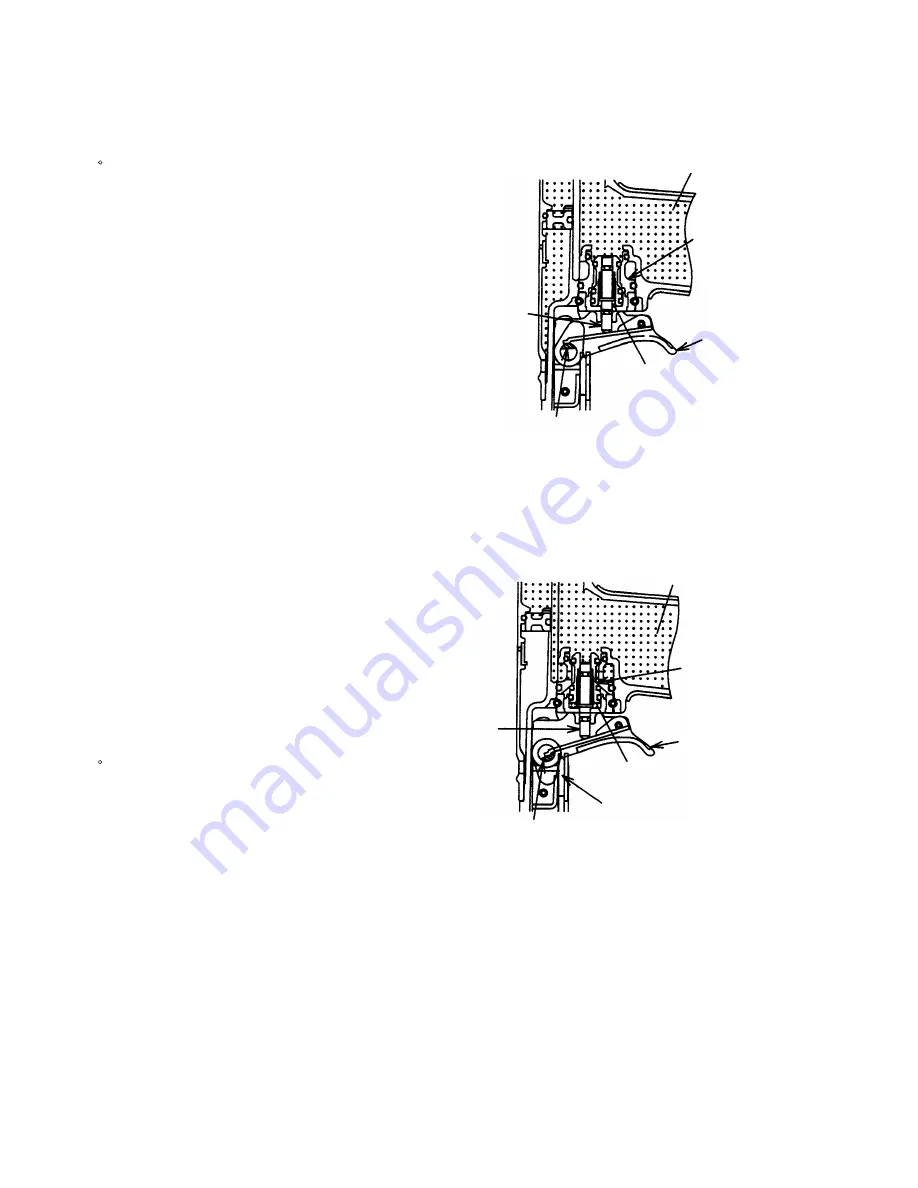
--- 12 ---
(4) Single actuation mechanism/contact actuation mechanism: (Fig. 8 and Fig. 9)
Single/contact actuation mechanism changeover is accomplished by turning the switching device
(Change Knob (C)
[58]
).
Single actuation mechanism (Switching device:
upward position):
1) Immediately after driving the first nail, the
control valve should be as shown in Fig. 7.
2) When only Pushing Lever (B)
[40]
is released
and Trigger (C) Ass'y
[36]
is held as shown in
Fig. 8, the plate of Trigger (C) Ass'y
[36]
contacts Change Knob (C)
[58]
and the Plunger
[67]
returns (lowers) only halfway.
Because of this, compressed air does not flow
into the valve piston lower chamber, and Valve
Piston
[63]
remains in the lowered position.
Accordingly, the Piston
[12]
remains in the
lowered position as shown in Fig. 6.
3) When Trigger (C) Ass'y
[36]
is released, the
Plunger
[67]
returns (lowers) completely as
shown in Fig. 5. Compressed air then flows into
the valve piston lower chamber, and the Valve
Piston
[63]
is forced upward. The Piston
[12]
then returns fully upward. Therefore, unless
Trigger (C) Ass'y
[36]
is released after each
nailing operation, the structural mechanism
prevents the next nailing operation.
Contact actuation mechanism (Switching device:
downward position):
1) Immediately after the first nail is driven, the
control valve should be as shown in Fig. 7.
2) Even when only Pushing Lever (B)
[40]
is
released and Trigger (C) Ass'y
[36]
is held, the
Plunger
[67]
returns (lowers) completely as
shown in Fig. 9. Thus the Piston
[12]
returns
(raises) fully. Accordingly, continuous nailing
can be accomplished by pushing only Pushing
Lever (B)
[40]
up and down while holding
Trigger (C) Ass'y
[36]
depressed.
Plunger
[67]
Valve piston
lower chamber
Trigger (C)
Ass'y
[36]
Valve Piston
[63]
Accumulator
Switching device (Change Knob (C)
[58]
)
(Upward position)
Fig. 8 Single actuation mechanism
Plunger
[67]
Pushing Lever (B)
[40]
Valve portion
lower chamber
Trigger (C) Ass'y
[36]
Valve Piston
[63]
Accumulator
Switching device (Change Knob (C)
[58]
)
(Downward position)
Fig. 9 Contact actuation mechanism
Summary of Contents for NT 65M2
Page 37: ......