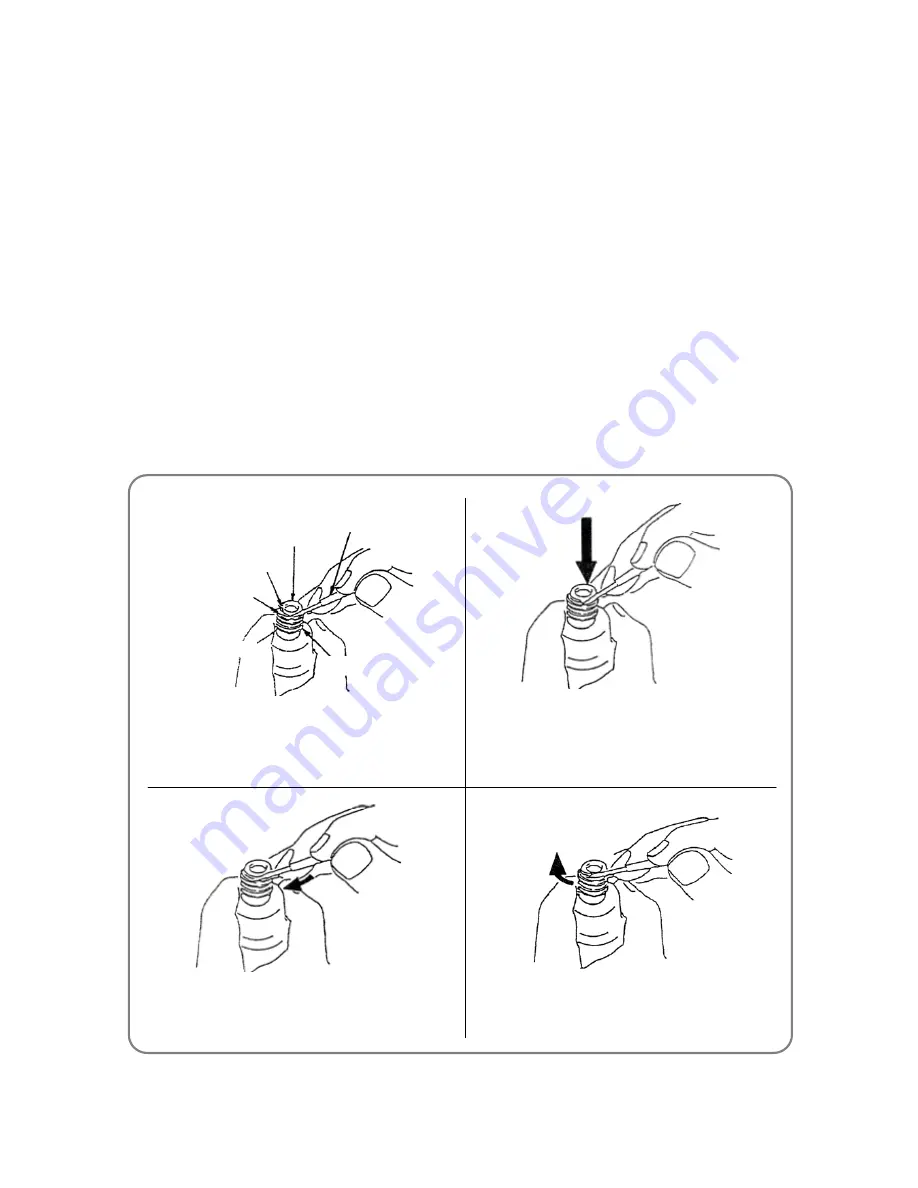
-21-
Hold the body and adjust the gap of the Retaining Ring
[1]
to the groove of Anvil (D)
[9]
, then insert a small
flat-blade screwdriver into the groove at an angle.
Slide the small flat-blade screwdriver under one side of
the gap of the Retaining Ring
[1]
.
Small flat-blade
screwdriver
Anvil (D)
[9]
Retaining Ring
[1]
Washer (D)
[2]
Gap of the Retaining
Ring
[1]
Guide Sleeve (D)
[4]
10. REPAIR GUIDE
WARNING: Without fail, remove the battery from the main body before starting repair or
maintenance work. Because the tool is cordless, if the battery is left in and the
switch is activated inadvertently, the motor will start rotating unexpectedly,
which could cause serious injury.
10-1. Precautions in Disassembly and Reassembly
The
[Bold]
numbers in the description below correspond to the item numbers in the Parts List
and the exploded assembly diagram of the Model WH 14DBL.
10-1-1. Disassembly
(1) Removal of guide sleeve (D)
By following the procedure shown in Figs. 5-1 to 5-4, remove the Retaining Ring
[1]
, Washer
(D)
[2]
, Guide Spring (D)
[3]
and Guide Sleeve (D)
[4]
in this order. Avoid quickly raising the
Retainer Ring
[1]
or it may fly out forcefully. Be sure not to lose the two Steel Balls D3.5
[8]
in
Anvil (D)
[9]
.
(2) Insert a small flat-blade screwdriver between Front Cap (F)
[5]
and the Front Cover (Black)
[6]
and remove Front Cap (F)
[5]
from the Hammer Case
[7]
.
Fig. 5-2
Fig. 5-4
Slowly raise the Retaining Ring
[1]
using the end
face of Guide Sleeve (D)
[4]
as a fulcrum.
Press down Washer (D)
[2]
with the small flat-blade
screwdriver.
Fig. 5-1
Fig. 5-3
• Removal of guide sleeve (D)