
Terminal refastening, electric line cover check and cleaning.
Pipe joints
Loose check
●
Oil cooler, Aftercooler
Cleaning
●
Lubricant (genuine synthetic oil)
Replacement
○
21
Oil level gauge
Replacement
●
Consumable Parts Suction throttle valve
※
Replacement
●
Replace the cap seal, valve plate, and O-ring.Clean.
Piston of minimum pressure valve / check valve
※
Replacement
●
Replace check valve spring, O-ring at the same time.
49
Oil filling port O-ring, plug O-ring
Replacement
●
Suction pipe
Replacement
●
Oil temperature control valve
Inspection/Cleaning
●
Change O-ring.
DCBL controller cooling fan
Replacement
●
Including cooling fan in the starter/control box.
Fan motor bearing
Replacement
●
If not so, clean it and continue to use it.
Thermistor
Inspection
●
Oil temperature control valve
Replacement
●
Check valve (1/4 inch)
Replacement
●
Locate it on the oil-scavenging pipe from the shaft seal.
Coupling elastic body
Replacement
●
If not so, clean it and continue to use it.
O-ring (Air end)
Replacement
●
O-ring (Flange)
Replacement
●
O-ring, oil separator tank O-ring
Replacement
●
Replace 1/2 stop valve O-ring at the same time.
DCBL motor bearing
Replacement
●
Mechanical seal
Replacement
●
Compressor Air end bearing
Replacement
●
Controller smoothing capacitor
Replacement
●
CPU printed circuit board,
power PCB
Check/Clean/Replace
●
If it is dirty or shows a change in color, replace it.
If not so, clean it and continue to use it.
Fan inverter
Replacement
●
※
Replace these parts every 2 calendar years or when the
HISCREW
has loaded/unloaded total 1,000,000 times,
whichever comes earlier. For the total load/unload times, watch the digital monitor.
43
8. PERIODIC MAINTENANCE [Maintenance Standards (A)]