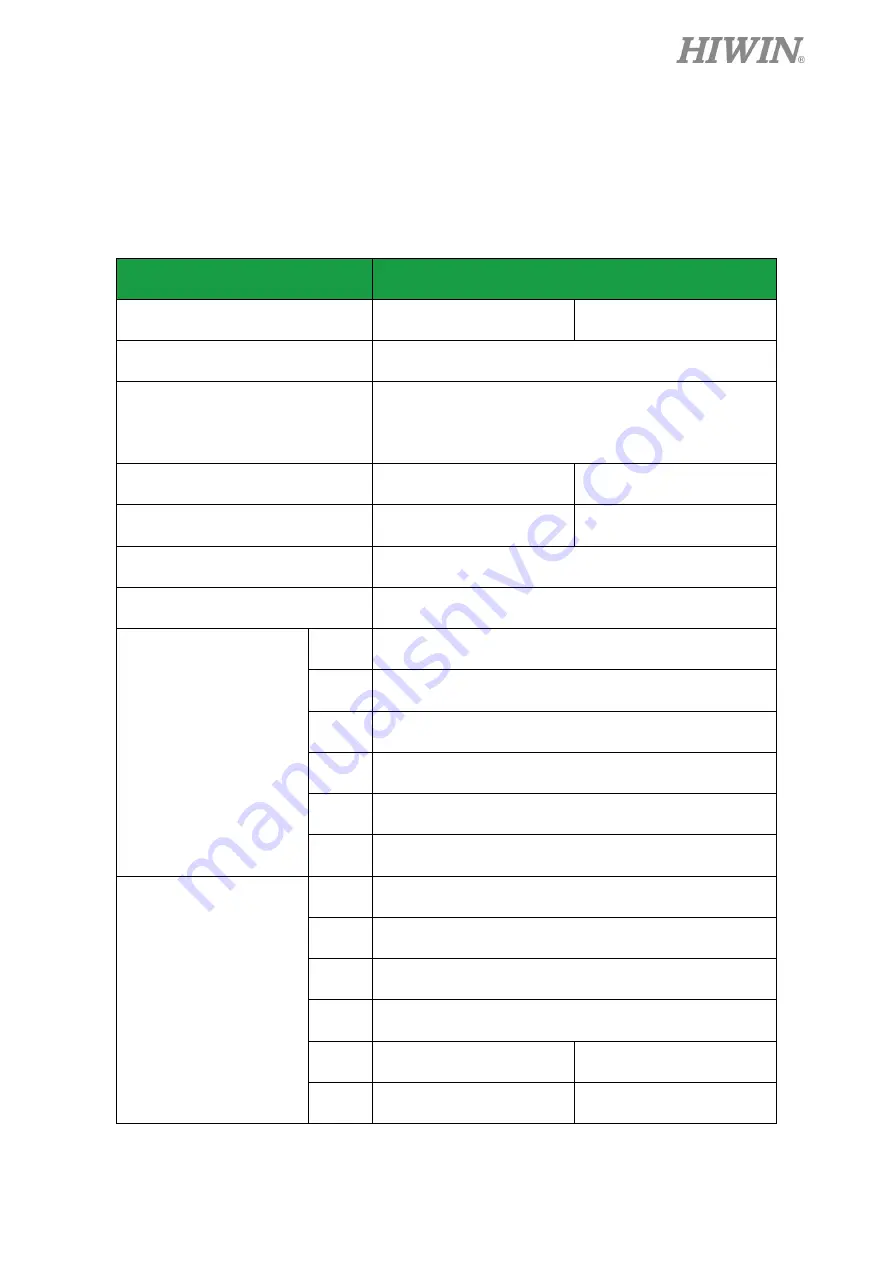
31
C08UE001-1912
2.3
Robot Specifications
The robot specifications are as shown in Table 2-2
Table 2-2 Robot specifications
Item
Specification
Model No.
RA620-1739
RA620-1621
Degrees of Freedom
6
Installation
Floor
(wall mounting, ceiling mounting) [*1]
Load capacity
20kg [*2]
30kg[*2]
Maximum reach radius
1739 mm
1621mm
Cycle time
0.9 s [*3]
Position
Repeatability
±0.06 mm
Motion range
J1
±180°
J2
+100°~-135°
J3
+190°~-80°
J4
±200°
J5
±130°
J6
±360°
Maximum speed
J1
231°/ s
J2
210°/ s
J3
205°/ s
J4
360°/ s
J5
420°/ s
210°/ s
J6
720°/ s
360°/ s
Summary of Contents for RA620-1621
Page 1: ...www hiwin tw User Manual Articulated Robot RA620 Original Instruction...
Page 35: ...34 C08UE001 1912 Figure 2 3 Outer dimension and motion range RA620 1621 J1 0 deg...
Page 37: ...36 C08UE001 1912 Figure 2 5 Wrist load diagram RA620 1621...
Page 54: ...53 C08UE001 1912 Table 5 3 Inspection schedule...