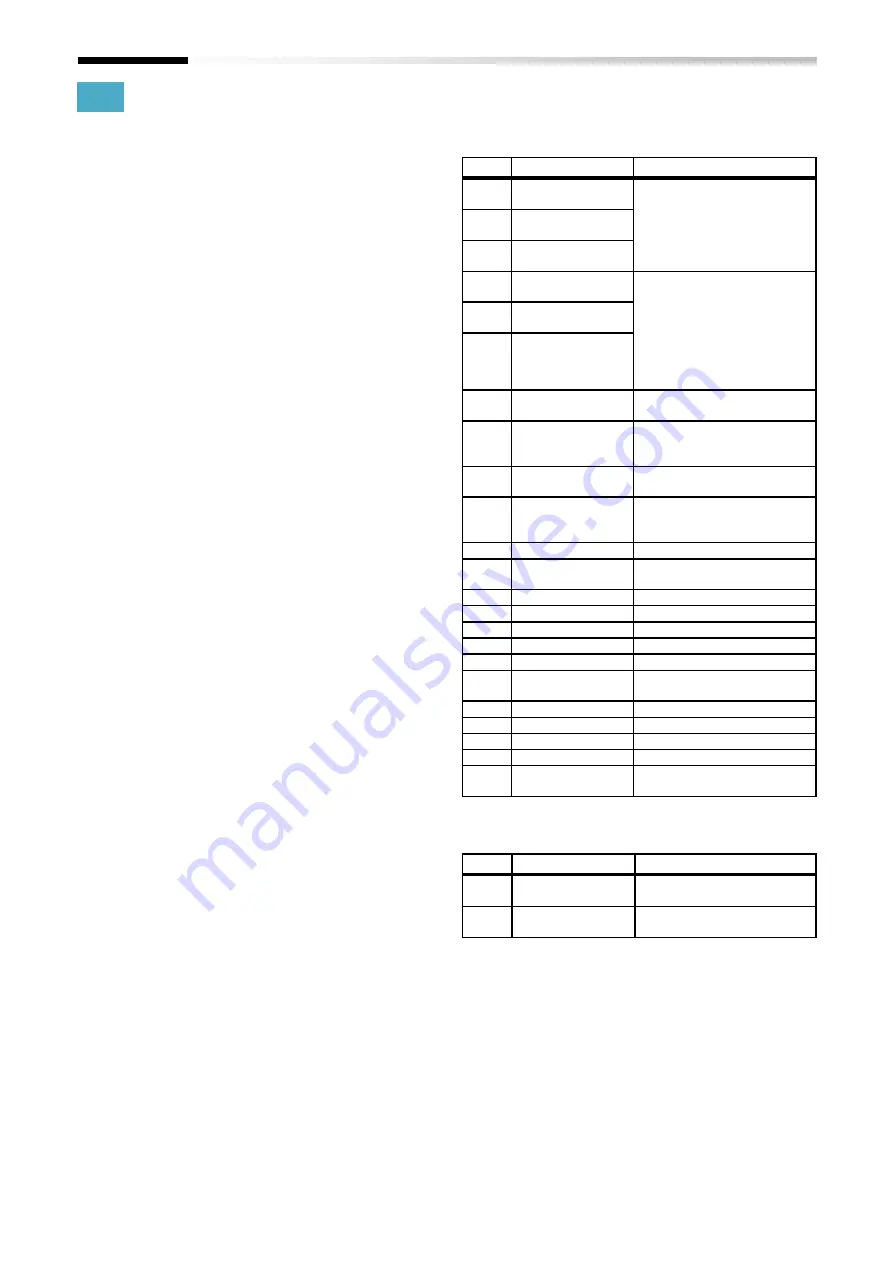
4-18
Chapter 4
Safety Function
4.5.2
SS1 function
■
How SS1 function works
The SS1 function can decelerates the motor speed to stop
by monitoring the time or speed until the motor speed to
stop. Eventually, SS1 function transits to STO function.
The SS1 function can be used by inputting SS1-A or SS1-B
function individually.
When SS1-A and SS1-B are activated at the same time,
SS1-A is higher priority function.
The setting [1-12]STO-A release mode / [2-12]STO-B
release mode is applied after transition to STO function.
Releasing of SS1 function depends on the activation of SS1
signal input.
Deceleration time in the SS1 state is determined by
Deceleration time [oC-10] or [oC-20] in the setting
parameters of SJ-P1.
■
Related parameters
No.
Name
Related data
0-11
Safety Function
Select Input 1
02:SS1-A / 12:SS1-B
0-12
Safety Function
Select Input 2
0-13
Safety Function
Select Input 3
0-21
Safety Function
Select Output 1
01:STO-A monitoring /
02:STO-A completed /
03:SS1-A monitoring /
04:SS1-A completed /
11:STO-B monitoring /
12:STO-B completed /
13:SS1-B monitoring /
14:SS1-B completed
0-22
Safety Function
Select Output 2
0-23
Safety Function
Select Output 3
1-11
Keep time after STO-
A
0.00 to 3600.00s
1-12
STO-A Release mode
00:Without release /
01:With safety signal /
02:With release signal
2-11
Keep time after STO-
B
0.00 to 3600.00s
2-12
STO-B release mode
00:Without release /
01:With safety signal/
02:With release signal
1-21
SS1-A Zero frequency
0.10 to 10.00Hz
1-22
SS1-A monitoring
method
00:Time /01:Frequency
1-23
SS1-A Active time
0.00 to 3600.00s
1-24
SS1-A Min ramp time
0.00 to 3600.00s
1-25
SS1-A Max ramp time
0.00 to 3960.00s
1-26
SS1-A Wait time
0.00 to 600.00s
2-21
SS1-B Zero frequency
0.10 to 10.00Hz
2-22
SS1-B monitoring
method
00:Time /01:Frequency
2-23
SS1-B Active time
0.00 to 3600.00s
2-24
SS1-B Min ramp time
0.00 to 3600.00s
2-25
SS1-B Max ramp time
0.00 to 3960.00s
2-26
SS1-B Wait time
0.00 to 600.00s
0-07
SFS Select
11:STO-A / 12:STO-B / 21:SS1-A /
22:SS1-B / 31:SBC-A / 32:SBC-B
■
Related P1 parameters
No.
Name
Related data
oC-10
SS1-A Deceleration
time
0.00 to 3600.00(s)
oC-20
SS1-B Deceleration
time
0.00 to 3600.00(s)
Summary of Contents for P1
Page 2: ...The picture is an example of installing P1 FS to SJ P1 ...
Page 8: ...C 3 Index Memo ...
Page 10: ...1 2 Chapter 1 Safety Precaution Risk Memo ...
Page 12: ...2 2 Chapter 2 Introduction to the Safety Function Guide Memo ...
Page 62: ...7 2 Chapter 7 Commissioning Memo ...
Page 64: ...8 2 Chapter 8 Verification and Validation Memo ...
Page 68: ...10 2 Chapter 10 Maintenance Memo ...
Page 72: ...11 4 Chapter 11 Specification and Technical data Memo ...