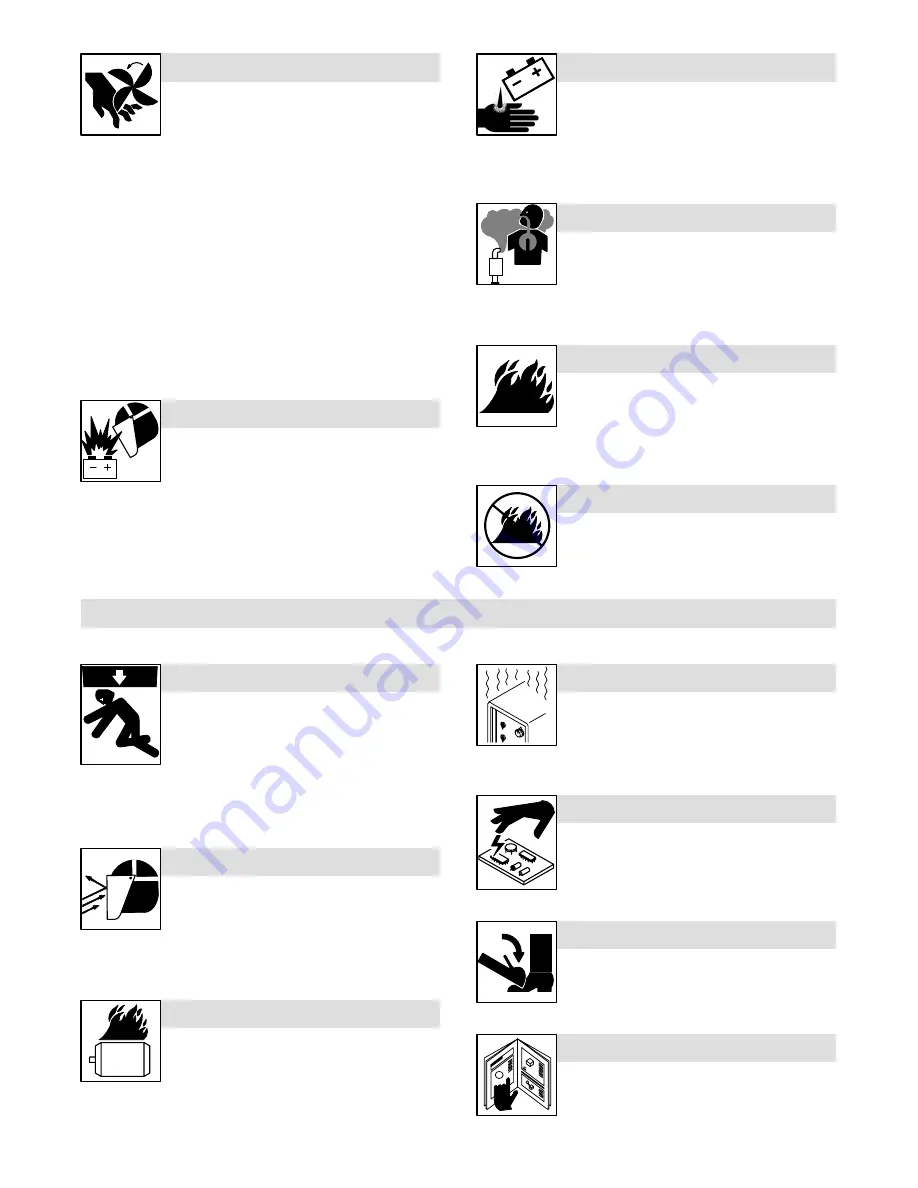
OM-494 Page 3
MOVING PARTS can cause injury.
Keep away from fans, belts, and rotors.
Keep all doors, panels, covers, and guards
closed and securely in place.
Stop engine before installing or connecting unit.
Have only qualified people remove guards or covers for maint-
enance and troubleshooting as necessary.
To prevent accidental starting during servicing, disconnect
negative (–) battery cable from battery.
Keep hands, hair, loose clothing, and tools away from moving
parts.
Reinstall panels or guards and close doors when servicing is
finished and before starting engine.
Before working on generator, remove spark plugs or injectors to
keep engine from kicking back or starting.
Block flywheel so that it will not turn while working on generator
components.
BATTERY EXPLOSION can BLIND.
Always wear a face shield, rubber gloves, and
protective clothing when working on a battery.
Stop engine before disconnecting or connect-
ing battery cables or servicing battery.
Do not allow tools to cause sparks when working on a battery.
Do not use welder to charge batteries or jump start vehicles.
Observe correct polarity (+ and –) on batteries.
Disconnect negative (–) cable first and connect it last.
BATTERY ACID can BURN SKIN and
EYES.
Do not tip battery.
Replace damaged battery.
Flush eyes and skin immediately with water.
ENGINE EXHAUST GASES can kill.
Use equipment outside in open, well-ventilated
areas.
If used in a closed area, vent engine exhaust
outside and away from any building air intakes.
ENGINE HEAT can cause fire.
Do not locate unit on, over, or near combustible
surfaces or flammables.
Keep exhaust and exhaust pipes way from
flammables.
EXHAUST SPARKS can cause fire.
Do not let engine exhaust sparks cause fire.
Use approved engine exhaust spark arrestor in
required areas – see applicable codes.
1-4.
Additional Symbols For Installation, Operation, And Maintenance
FALLING UNIT can cause injury.
Use lifting eye to lift unit only, NOT running
gear, gas cylinders, trailer, or any other
accessories.
Use equipment of adequate capacity to lift and
support unit.
If using lift forks to move unit, be sure forks are long enough to
extend beyond opposite side of unit.
FLYING SPARKS can cause injury.
Wear a face shield to protect eyes and face.
Shape tungsten electrode only on grinder with
proper guards in a safe location wearing proper
face, hand, and body protection.
Sparks can cause fires — keep flammables away.
OVERHEATING can damage motors.
Turn off or unplug equipment before starting or
stopping engine.
Do not let low voltage and frequency caused by
low engine speed damage electric motors.
Do not connect 50 or 60 Hertz motors to the 100 Hertz receptacle
where applicable.
OVERUSE can cause OVERHEATING.
Allow cooling period; follow rated duty cycle.
Reduce current or reduce duty cycle before
starting to weld again.
Do not block or filter airflow to unit.
STATIC (ESD) can damage PC boards.
Put on grounded wrist strap BEFORE handling
boards or parts.
Use proper static-proof bags and boxes to
store, move, or ship PC boards.
TILTING OF TRAILER can cause injury.
Use tongue jack or blocks to support weight.
Properly install welding generator onto trailer
according to instructions supplied with trailer.
READ INSTRUCTIONS.
Use only genuine MILLER replacement parts.
Perform engine maintenance and service
according to this manual and the engine
manual.
Summary of Contents for Hobart 300/300
Page 4: ......
Page 38: ...OM 494 Page 34 7 2 Maintenance Label ...
Page 49: ...OM 494 Page 45 Notes ...
Page 50: ...OM 494 Page 46 SECTION 8 ELECTRICAL DIAGRAMS Figure 8 1 Circuit Diagram For Welding Generator ...
Page 51: ...OM 494 Page 47 ST 192 298 F ...
Page 74: ...Notes ...